El sistema Kanban - 看板 (del japonés, kan = 'visual', ban = 'etiqueta') es una herramienta para el control del flujo pull desacoplado, que proporciona la gestión de los materiales directamente desde el taller, es decir, el área donde sucede la producción. En teoría, no requiere ningún software para su gestión, aunque hoy en día casi siempre se asocia a un programa informático con el fin de lograr un mayor control, flexibilidad y reducción de las actividades sin valor.
En concreto, el kanban adopta la forma de una etiqueta pegada a un contenedor que comunica la demanda de material a los proveedores, internos o externos. La etiqueta contiene la información más importante sobre el material y el contenedor al que está vinculada: por ejemplo, el código del producto, la descripción, el proveedor del que viene, el cliente a destino, la cantidad y el plazo de entrega.
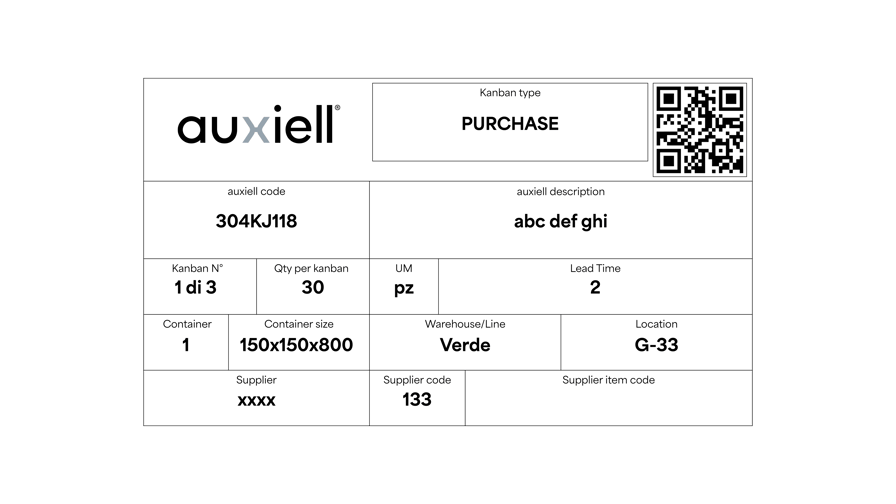
Suele utilizarse en tres ámbitos:
- kanban de compra: se utiliza para solicitar la compra del código al proveedor;
- kanban de producción: sirve para solicitar la producción del código a la fase anterior a la que está conectado.
- kanban de movimiento: se utiliza para tomar y trasladar material desde un almacén centralizado hasta el lugar de uso.
Conceptos preliminares: flujo desacoplado
Una de los métricos clave a la hora de rediseñar un proceso es el lead time, el intervalo de tiempo entre dos eventos. En particular, es importante comparar el plazo de entrega requerido por el cliente con el plazo de entrega del proceso:
- cuando el plazo de entrega requerido por el cliente es mayor que el plazo de entrega del proceso, ambos pueden sincronizarse y la transformación del flujo de productos tiene lugar en la misma secuencia que la demanda (flujo acoplado);
- cuando el plazo de entrega requerido por el cliente es inferior al plazo de entrega del proceso, debe desacoplarse de la demanda del cliente y la gestión de la producción del proceso debe realizarse mediante acumulación y almacenamiento (flujo desacoplado).
El kanban es una herramienta para controlar el flujo desacoplado.
Tamaño del Kanban
Para que el kanban sea efectivo es necesario dimensionarlo para cada código, analizando el número de contenedores que deben rotar (llenar, vaciar, ...) en el sistema.
De acuerdo a la teoría existen muchas fórmulas para hacer esto. La siguiente es probablemente la más sencilla y la más aplicable en la práctica:
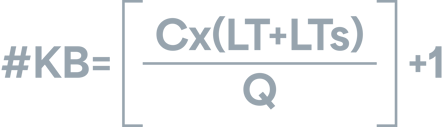
Donde:
- #KB es un número entero de contenedores, de ahí la necesidad de redondear la primera parte de la fórmula;
- Ces el consumo máximo durante el plazo de entrega del proceso -en piezas/unidades de tiempo (normalmente días)- que debe mantener el sistema. Un cálculo excesivo provocará un exceso de inventario, mientras que un cálculo insuficiente provocará una falta de inventario. Suponiendo que ningún kanban proteja contra los picos extremos de demanda, para determinar el C una buena práctica es partir de la serie histórica de consumo -posiblemente corregida con factores apropiados de aumento o reducción de precio y "recortado" a un determinado nivel de servicio- y obtener el promedio la media móvil en el plazo de reposición LT, para absorber las variaciones de la demanda a lo largo del período;
- LT es el tiempo de entrega de reposición, es decir, cuántos días tarda el proveedor interno o externo en reponer el componente en el supermercado;
- LTs es tiempo de entrega de seguridad, es decir, cuántos días extra de cobertura quiere tener para protegerse cualquier problema de suministro;
- Q es la cantidad de piezas por contenedor. En la práctica, un suministro kanban no es más que un punto de reorder -ROP=CxLT- dividido en muchos contenedores lo suficientemente pequeños como para facilitar la rotación del inventario y lo suficientemente grande como para que su manejo sea cómodo;
- El "+1" representa un contenedor extra que se añadirá al cálculo en función de que el primer Kanban se "desprenda" cuando se vacíe el primer contenedor. Sirve para mantener el proceso en marcha antes de que se restablezca el primer contenedor consumido.
Tipos de Kanban
Lote Kanban - lote de tarjetas
El lote de etiquetas, también llamado lote kanban, es un sistema que se utiliza cuando el reorden del material no puede realizarse según la cantidad indicada por la etiqueta individual. Esto puede depender de varios factores:
- necesidades de material durante el plazo de resurtimiento menor a comparación con el lote de producción económico del proveedor;
- número excesivo de pedidos que se desprenderían al proveedor con una liberación en cada etiqueta (costo del pedido, EOQ);
- necesidad de crear contenedores más pequeños y más numerosos (por ej. un mejor servicio de los códigos compartidos entre varias líneas) sin revisar parámetros de suministro como la cantidad mínima de reorden.
Señal kanban
La señal kanban implica una única etiqueta del resurtimiento, que se coloca en un nivel de existencias específico denominado punto de reorden. Cuando las existencias de material descienden por debajo del punto de reorden, se realiza una solicitud para restablecer el material.
La señal kanban puede utilizarse cuando:
- el lote de producción/compra es muy grande comparado con el consumo y no es posible intervenir para reducirlo;
- i#KB' es menor que 2, donde #KB' es el número de Kanban no redondeado al entero superior.
Doble contenedor (double bin)
Esta es la forma "más simple" de Kanban.
Este sistema se utiliza normalmente para códigos de bajo valor y alta rotación, donde el valor del inventario no justifica un redimensionamiento frecuente y suelen ser de gran tamaño.
Ventajas del sistema Kanban
Las ventajas de utilizar el sistema kanban son muchas:
- hace sea menos probable que se produzcan desabastecimientos;
- reduce significativamente los inventarios en comparación con la lógica push;
- permite respuestas rápidas a los cambios en la demanda;
- mejora la precisión de los inventarios;
- simplifica la programación, reduciendo el uso de MRP.