Il kanban system - 看板 (dal giapponese, kan = “visuale”, ban = “cartellino”) è uno strumento per il controllo del flusso pull disaccoppiato, che prevede una gestione dei materiali direttamente dallo shopfloor – cioè dall’area dove avviene la produzione. Nella teoria non necessita di alcun software per la sua gestione, anche se oggi quasi sempre gli si associa un programma informatico per poter ottenere maggior controllo, flessibilità e riduzione delle attività non a valore.
Concretamente il kanban si presenta come un cartellino applicato a un contenitore che comunica la domanda di materiale ai fornitori, interni o esterni. Il cartellino tipicamente riporta le informazioni più importanti relative al materiale e al contenitore a cui è associato: per esempio il codice del prodotto, la descrizione, il fornitore da cui arriva, il cliente a cui è destinato, la quantità e il lead time.
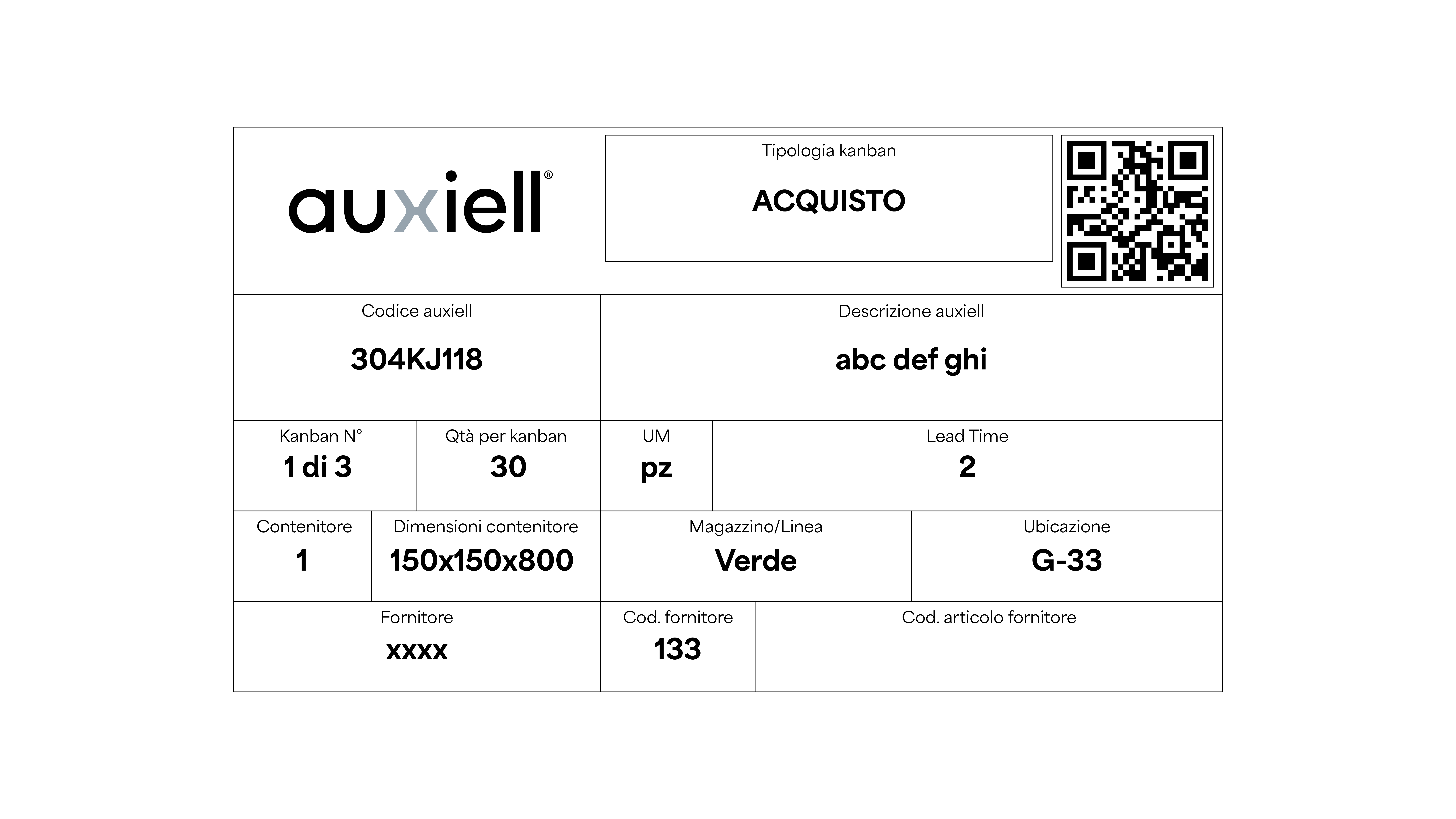
Solitamente viene utilizzato in tre ambiti:
- kanban di acquisto: utilizzato per richiedere l’acquisto del codice al fornitore;
- kanban di produzione: utilizzato per richiedere la produzione del codice alla fase a monte a cui è collegato;
- kanban di movimentazione: utilizzato per prelevare e spostare materiale da un magazzino centralizzato al luogo di utilizzo.
Concetti preliminari: flusso disaccoppiato
Una delle metriche fondamentali quando si riprogetta un processo è il lead time, ovvero l'intervallo di tempo tra due eventi. In particolar modo è importante mettere a confronto il lead time richiesto dal cliente con quello di processo:
- quando il lead time richiesto dal cliente è superiore al lead time di processo i due possono essere sincronizzati e il flusso di trasformazione dei beni avvenire nella stessa sequenza della domanda (flusso accoppiato);
- quando il lead time richiesto dal cliente è inferiore al lead time di processo quest’ultimo deve essere disaccoppiato dalla domanda del cliente e la gestione degli output del processo avvenire tramite accumuli e scorte (flusso disaccoppiato).
Il kanban è uno strumento per il controllo del flusso disaccoppiato.
Dimensionare il kanban
Affinché il kanban sia efficace è necessario dimensionarlo determinando per ogni codice oggetto di analisi il numero di contenitori che devono ruotare (svuotarsi, riempirsi, svuotarsi, …) nel sistema.
In letteratura esistono molteplici formule per farlo. Quella che segue è probabilmente la più semplice e di più concreta applicazione:
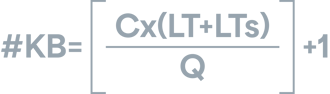
Dove:
- #KB è un numero intero di contenitori, da cui la necessità di arrotondare per eccesso la prima parte della formula;
- C è il consumo massimo durante il lead time di processo – in pezzi/unità di tempo (tipicamente giorni) - che il sistema dovrà sostenere. Un consumo sovrastimato comporterà scorte eccessive, mentre un consumo più basso del necessario porterà a stock-out. Partendo dal presupposto che nessun kanban metterà al riparo da picchi estremi della domanda, per determinare C una buona prassi è quella di partire dalla serie storica dei consumi – eventualmente corretta con opportuni coefficienti di maggiorazione o riduzione e “tagliata” a un certo livello di servizio – e ricavarne la media mobile nel lead time LT di riapprovvigionamento, così da assorbire le variazioni di domanda nel periodo;
- LT è il lead time di riapprovvigionamento, ovvero quanti giorni sono necessari al fornitore interno o esterno per ripristinare il componente a supermarket;
- LTS è il lead time di sicurezza, ovvero quanti giorni di copertura aggiuntivi si desidera avere per tutelarsi da eventuali problemi di fornitura;
- Q è la quantità di pezzi per ogni contenitore. Nella pratica, infatti, una scorta a kanban non è altro che un reorder point – ROP=CxLT – suddiviso in tanti contenitori sufficientemente piccoli per favorire la rotazione delle giacenze e sufficientemente grandi da rendere conveniente la movimentazione;
- Il “+1” rappresenta un contenitore extra da aggiungere al dimensionamento in funzione del fatto che il primo kanban verrà “staccato” allo svuotarsi del primo contenitore. Serve a mantenere alimentato il processo prima che il primo contenitore consumato venga ripristinato.
Tipologie di kanban
Kanban batch – lotto di cartellini
Il lotto di cartellini, detto anche kanban batch, è un sistema utilizzato quando il riordino del materiale non può avvenire secondo la quantità indicata dal singolo cartellino. Ciò può dipendere da molteplici fattori:
- fabbisogno di materiale durante il lead time di ripristino troppo basso rispetto al lotto economico di produzione del fornitore;
- eccessivo numero di ordini che si staccherebbero al fornitore con un rilascio a ogni cartellino (costo ordine, EOQ);
- esigenza di creare contenitori più piccoli e numerosi (es. miglior asservimento di codici condivisi fra più linee) senza rivedere i parametri di fornitura come la quantità minima di riordino.
Signal kanban
Il signal kanban prevede un unico cartellino di ripristino, che viene posizionato a un determinato livello di scorta detto punto di riordino - reorder point. Quando la giacenza del materiale scende al di sotto del reorder point viene effettuata la richiesta di ripristino del materiale.
Il signal kanban può essere utilizzato quando:
- il lotto di produzione/acquisto è molto grande rispetto ai consumi e non è possibile intervenire per ridurlo;
- se #KB’ è minore di 2, dove #KB’ è il numero di kanban non arrotondato all’intero superiore.
Double bin
È la forma più “semplice” di kanban. Si compone di due contenitori ed è caratterizzato dall’assenza di un vero e proprio flusso informativo - il contenitore vuoto costituisce ordine di ripristino.
Questo sistema è utilizzato tipicamente per codici a basso valore e alta rotazione, dove il valore della giacenza non giustifica frequenti ridimensionamenti ed è solitamente sovradimensionata.
Vantaggi del kanban system
I vantaggi dell’utilizzo del sistema kanban sono molteplici:
- rende meno probabili le rotture di stock;
- riduce notevolmente le scorte rispetto alla logica push;
- permette risposte veloci ai cambiamenti della domanda;
- migliora l’accuratezza della scorta;
- semplifica la programmazione, riducendo l’uso dell’MRP.