Portfolio
ABS
Intro
Come è stato possibile migliorare la competitività grazie a una visione sistemica dei processi e all’allineamento con la domanda
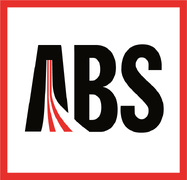
Settore
Sede
Performance
raggiunte
Produttività
media giornaliera
Performance
raggiunte
puntualità (LOTP)
riduzione stock su tutta la linea
Vuoi migliorare le performance della tua azienda?
Storia
azienda
1988
ABS nasce nel 1988 dalla fusione di due acciaierie di lunga esperienza e alta qualificazione: le Officine Bertoli, fondate nel 1813, e Safau, le cui origini risalgono al 1934. Da allora rappresenta la divisione Steelmaking del Gruppo Danieli.
Oggi
ABS è specializzata nella produzione di acciai lunghi speciali, una tipologia di prodotti ad alta specializzazione per settori che richiedono prestazioni di qualità elevata e applicazioni tecniche e meccaniche avanzate. La produzione utilizza interamente il ciclo del rottame che riduce le emissioni del 65% rispetto al ciclo con altoforno. ABS è fornitore di importanti filiere in costante innovazione come l'Automotive, la Power Generation Wind e Oil & Gas.
Dipendenti (2024)
0Fatturato (2024)
0EBITDA (2024)
0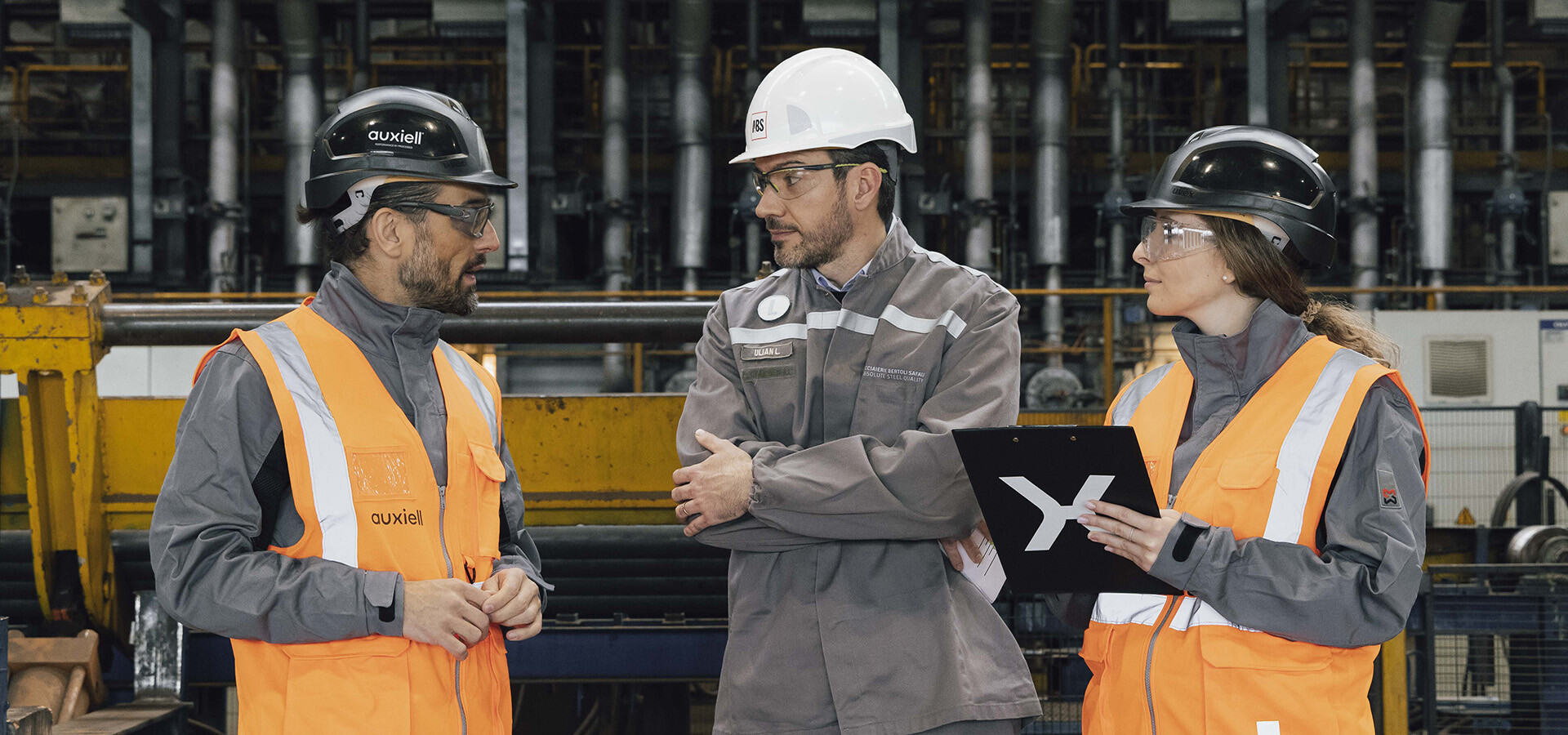
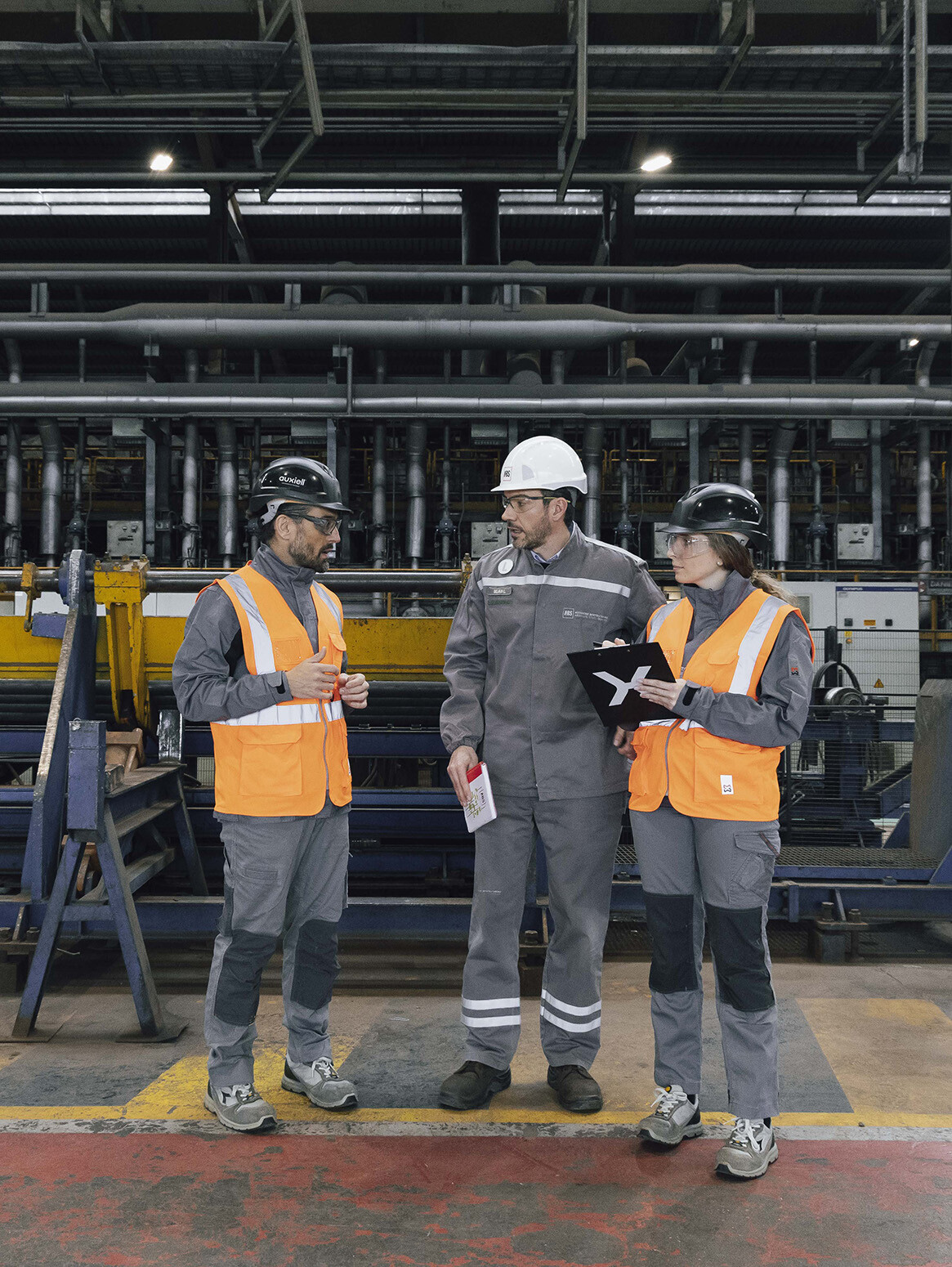
La sfida di ABS
ABS si è rivolta al nostro team per ricercare un valido supporto nell'acquisizione di una visione sistemica dei propri processi produttivi. L'obiettivo è stato quello di sostenere la crescita del business attraverso la creazione di processi di fornitura e produzione best-in-class collegati ai bisogni reali degli specifici clienti.
Il punto di partenza
La trasformazione del primo macro-processo: Delivery
2022
Anno avvio collaborazione
con auxiell
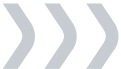
Il progetto continua
Con ABS abbiamo inizialmente intrapreso un progetto sul macro-processo di Delivery che comprende produzione, supply chain e gestione degli ordini.
SCAN
Lean Gap Analysis® in Delivery
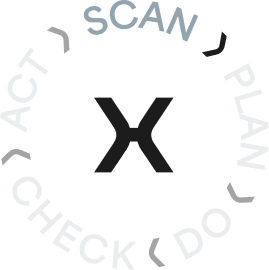
Per analizzare lo stato corrente dei processi il team auxiell-ABS si è impegnato nella Lean Gap Analysis® dell'intera value stream Luna: processo che partendo dal rottame produce barre con diverse finiture. La mappatura ha riguardato tutto il processo, dalla produzione in acciaieria fino alla consegna del prodotto finito al cliente. Gli sprechi e le relative opportunità di miglioramento emersi hanno riguardato acciaieria (dalla fusione del rottame fino alla creazione del blumo), laminatoio e finiture.
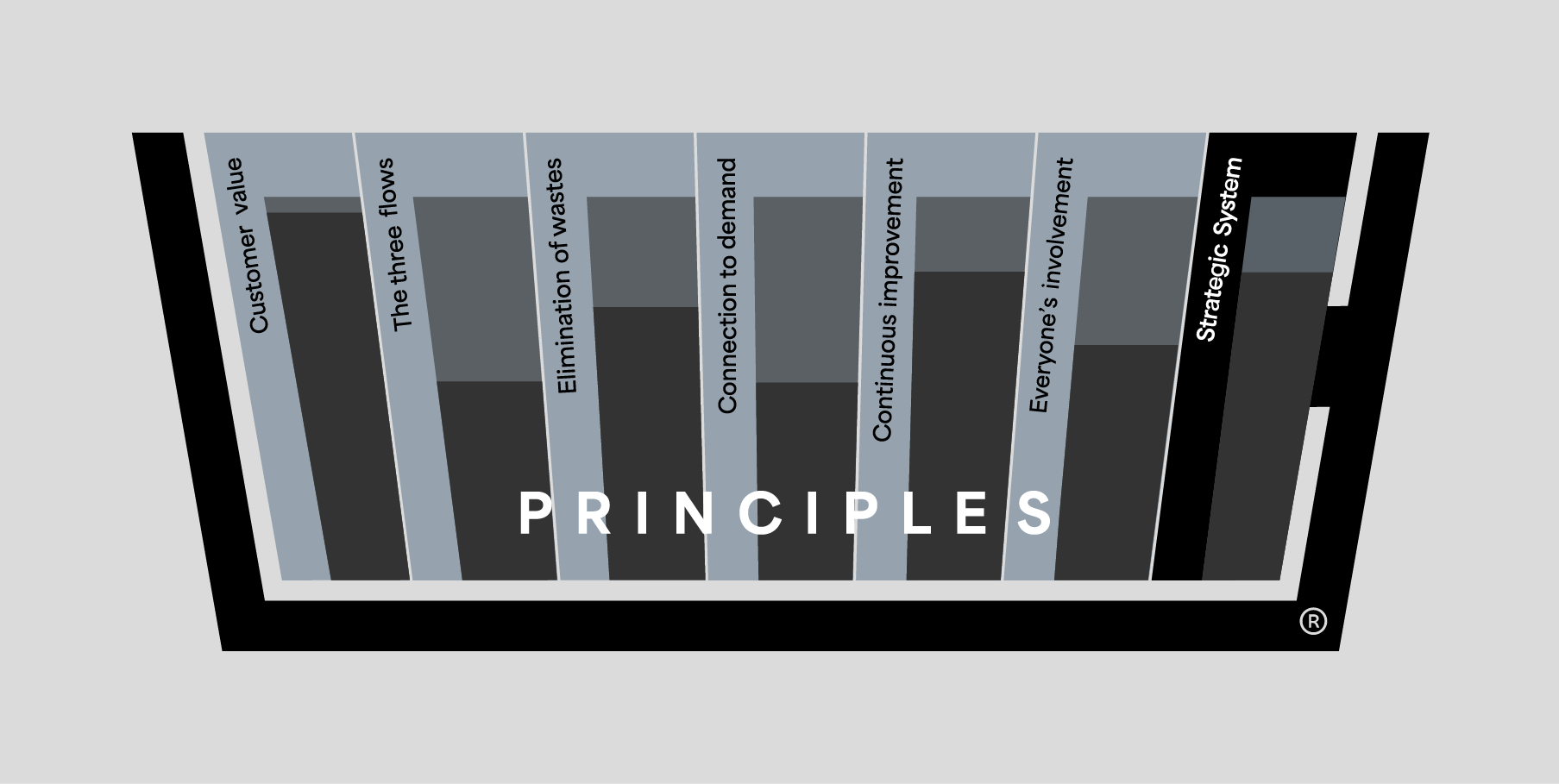
Tempi di consegna al cliente non conformi
L’elevato volume di materiali in work-in-progress e la struttura produttiva caratterizzata da limitata flessibilità incidevano sui lead time complessivi del processo.
Variabilità nelle performance di consegna
Scostamenti rispetto alle tempistiche previste, con impatto sulla percezione del livello di servizio da parte dei clienti.
Gestione dei materiali in WIP tra le diverse fasi del processo
L’organizzazione dei flussi di finitura secondo un modello “a lotti e code” portava a un accumulo di scorte non sempre ottimizzato nei punti di discontinuità del processo, in particolare tra acciaieria e laminatoio e nelle fasi successive. Questo fenomeno era influenzato dal disallineamento delle capacità produttive delle singole fasi.
Efficienza di fase
Il focus era nell'efficientamento del costo di ogni singola fase e mancava una visione di processo end-to-end.
Decisioni prese sulla base di indicatori di fase
L'assenza di indicatori di processo limitava la possibilità di supportare le scelte legate al flusso.
PLAN
Lean RoadMap® in Delivery
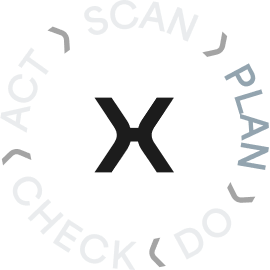
Questi i punti di partenza alla base della fase successiva del progetto, ossia quella di PLAN. Attraverso la Lean RoadMap® abbiamo definito la sequenza di implementazione delle più corrette tecniche lean che ci permettessero di raggiungere gli obiettivi concordati con il team ABS. Nello specifico, il team di lavoro si è concentrato su:
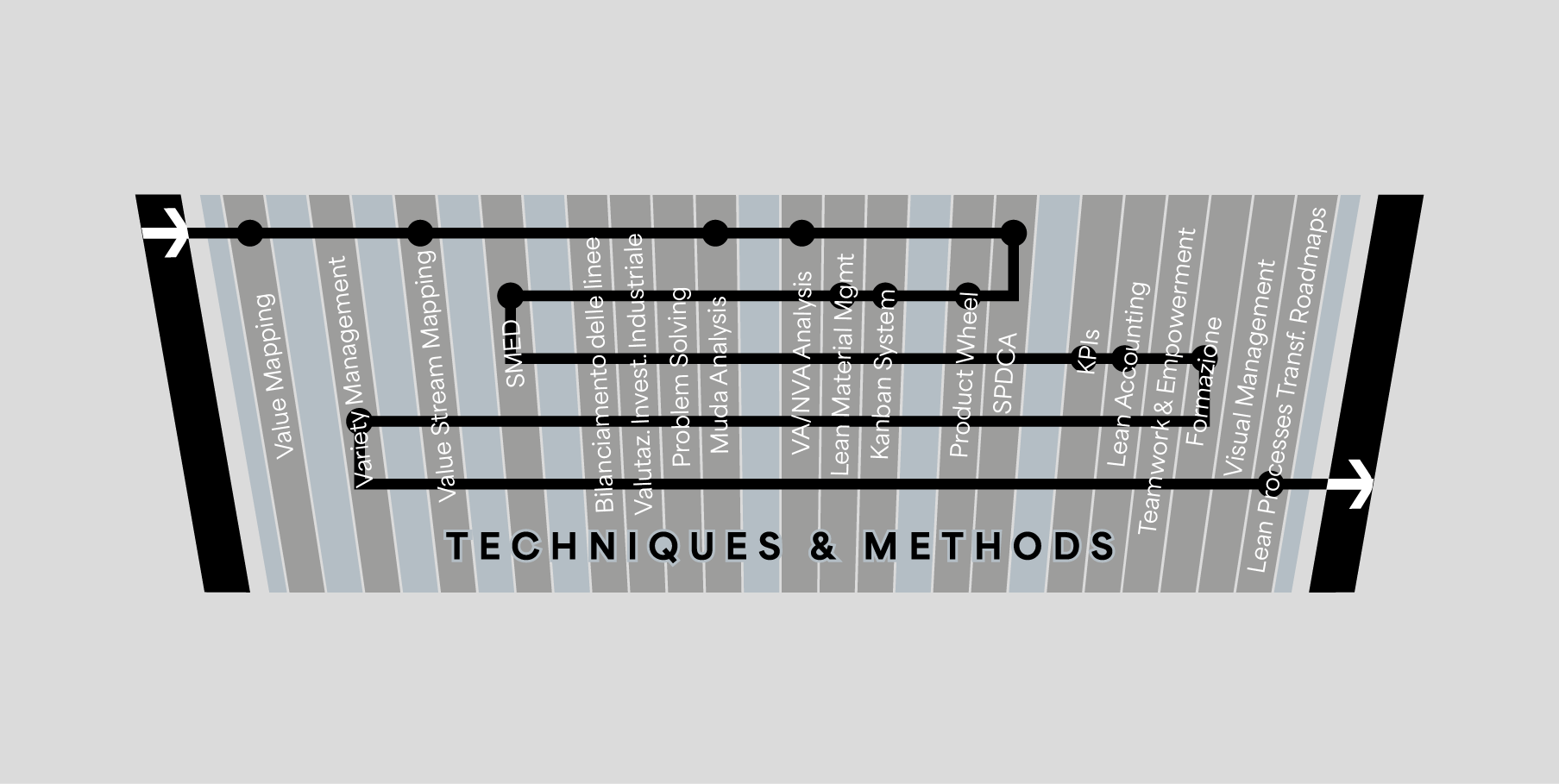
Aggiornamento della Product Wheel del laminatoio
Per aumentare il collegamento alla domanda e la flessibilità di produzione.
Revisione dell'organizzazione di collaudi e laboratori secondo la logica pull
Per far sì che i collaudi - effettuati da chi verifica i parametri di processo e qualità - e i laboratori - in cui vengono fatte le analisi di qualità dei prodotti - venissero gestiti più efficientemente e con tempistiche ridotte.
Introduzione di un sistema pull di gestione della produzione
Per ridurre il lead time di processo e ridimensionare la capacità produttiva di ogni fase al fine di evitare "code", ossia materiale in giacenza in attesa davanti ogni fase.
Revisione KPI di processo
Per renderli maggiormente esaustivi e collegati tra loro e al bisogno del cliente.
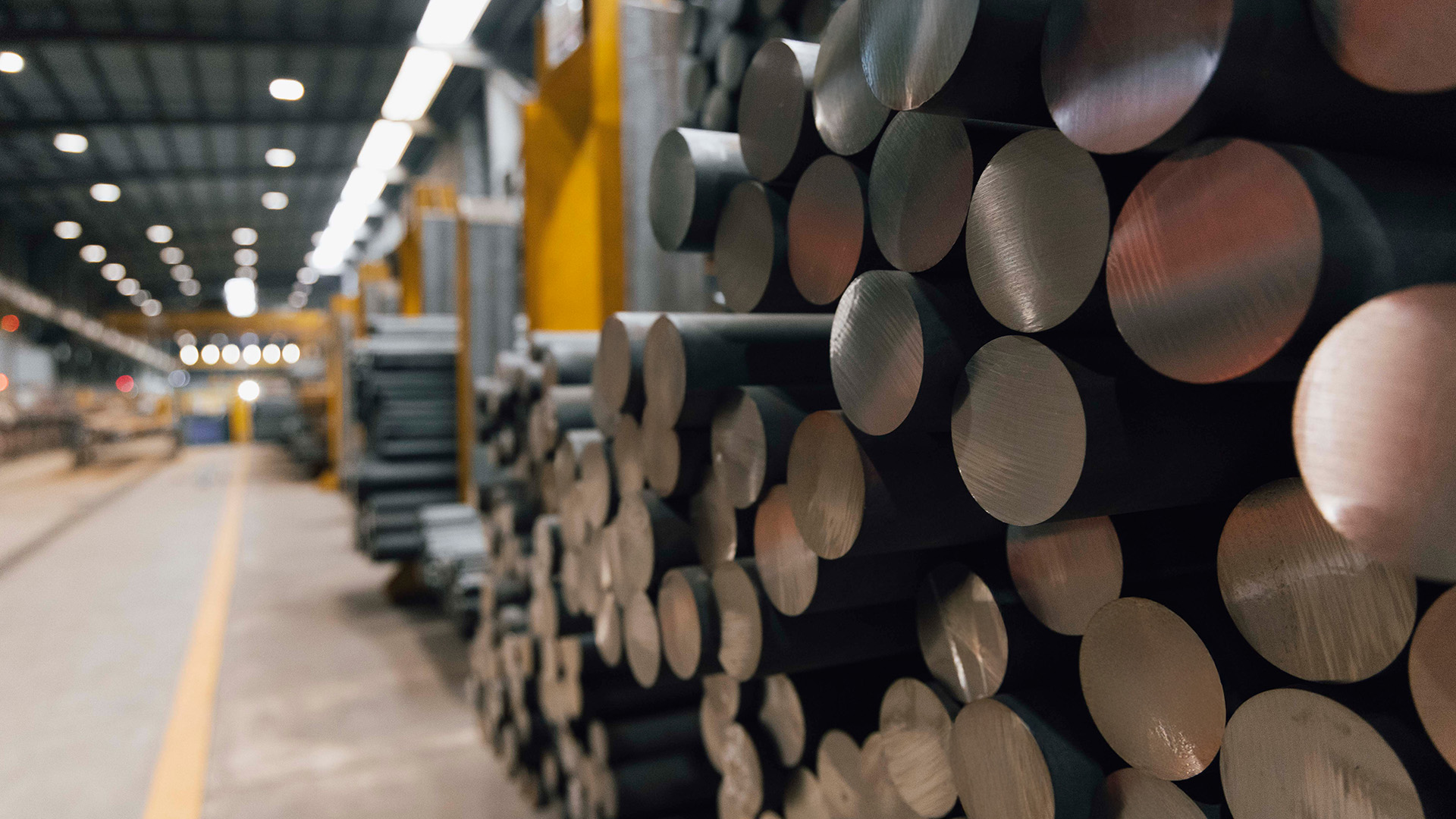
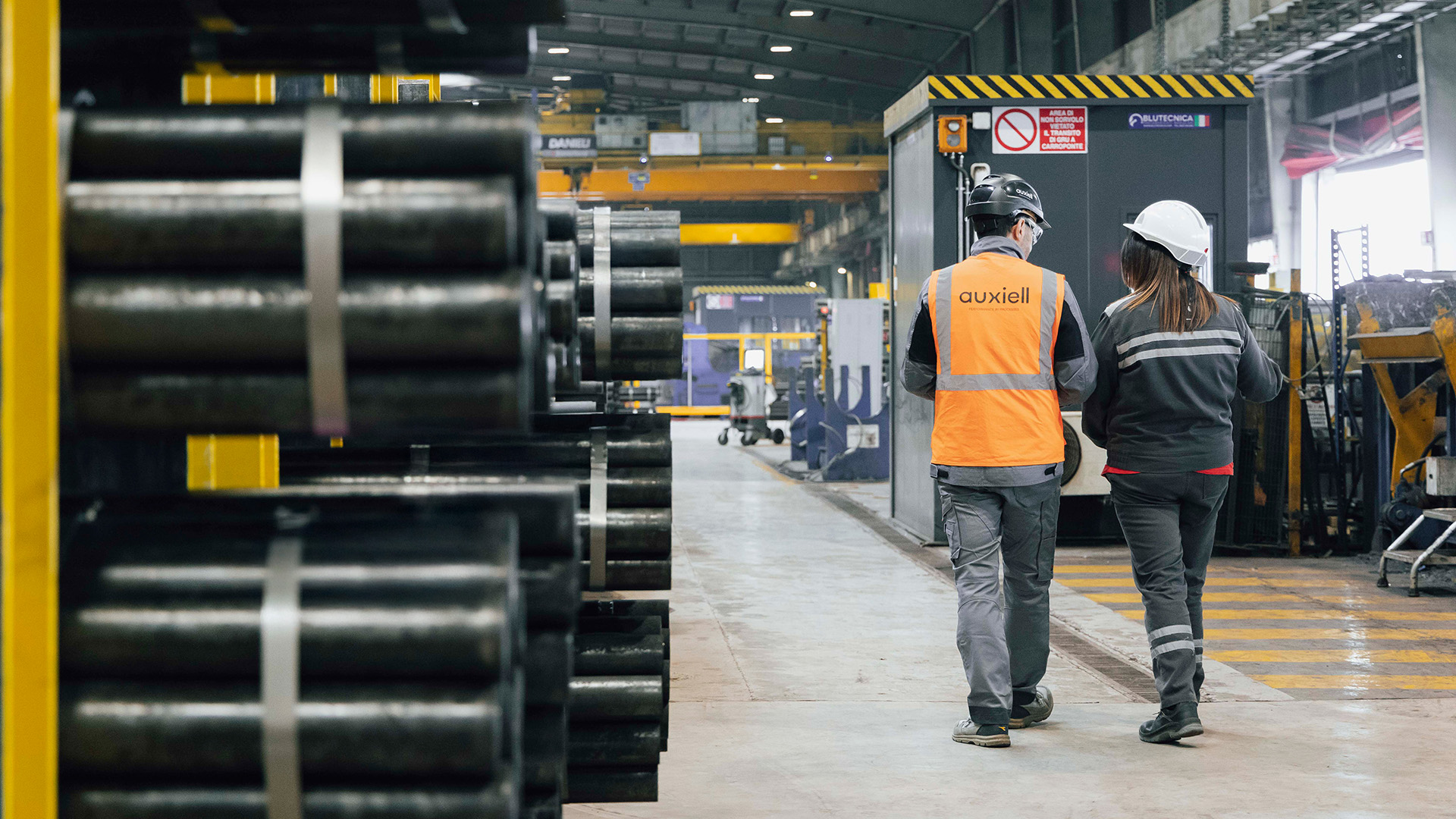
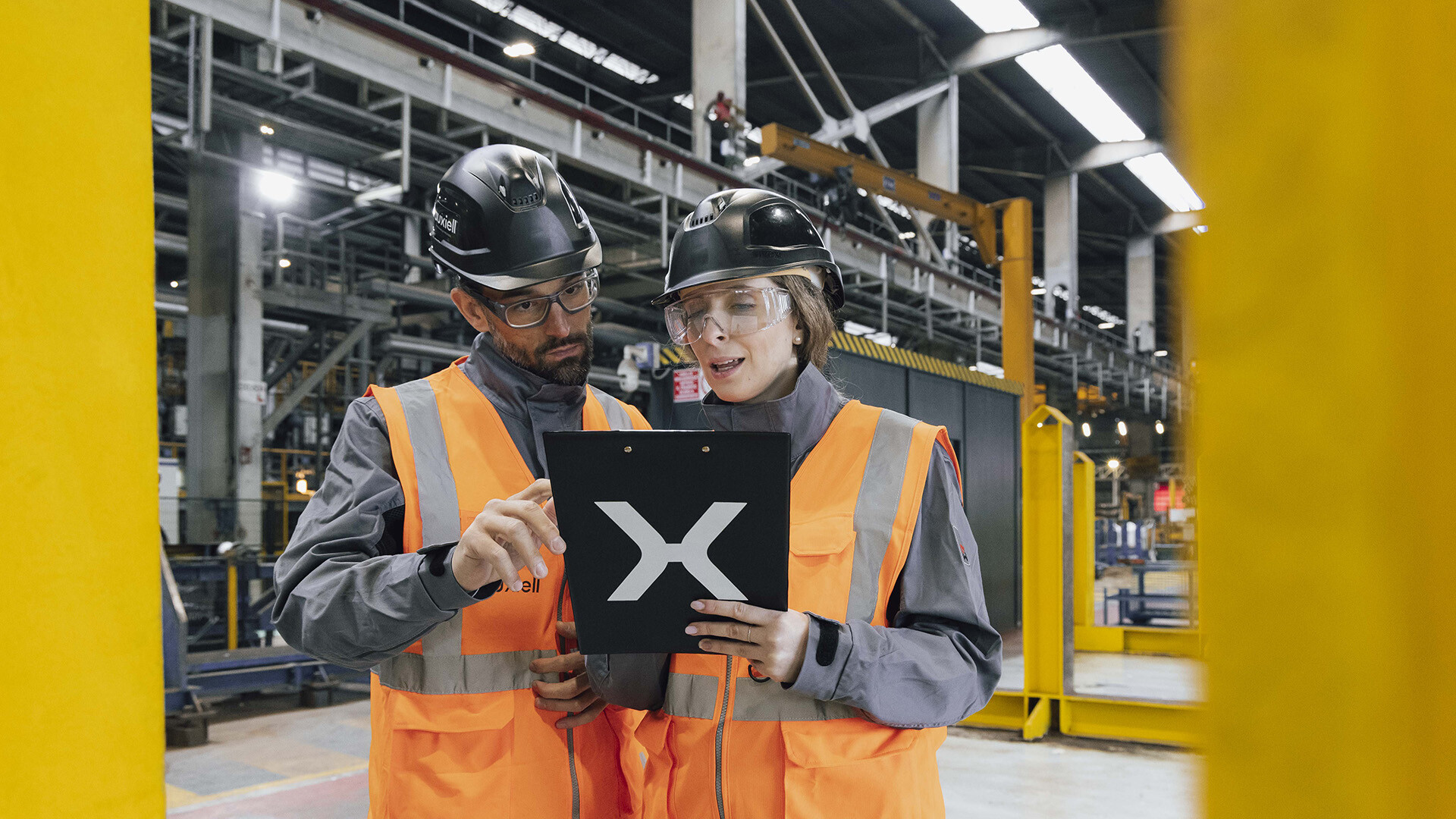
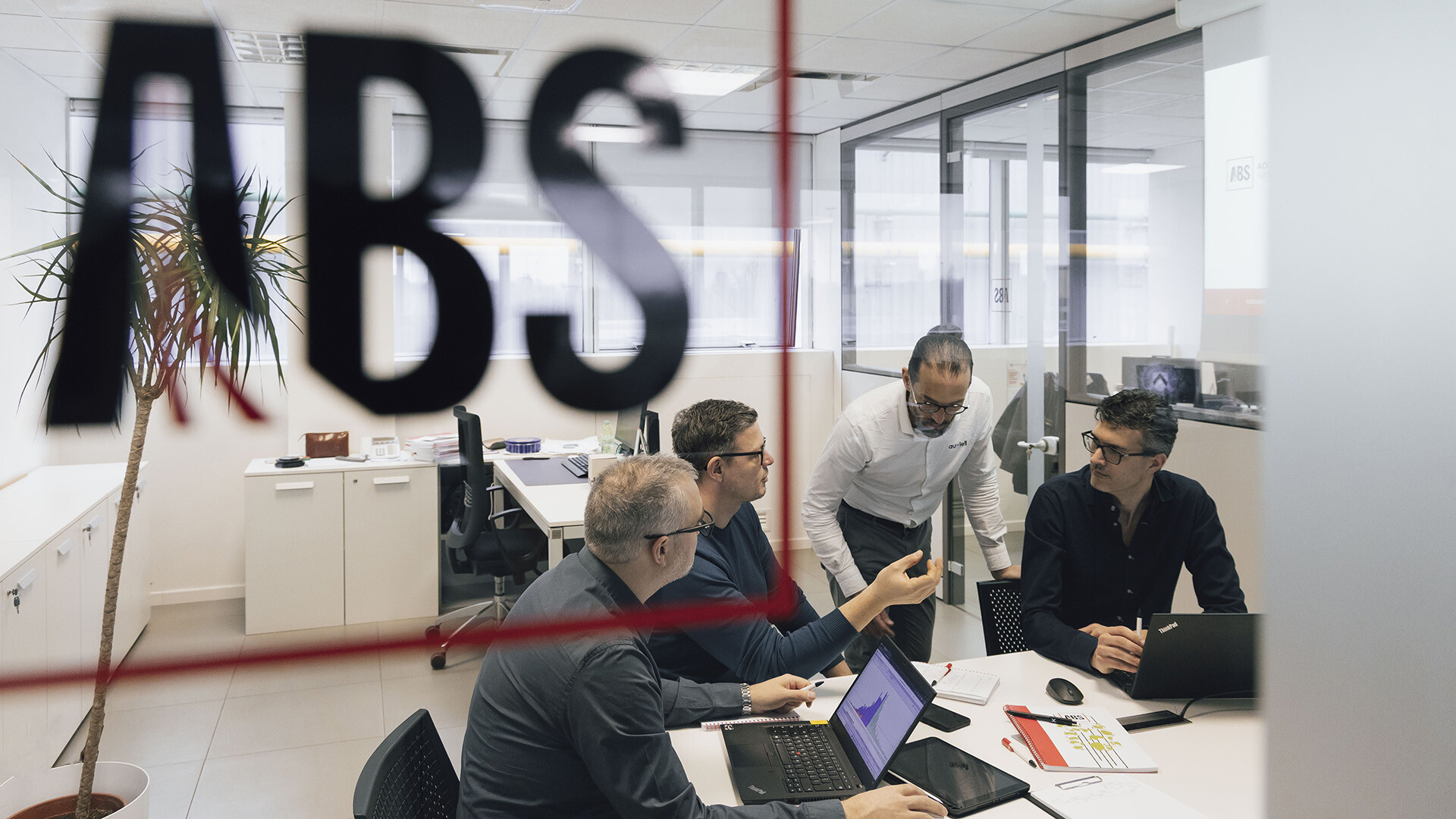
DO
Delivery Overall Transformation
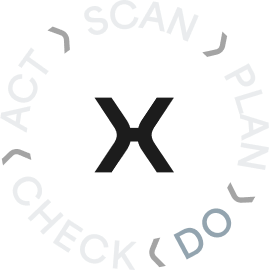
Quali attività e tecniche lean ci hanno permesso di raggiungere l’obiettivo stabilito?
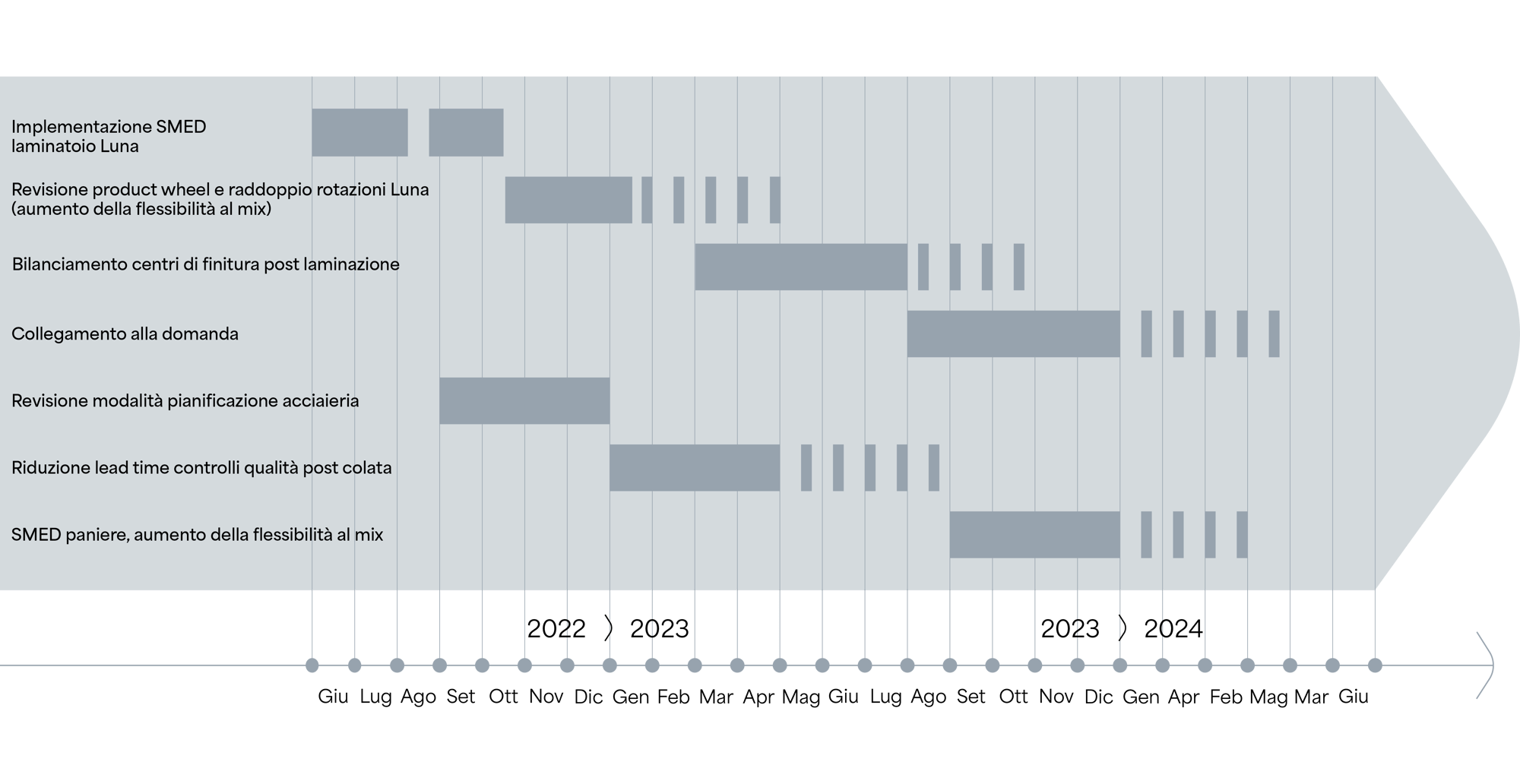
Collegamento alla domanda e alla product wheel del laminatoio
Lavorando con produzione e controllo qualità da un lato e forza commerciale e team di pianificazione dall'altro sono state stabilite le migliori azioni da implementare per capire a fondo quali potessero essere i bisogni reali dei clienti. Con il supporto di edxiting è stato organizzato un workshop - lo Steel Game - dedicato all'identificazione dei bisogni dei clienti e al collegamento alla domanda. Una volta creati con ABS i modelli di risposta al mercato abbiamo coinvolto direttamente i clienti nel progetto definendo con loro - nel massimo livello di dettaglio - le azioni e gli strumenti per rispondere alle richieste. Sulla produzione l'effetto è stato quello di livellarla grazie a un miglior collegamento alla domanda mediante l'utilizzo del kanban con alcuni clienti selezionati. Grazie alla visibilità della Product Wheel, alcuni clienti hanno avuto l'opportunità di operare in logica di 'prenotazione della capacità produttiva', potendo riservare uno specifico slot per i loro ordini. Questo approccio ha permesso di testare e ottimizzare il sistema, con potenziali benefici estendibili in futuro.
Revisione in ottica pull del flusso delle finiture
L'intero processo produttivo è stato rivisto andando a identificare i diversi colli di bottiglia per eliminarli in modo da garantire il flusso nelle fasi di finitura evitando interruzioni o aumento delle code.
Problem solving esteso: miglioramento della puntualità e riduzione dello stock
Con un team multifunzionale - pianificazione, produzione, qualità, commerciale - attraverso l'applicazione della tecnica del problem solving sono state indagate le cause radice degli ostacoli allo scorrere del flusso ed è stato definito un set di azioni che portassero un impatto diretto sulla puntualità e sullo stock. Due aspetti in particolare sono stati rivisti:
1. Le logiche e i parametri di pianificazione in acciaieria, laminatoio e finiture.
2. Il collegamento delle fasi del processo per abbassare scorte, ridurre il lead time e migliorare la produttività.
Revisione KPI di processo
Partendo dagli indicatori già utilizzati in ABS si è andati ad analizzare cosa fosse a valore per il cliente, passando da KPI di fase a KPI di processo. Nello specifico è stato rivisto il Lean on Time Production (LOTP) - puntualità sulla data di fine produzione stabilita - e sono stati introdotti altri due indicatori:
1. Shipped on Time (SOT) per misurare - concluso il processo di lavorazione - il rispetto della data di spedizione del prodotto finito al cliente
2. Lean on Time Delivery (LOTD) per monitorare l'arrivo del materiale al cliente.
Questa attività è stata interamente svolta a quattro mani con il team ABS composto da figure afferenti a diverse aree aziendali - dal direttore commerciale allo sviluppo del business, dalla logistica alla pianificazione.
Gestione in pull delle prove di laboratorio e dei collaudi
La fase di collaudo è stata messa a flusso rendendo visibile al laboratorio i campioni tagliati, individuando dei momenti fissi di prelievo dei campioni da parte degli operatori di laboratorio che eseguivano i test e pubblicavano i risultati entro un giorno (dai 4 giorni iniziali). Sono stati ridefiniti i flussi operativi del laboratorio ed è stato implementato il milkrun di prelievo dei provini in logica pull - rendendolo poka yoke - e riducendo così anche il lead time dei test metallografici in laboratorio. Un'ulteriore attività di miglioramento ha riguardato il processo di emissione del certificato di qualità del prodotto: è stato rivisto il flusso informativo collegando la fase di approntamento del materiale (in attesa di essere spedito) alle priorità di emissione dei certificati.
Pianificazione degli ordini di produzione dell'acciaieria con orizzonti variabili
Per abbassare lo stock tra acciaieria e laminatoio e i parchi a valle del laminatoio è stato ridotto l’orizzonte di programmazione: inizialmente veniva considerato un orizzonte temporale di 5 settimane. In prima istanza gli articoli sono stati classificati sulla base dei volumi e della frequenza di consumo grazie alla tecnica ABC-RRS (tecnica di analisi che si applica in fase di scan e plan). La proposta è stata quella di lavorare con un orizzonte differenziato sulla base della rotazione dell’articolo: 3 settimane su articoli alto rotanti [runners] (consumati per almeno 80% delle settimane nel periodo analizzato) mentre 4 settimane sui medio rotanti [repeaters] e 5 settimane sui basso rotanti [strangers] (consumati per meno del 15% delle settimane nel periodo analizzato). La classificazione è stata poi inserita nel sistema gestionale in modo da pianificare la produzione degli ordini sulla base delle tempistiche previste per ogni categoria.
CHECK
Abbiamo raggiunto gli obiettivi stabiliti?
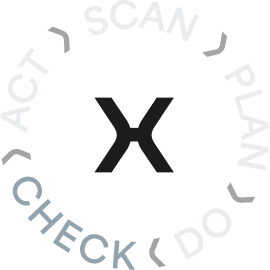
La puntualità è aumentata del 7% LOTP - in target rispetto al valore stabilito inizialmente
Le giacenze di semilavorati e prodotto finito sono diminuite del 17%
A livello di team sono state avviate diverse attività di problem solving che si autoalimentano e il gruppo rimane costantemente coinvolto nel migliorare in autonomia i processi
Il coinvolgimento delle prime linee dei team commerciale/logistica/produzione/controllo di gestione ha permesso di organizzare meeting settimanali sui progetti in modo tale da agire prontamente in caso di scostamenti dal target
Il team ragiona per processo e non in ottica di costi della singola fase tanto da optare, in alcuni casi, per soluzioni che prevedono un aumento dei costi della singola fase a fronte di una riduzione di quelli di processo
I benefici raggiunti hanno influenzato positivamente il team. Le persone, che si sono rese da subito disponibili dimostrando una notevole propensione al cambiamento, hanno accolto il progetto con entusiasmo. Sono le persone a portare i risultati e solo cambiando il loro comportamento è possibile avere successo nella trasformazione: questa è la vera differenza tra essere lean e fare lean.
Dal punto vendita pilota a tutto il canale di vendita
Il metodo acquisito della riprogettazione del punto vendita pilota ha consentito al management e al team interno di miglioramento di acquisire consapevolezza sui benefici qualitativi e quantitativi della trasformazione Lean. Questo ci ha portato a costruire uno standard Aspiag per l'analisi e la riprogettazione di tutti i processi dei punti vendita e ha consentito di avviare l'estensione dei miglioramenti portati all'interno del punto vendita pilota a tutti i punti vendita del canale in un percorso della durata di 3 anni.
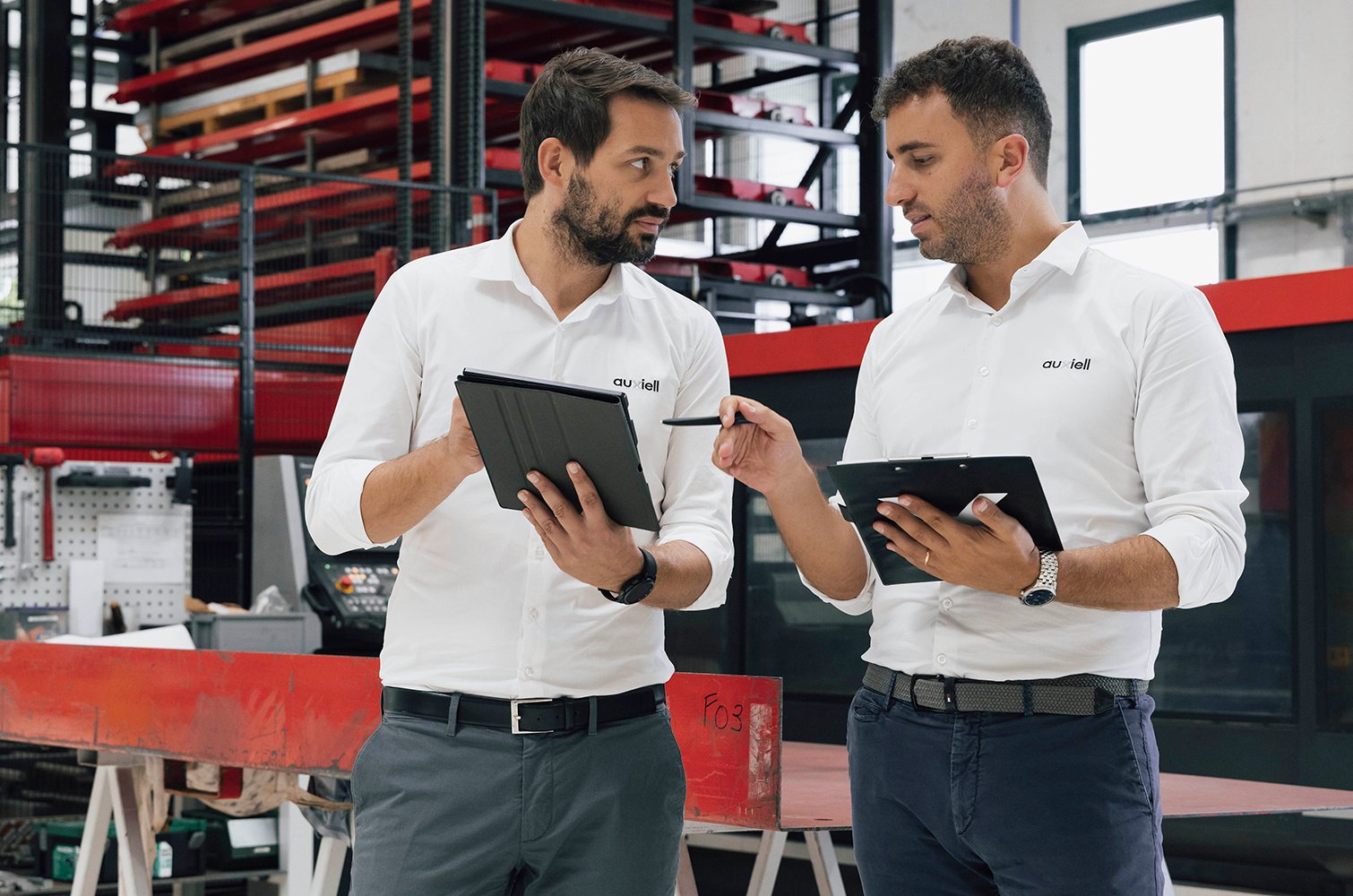
I nostri esperti a disposizione per guidare la tua azienda alla trasformazione
Iscriviti alla nostra newsletter e ricevi contenuti esclusivi, consigli pratici e novità direttamente nella tua inbox!