Portfolio
Effeuno
Intro
Come l'introduzione dell'approccio lean in un'azienda di piccole dimensioni ha permesso di acquisire il controllo dei processi duplicando la capacità produttiva e il fatturato
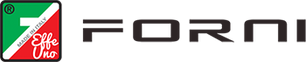
Settore
Sede
Con Effeuno abbiamo lavorato per efficientare i processi produttivi al fine di aumentare la capacità produttiva e raddoppiare il fatturato in due anni.
Il progetto che abbiamo intrapreso ha interessato il macro-processo di Delivery che comprende produzione, supply chain e gestione degli ordini: l’ambito che avrebbe portato maggiori benefici nel breve periodo in termini di capacità produttiva.
Grazie all’inserimento di Heijunka e Andon Board è migliorata la risposta al cliente finale ed è aumentata la consapevolezza del team di pianificazione in termini di capacità produttiva.
Applicando la tecnica di lean layout, inoltre, il team Effeuno ha potuto gestire in maniera consapevole il dimensionamento - in termini di persone e materiali - del plant produttivo, dei costi e dei tempi di implementazione delle linee stabilendo con anticipo gli obiettivi di efficientamento degli spazi, dei tempi e delle modalità di spedizione al cliente finale o al distributore.
Riprogettando il bilanciamento attraverso la tecnica VA/NVA e ottimizzando le logiche di pianificazione delle linee produttive la produttività è aumentata permettendo al team di eliminare le situazioni di sovraccarico e influenzando - di conseguenza l'efficienza produttiva.
Il lead time di consegna è diminuito del 78% allineandolo alle necessità del mercato. Grazie all'aumento dell'efficienza e della capacità produttiva, il fatturato in 4 anni è aumentato del + 286%, in linea con le aspettative del progetto.
Performance Raggiunte
efficienza
lead time
(dal momento dell'ordine alla spedizione)
fatturato in 4 anni
Vuoi migliorare le performance della tua azienda?
Storia
azienda
2007
Fondata nel 2007, Effeuno è un'azienda italiana che inizialmente si occupava esclusivamente della commercializzazione di forni professionali per la pizza.
Oggi
Negli anni Effeuno ha ampliato le sue attività includendo ora anche la produzione dei forni. La combinazione di tradizione e innovazione ha permesso all'azienda di crescere rapidamente e affermarsi nel mercato globale. Oggi l'azienda si distingue per la qualità dei suoi prodotti sia in Italia che a livello internazionale.
Dipendenti
0Fatturato (2023)
0EBITDA (2023)
0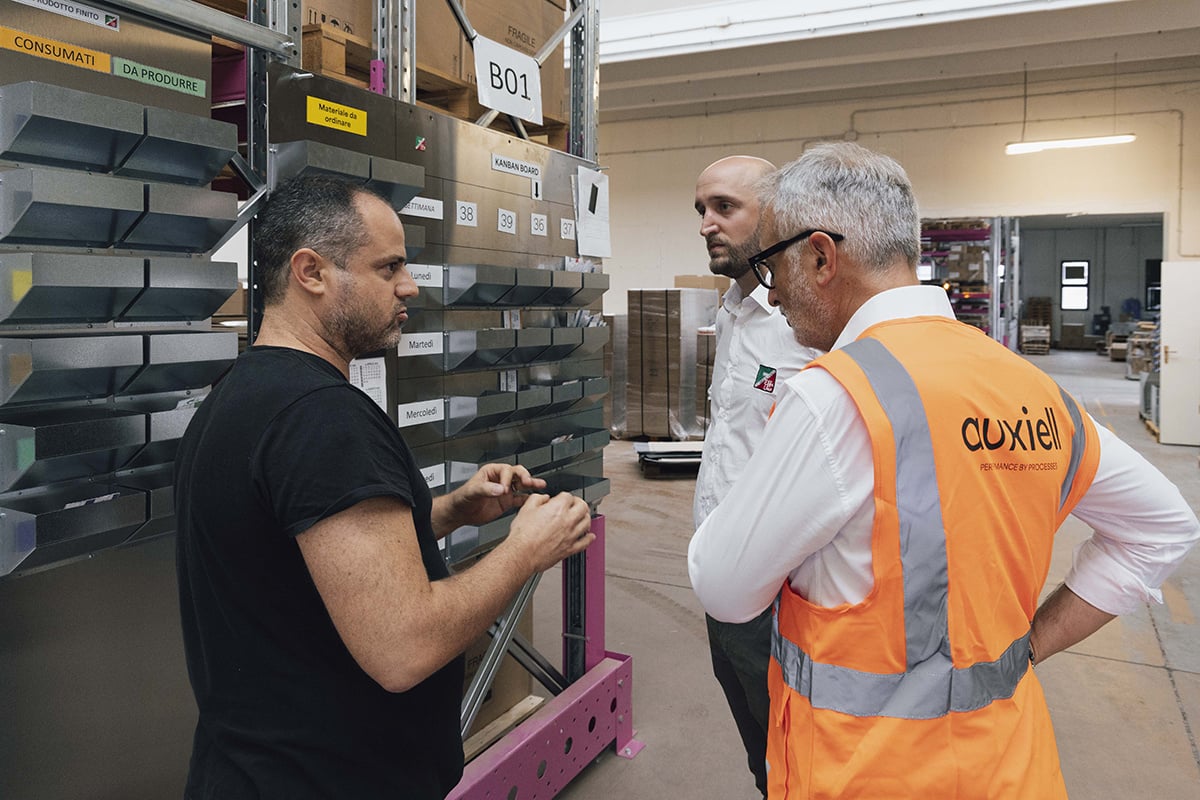
La sfida di Effeuno
Effeuno si è rivolta al nostro team per trovare un valido supporto nell’efficientamento dei processi al fine di aumentare la capacità produttiva e raddoppiare il fatturato in due anni.
Il punto di partenza
La trasformazione del primo macro-processo: Delivery
2020
Anno avvio collaborazione
con auxiell
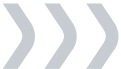
la collaborazione continua
Con Effeuno abbiamo intrapreso un progetto sul macro-processo di Delivery che comprende produzione, supply chain e gestione degli ordini: l’ambito che avrebbe portato maggiori benefici nel breve periodo in termini di capacità produttiva.
SCAN
Lean Gap Analysis® in Delivery
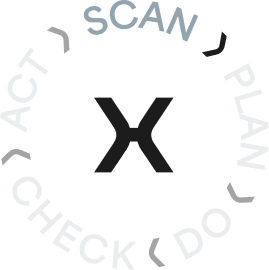
Per analizzare lo stato corrente dei processi il team auxiell-Effeuno si è impegnato nella Lean Gap Analysis®. In questa prima fase il team ha lavorato per “fotografare” lo stato corrente dell'intero processo produttivo dei forni "piccoli" - dal momento dell’arrivo dell’ordine fino alla spedizione del prodotto al cliente.
Lean Gap Analysis®
Fase indispensabile per misurare e analizzare i processi attuali e definire i gap tra lo stato attuale e quello desiderato. In questa prima fase si va a “fotografare” lo stato corrente dei processi in termini di quantificazione degli sprechi, individuazione di eventuali problematiche e opportunità di miglioramento, nonché di tempificazione di tutte le fasi. Avere una visione chiara delle performance del processo è necessario per individuare le più corrette contromisure volte a rimuovere la causa radice del problema e progettare, in ottica futura, le attività da fare – e su quali KPI misurarsi – per efficientarlo.
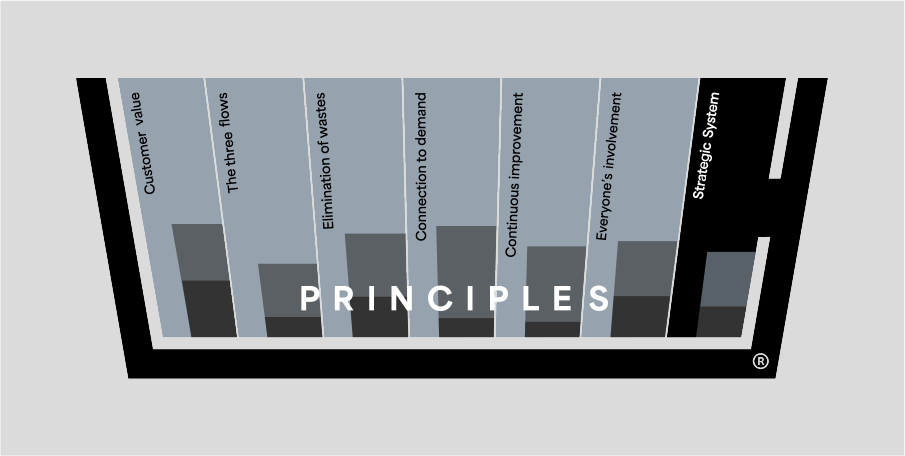
Processi con attività NVA (link alla wiki dove c'è attività NVA)
Le attività non a valore per il cliente – quali attese e movimentazioni di materiale non necessarie – presenti nella linea causavano uno sbilanciamento della linea di produzione.
Lunghi tempi di consegna al mercato
Molti clienti lamentavano la mancata ricezione di ordini nei tempi previsti.
Processi di miglioramento lenti
Le iniziative di miglioramento fino ad allora proposte ai fornitori non venivano ben accolte o avevano lunghi tempi di implementazione.
Lungo tempo impiegato nella gestione delle scorte
La pianificazione delle risorse e dei materiali per la produzione dei forni richiedeva tempi lunghi e la gestione di questa operazione interessava più risorse allungando i tempi.
PLAN
Lean RoadMap® in Delivery
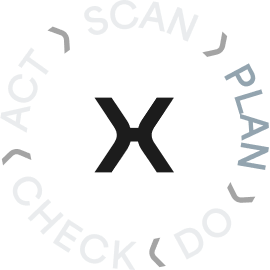
Una volta emersi i gap dalla Lean Gap Analysis® siamo passi alla fase successiva, ossia quella di PLAN. Attraverso la Lean RoadMap® abbiamo così definito la sequenza di implementazione delle più corrette tecniche lean che ci permettessero di raggiungere gli obiettivi concordati con il team Effeuno. La Lean RoadMap® identifica tecniche e metodi applicati nel corso del progetto.
Lean RoadMap®
Fase in cui si progetta lo stato futuro del processo analizzato in ottica multiscenario. Una volta scelto lo scenario più corretto dal punto di vista tecnico-economico si passa alla pianificazione del percorso da intraprendere per realizzarlo. Nella Lean RoadMap® emergono le attività su cui focalizzarci e le tempistiche con cui portarle a termine.
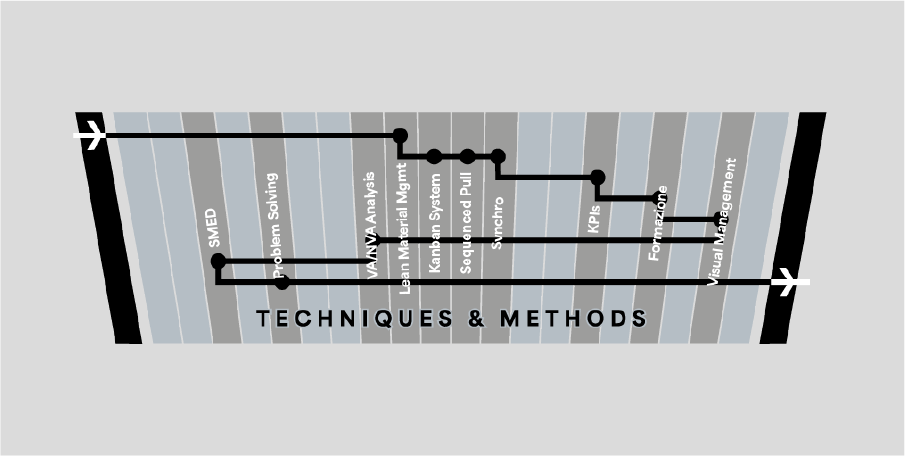
Valutazione make or buy
Attività implementata al fine di valutare se convenisse internalizzare o meno le varie fasi del processo di assemblaggio.Lean layout
Per progettare il layout - macro e micro - migliore possibile allineato alla crescita di fatturato prevista in modo tale da quantificare gli spazi necessari per materiali e prodotto finito.
Progettazione dei modelli di risposta al mercato per le differenti tipologie di clienti
Per progettare i processi produttivi in modo tale da quantificare gli spazi necessari per materiali e prodotto finito e poter quindi rispondere con modelli diversificati alle diverse tipologie di clienti (consumer per il mercato italia e dealer per il mercato estero) in termini di volumi e tempi di consegna.
Dimensionamento delle risorse e mappatura delle competenze necessarie per avviare il nuovo plant produttivo
Per definire il piano di assunzioni e gestire la formazione allineandola alle necessità del nuovo plant.
Creazione del piano di implementazione delle attività del nuovo processo produttivo
Per coordinare correttamente l'implementazione dei vari step produttivi senza ritardi o spreco di risorse.
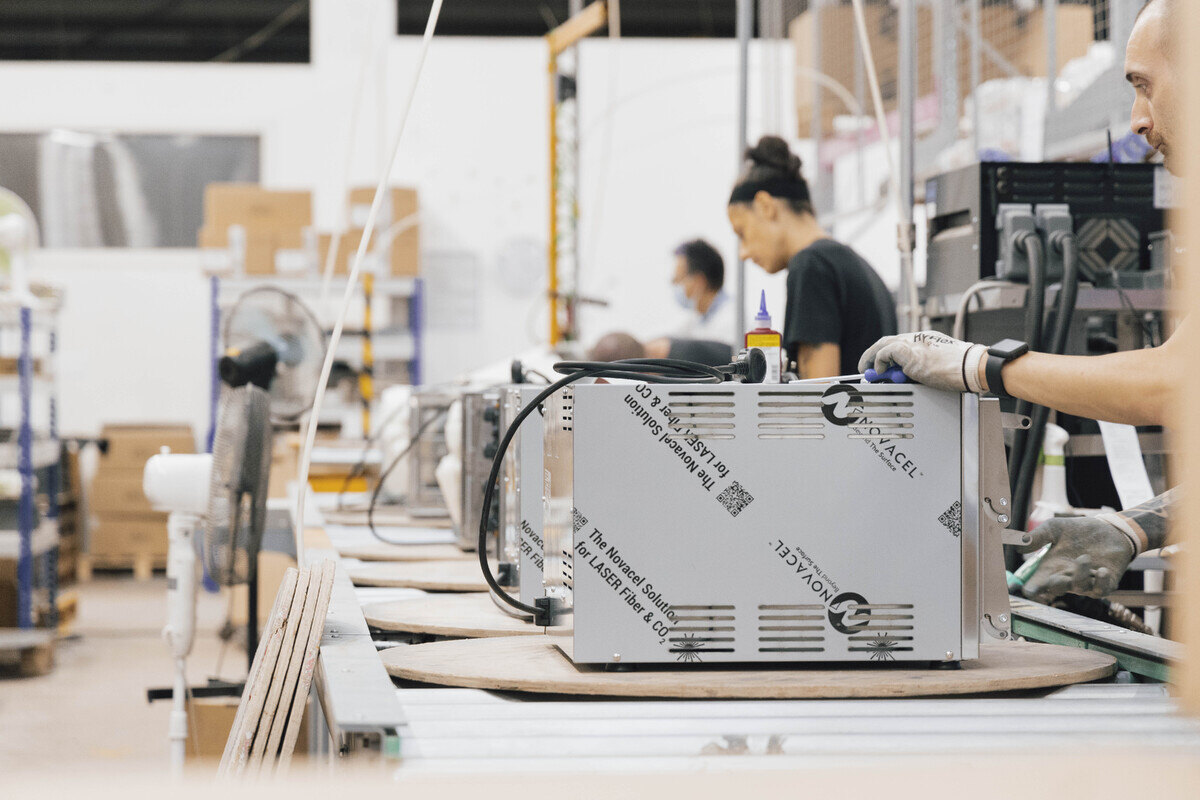
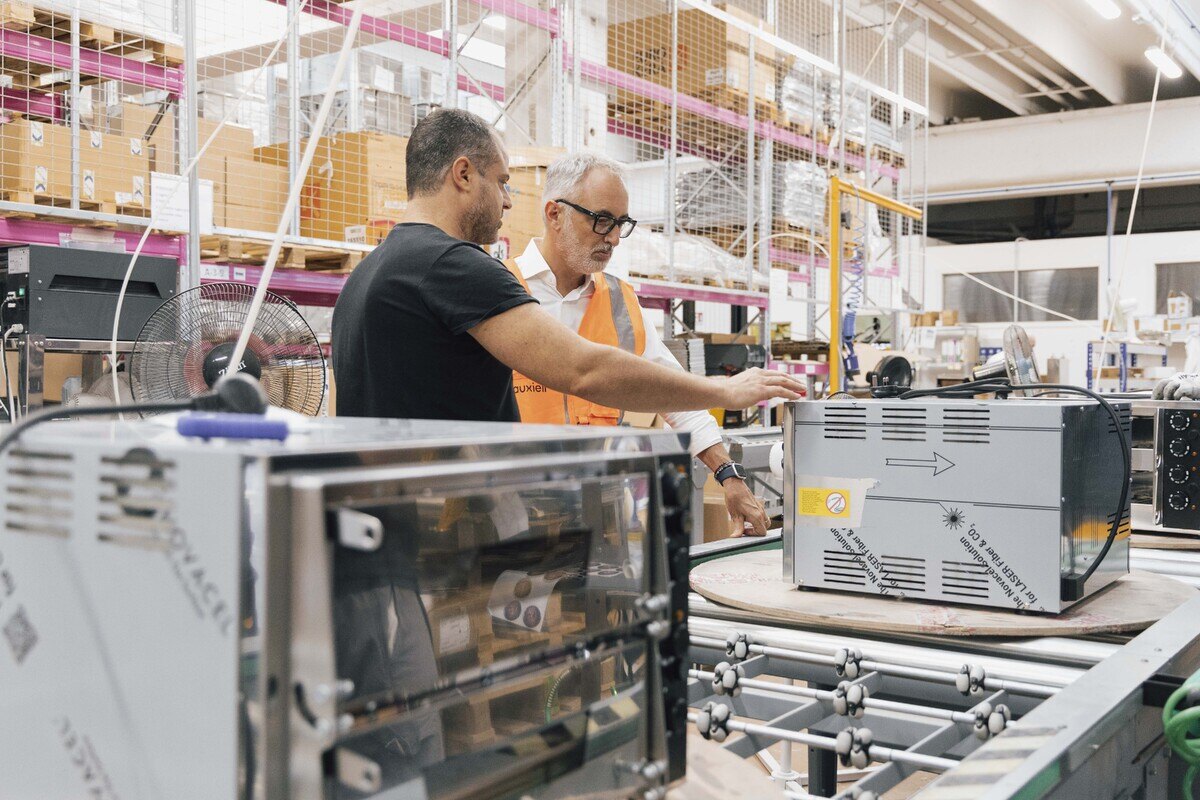

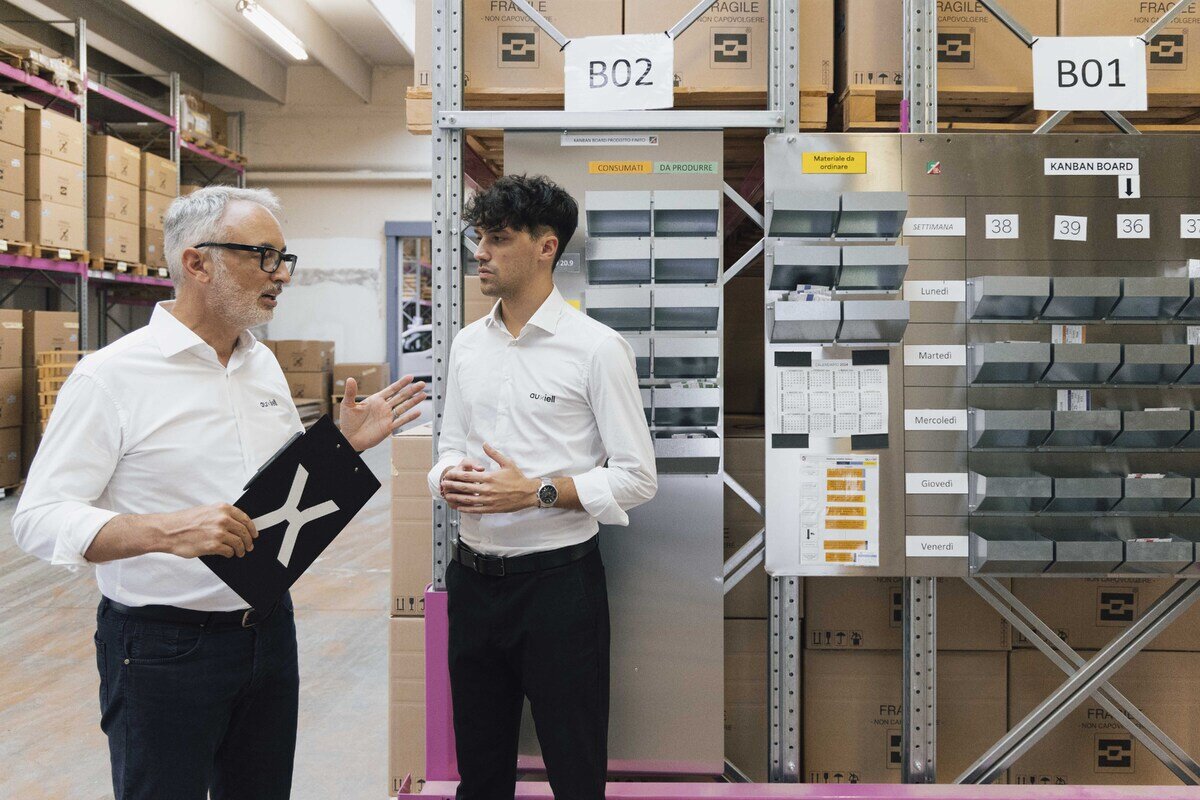
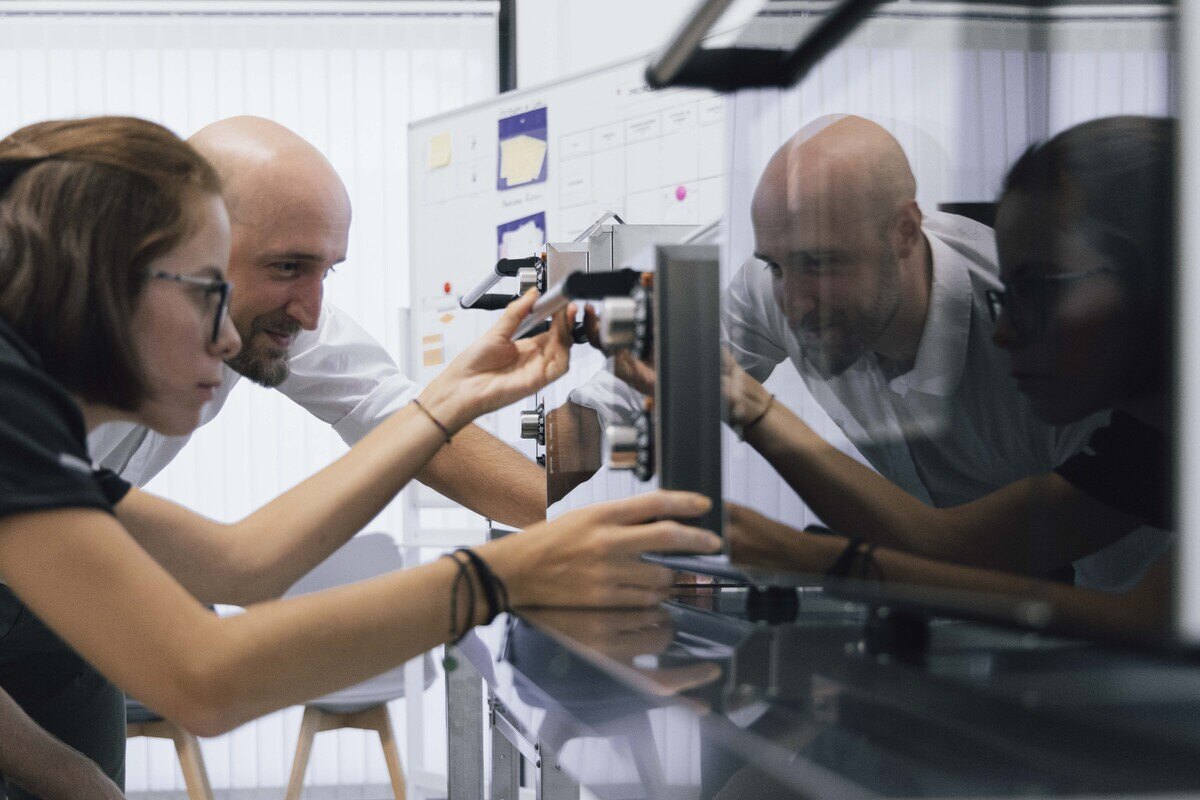
DO
Delivery Overall Transformation
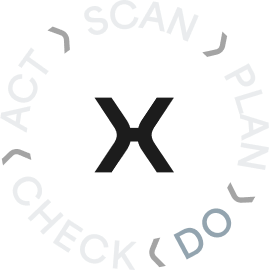
Quali attività e tecniche lean ci hanno permesso di raggiungere l’obiettivo stabilito?
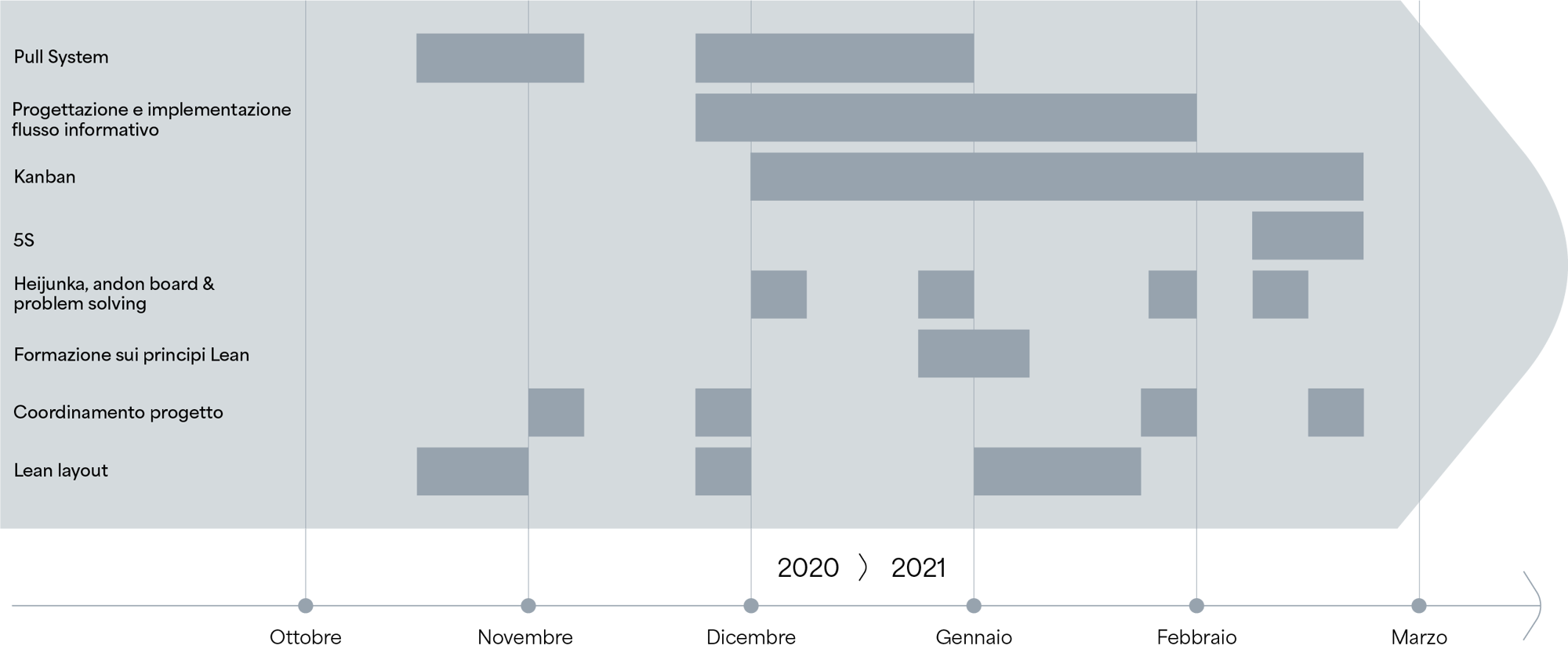
Heijunka e Andon Board
Il primo processo di schedulazione degli ordini di produzione è stato creato sulla base della capacità produttiva allocabile ed è stato inoltre introdotto un tabellone di monitoraggio della produzione giornaliera che segnala produttività e criticità emerse.
Lean layout
Il layout macro è stato progettato tenendo in considerazione vincoli architettonici e strutturali del nuovo plant. Il layout di dettaglio - delle singole postazioni - è stato progettato e realizzato tenendo in considerazione l'ergonomia e l'eliminazione delle attività non a valore individuate grazie all'implementazione della tecnica di analisi VA-NVA.
VA-NVA e Bilanciamento delle fasi
Le diverse fasi di lavorazione sono state analizzate e riprogettate equilibrando il carico di lavoro ed eliminando i tempi di attesa che generavano sprechi in termini di efficienza.
Kanban
Il problema dei materiali mancanti nel flusso produttivo è stato risolto creando delle regole di riapprovvigionamento automatiche che riducessero anche lo sforzo di pianificazione. Con il team Effeuno abbiamo inoltre lavorato anche sui fornitori critici per allineare e stabilizzare l'approvvigionamento dei materiali.
Problem solving
Tecnica applicata per analizzare la causa radice delle problematiche emerse nella quotidianità al fine di ridurre le soluzioni improvvisate e le interruzioni al processo produttivo.
5S
Tecnica applicata in tutta la produzione - sia a livello di singola postazione sia nelle aree di movimentazione - per garantire ordine e pulizia degli spazi di lavoro.
CHECK
Abbiamo raggiunto gli obiettivi stabiliti?
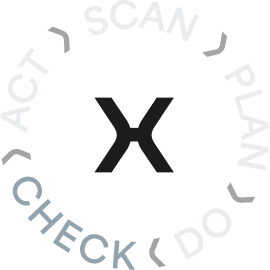
Applicando le tecniche di Heijunka e Andon Board è stato registrato un evidente miglioramento in termini di risposta alla domanda del cliente finale ed è aumentata inoltre la consapevolezza del team di pianificazione in termini di capacità produttiva.
Applicando la tecnica di lean layout il team Effeuno ha potuto gestire in maniera consapevole il dimensionamento - in termini di persone e materiali - del plant produttivo, dei costi e dei tempi di implementazione delle linee stabilendo con anticipo gli obiettivi di efficientamento degli spazi, dei tempi e delle modalità di spedizione al cliente finale o al distributore.
Riprogettando il bilanciamento attraverso la tecnica VA/NVA e ottimizzando le logiche di pianificazione delle linee produttive la produttività è aumentata del 141% permettendo al team di eliminare le situazioni di sovraccarico. L'efficienza produttiva ha così registrato un miglioramento del 14%.
Il lead time di consegna è diminuito del 78% rendendolo allineato alle necessità del mercato.
Attraverso la tecnica del problem solving (ricerca delle cause radice dei problemi) il team ha iniziato a sviluppare autonomamente il miglioramento degli standard di processo accelerandone quindi le attività.
La tecnica delle 5S applicata in tutta la produzione ha facilitato l'inserimento di nuove risorse con regole chiare e ha permesso di rendere il team più ingaggiato e coeso nella gestione degli spazi e attrezzature comuni.
Grazie all'aumento dell'efficienza e della capacità produttiva il fatturato in 4 anni è aumentato del + 286%.
I conflitti tra le funzioni commerciale, progettazione e produzione si sono ridotti.
Il progetto realizzato con il team Effeuno ha raggiunto risultati significativi e concreti. Grazie a un approccio mirato e collaborativo siamo riusciti a risolvere le sfide iniziali e a generare un impatto positivo e duraturo sul team. Il successo di questa prima collaborazione ha posto le basi per un rapporto di fiducia reciproca, che ci ha già permesso di esplorare nuove opportunità di crescita insieme.
Dal successo del primo progetto alle future possibilità di collaborazione
Oltre a concentrarsi sull'ottimizzazione dei processi è fondamentale lavorare sulle persone e con le persone. Favorire il coinvolgimento attivo del team, sviluppare le loro capacità e promuovere una cultura di collaborazione sono elementi chiave per garantire il successo di qualsiasi realtà. Solo creando un ambiente di lavoro positivo, in cui le persone si sentano valorizzate e parte integrante del processo, è possibile ottenere risultati duraturi e innovativi migliorando non solo l'efficienza operativa, ma anche il benessere organizzativo. Scopri come Effeuno ha lavorato con euxilia, realtà dell'auxiell group che opera facendo evolvere sistematicamente le persone e l'organizzazione per migliorare le competenze manageriali, comunicative e di allineamento strategico del team.
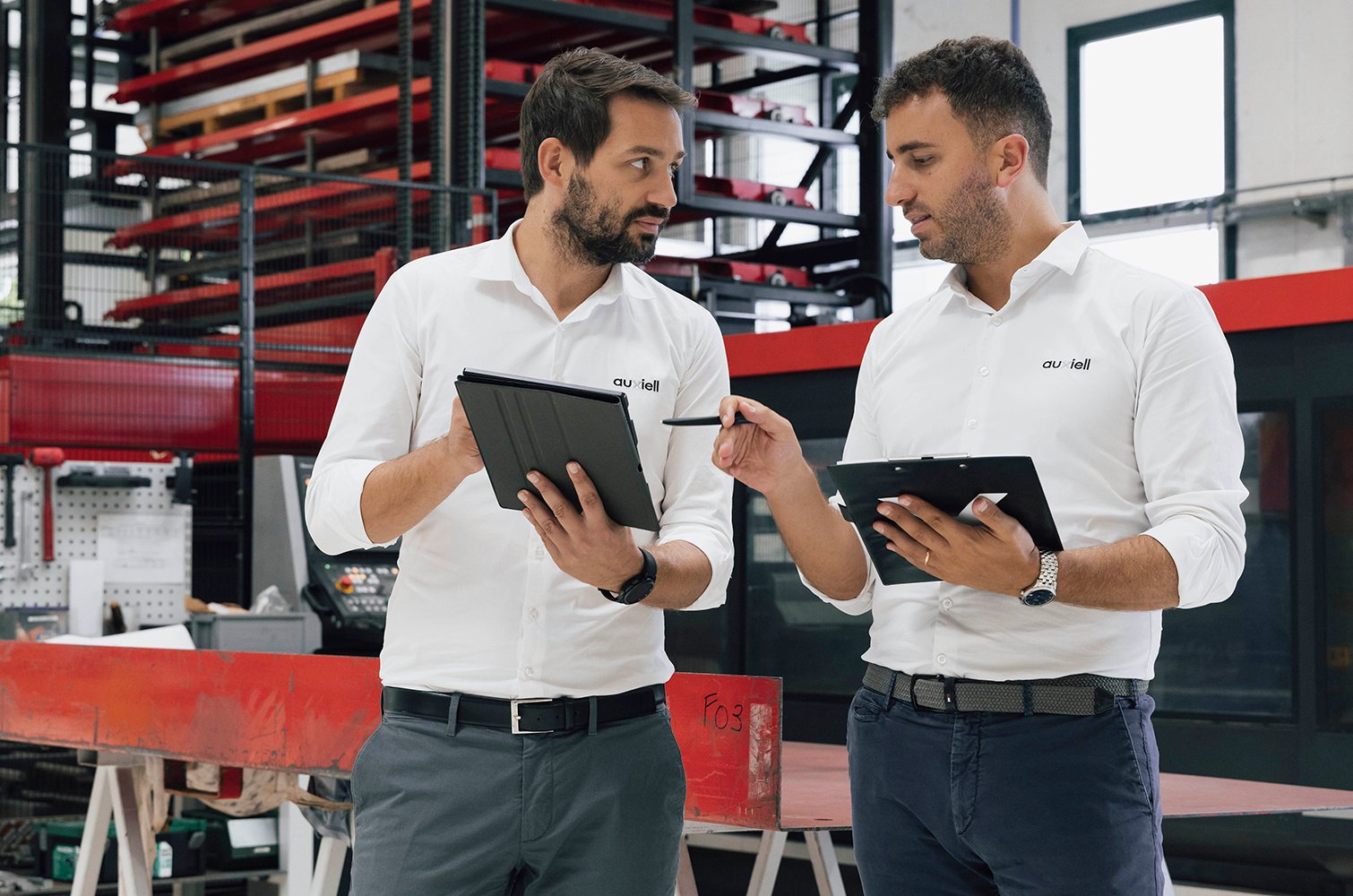
I nostri esperti a disposizione per guidare la tua azienda alla trasformazione
Iscriviti alla nostra newsletter e ricevi contenuti esclusivi, consigli pratici e novità direttamente nella tua inbox!