Portfolio
Energreen
Intro
Cómo Energreen consiguió hacer más eficientes los procesos aumentando la capacidad de producción en menos de un año
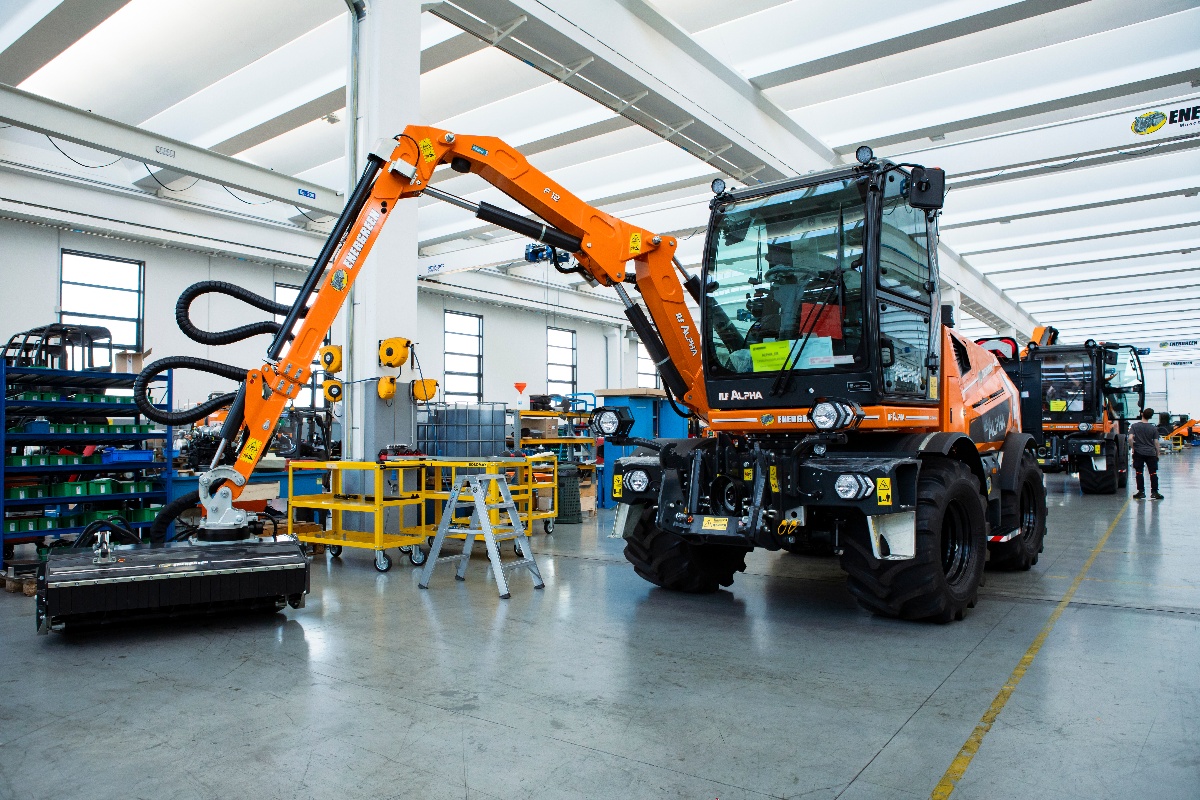
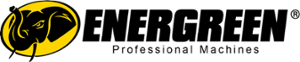
Industria
Oficina
Filiales
Energreen se dirigió a nuestro equipo para encontrar un valioso apoyo en la eficiencia de los procesos con el fin de sostener el crecimiento de la empresa, estimado en torno al 30% de facturación anual -una expectativa de crecimiento superada con creces teniendo en cuenta las cifras de 2023-, gran parte del cual derivaba de la producción de una familia de productos específica: las máquinas autopropulsadas ILF.
Por ello, emprendimos con Energreen un proyecto sobre el macroproceso de entrega que comprende la producción, la cadena de suministro y la gestión de pedidos: el área que más beneficios aportaría a corto plazo.
En cuanto a las actividades implementadas, la definición de los modelos de respuesta al mercado, el rediseño del flujo logístico-productivo, así como el del almacén y el servicio, permitieron, gracias también al diseño de una nueva disposición de las líneas y a la aplicación de la técnica de las 5S para la reorganización del espacio, reducir el plazo de entrega y el tiempo medio de producción, pero sobre todo aumentar la productividad media diaria.
Resultados obtenidos
Productividad media
diaria
ratio almacén/volumen de negocio
(con un objetivo inicial del 24,1%)
Tiempo medio de travesía
Tiempo ajustado
Historia
empresa
1999
Tras veinte años de experiencia en subcontratación para otras empresas, los hermanos Ivo y Lino Fraron, empresarios de Vicenza, fundaron Energreen, introduciendo una nueva rama de la empresa dedicada a la producción de máquinas para el mantenimiento ecológico.
Hoy
Energreen está en constante evolución y con los años se ha convertido en un actor importante en el sector público y privado de la maquinaria de mantenimiento verde. Sus innovadoras máquinas destacan por sus prestaciones, innovaciones tecnológicas, versatilidadyseguridad. La gama de máquinas autopropulsadas, en particular, se ha desarrollado con gran esmero para satisfacer las necesidades operativas directas de los usuarios finales, lo que ha dado lugar al registro de numerosas patentes a escala internacional.
Empleados
0Facturación (2023)
0EBITDA (2023)
0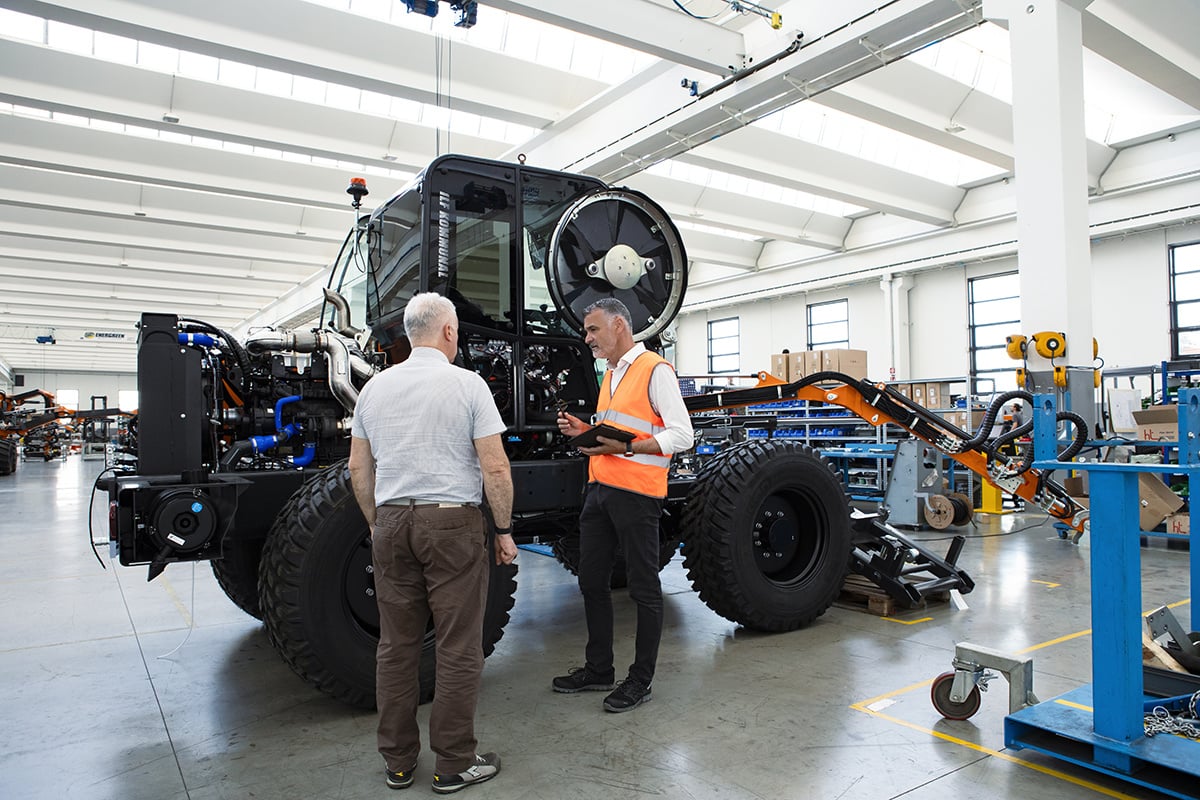
El reto de Energreen
Energreen recurrió a nuestro equipo para encontrar un valioso apoyo en la eficiencia de los procesos con el fin de mantener el crecimiento estimado de la empresa de alrededor del 30% en su facturación anual -una expectativa de crecimiento superada con creces teniendo en cuenta las cifras de 2023-, gran parte del cual se derivaba de la producción de una familia de productos específica: las máquinas autopropulsadas ILF.
El punto de partida
La transformación del primer macroproceso: la entrega
2023
Año de inicio de la colaboración
con auxiell
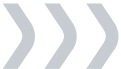
la colaboración continúa
Con Energreen emprendimos un proyecto sobre el macroproceso de entrega que comprende la producción, la cadena de suministro y la gestión de pedidos: el área que aportaría más beneficios a corto plazo. La elección recayó en la familia de productos de maquinaria autopropulsada ILF, que por sí sola representa entre el 45% y el 50% de la facturación y es también el producto con el proceso de producción más importante.
ESCÁNER
Lean Gap Analysis® en la entrega
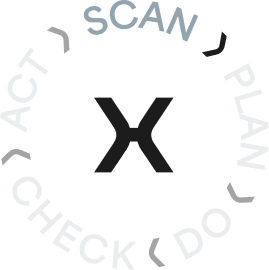
Para analizar el estado actual de los procesos, el equipo de Auxiell-Energreen realizó un Lean Gap Analysis® del proceso de producción, desde que llega el pedido hasta que se envía el producto al cliente. ¿Cuáles eran las actividades de valor y las que no lo eran? El resultado fue un análisis exhaustivo del estado actual del equilibrio de la línea y de los despilfarros existentes.
Lean Gap Analysis
Fase indispensable para medir y analizar los procesos actuales y definir las diferencias entre el estado actual y el deseado. En esta primera fase se toma una "instantánea" del estado actual de los procesos en términos de cuantificación de residuos, identificación de posibles problemas y oportunidades de mejora, y cronometraje de todas las etapas. Tener una visión clara del rendimiento del proceso es necesario para identificar las contramedidas más correctas para eliminar la raíz del problema y planificar, de cara al futuro, las actividades que hay que hacer -y sobre qué KPI medir- para hacerlo más eficiente.
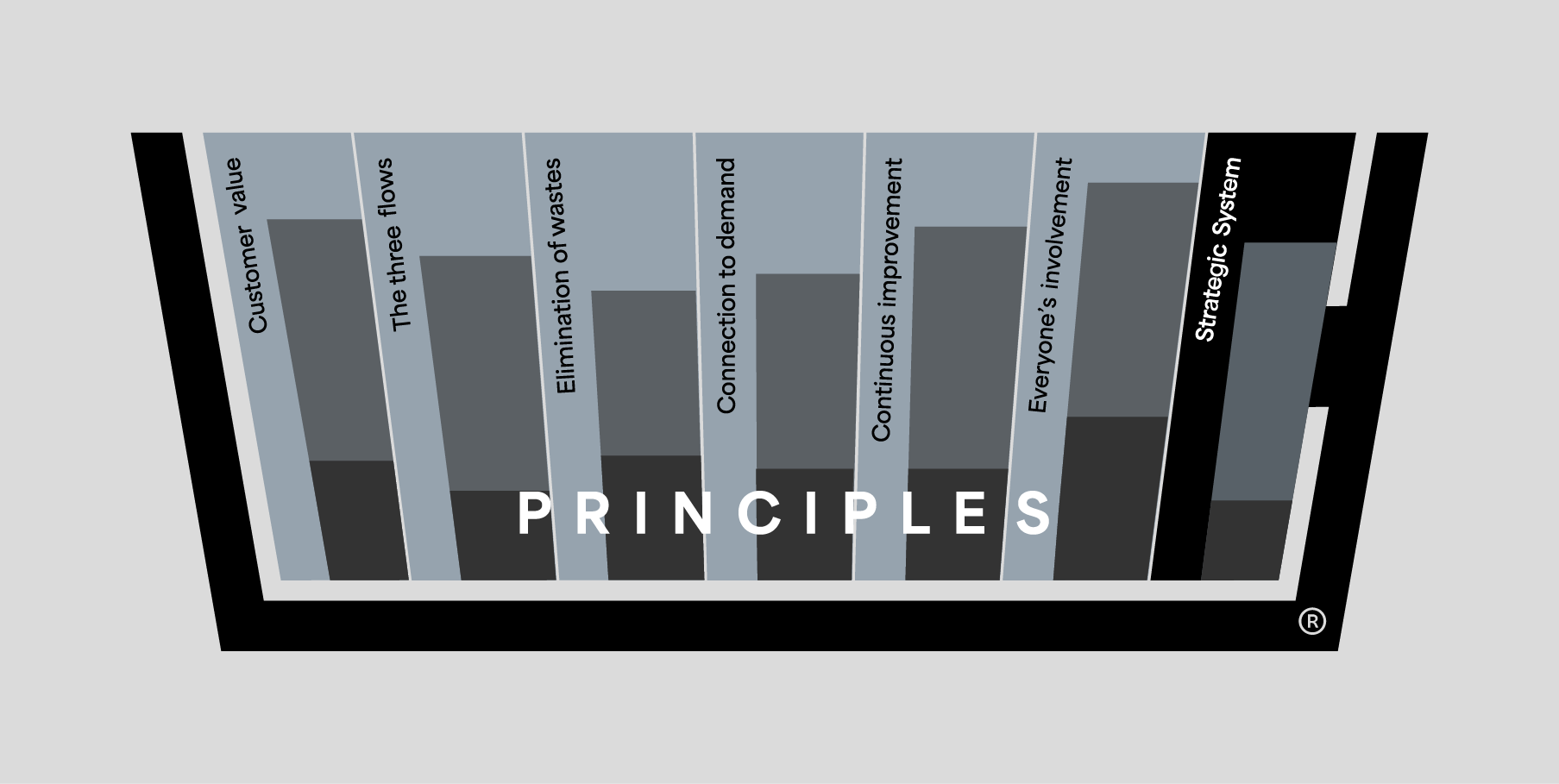
Procesos complejos con un elevado número de actividades NVA
Las actividades sin valor para el cliente -como las esperas innecesarias y la manipulación de materiales- en la línea provocaban un desequilibrio en la cadena de producción.
Disposición no lineal de la línea de producción
La disposición no lineal de la línea generaba ineficiencias en la producción.
Material en la zona de trabajo
La presencia excesiva de material innecesario generaba ineficiencias debido a los largos tiempos de búsqueda del mismo.
Centrarse en la eficiencia
Al principio, la atención se centró en la eficiencia de cada operación, pero no en todo el flujo de valor.
Procedimiento de producción uniforme para distintos productos
Las máquinas "estándar" y "a medida" seguían el mismo procedimiento de producción con tiempos de producción indefinidos y prolongados.
Processi complessi con un alto numero di attività NVA
Le attività non a valore per il cliente – quali attese e movimentazioni di materiale non necessarie – presenti nella linea causavano uno sbilanciamento della linea di produzione.
Layout della linea di produzione non lineare
La non linearità del layout della linea generava inefficienze nella produzione.
Materiale nell'area di lavoro
La presenza eccssiva di materiale non necessario generava inefficienze dovute ai tempi dilatati di ricerca dello stesso.
Visione puntuale dell'efficientamento
Il focus era inizialmente sull’efficientamento della singola operazione ma non sull’intero flusso del valore.
Iter produttivo omogeneo per prodotti differenti
Macchinari “standard” e “custom” seguivano lo stesso iter produttivo con tempi di produzione non definiti e lunghi.
PLAN
Lean RoadMap® en la entrega
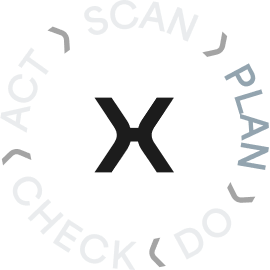
Estos fueron los puntos de partida para la siguiente fase del proyecto, la fase PLAN. A través del Lean RoadMap® definimos la secuencia de implantación de las técnicas lean más correctas que nos permitirían alcanzar los objetivos acordados con el equipo de Energreen.
Hoja de ruta Lean
Fase en la que se planifica el estado futuro del proceso analizado desde una perspectiva multiescenario. Una vez elegido el escenario más correcto desde el punto de vista técnico y económico, se pasa a la planificación del camino a seguir para realizarlo. En el Lean RoadMap® surgen las actividades en las que hay que centrarse y el plazo en el que hay que completarlas.
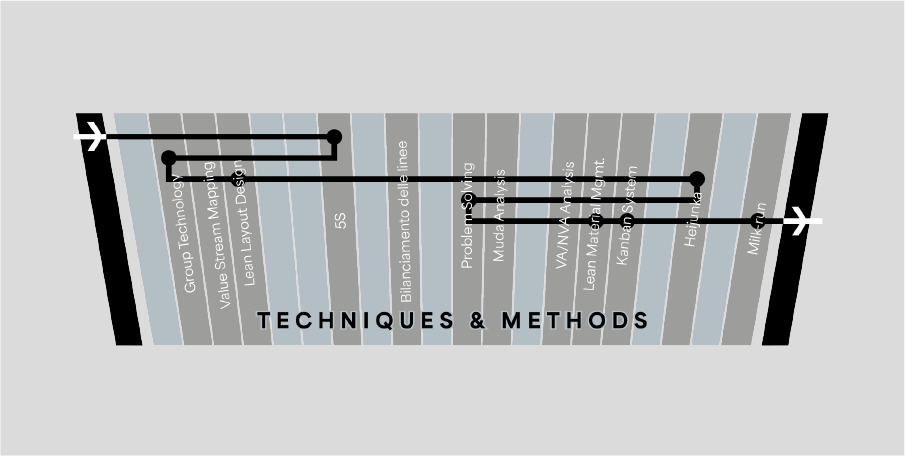
La dirección a seguir
Con el objetivo de reorganizar los distintos modelos organizativos para planificar mejor el proceso de producción, hemos reorganizado los productos de la siguiente manera:
-
Make to Stock - máquinas ya listas cuando llega el pedido.
-
Make to Order - material en stock ya disponible para poner el pedido en producción.
-
Purchase to Order - hay que comprar material para fabricar la máquina.
-
Engineer to Order - cuando llega el pedido hay que diseñar la máquina antes de iniciar la producción.
Rediseño del flujo logístico-productivo
En función de la reducción de las actividades del NVA.
Nuevo diseño de la distribución
Rediseño del flujo principal de la línea con tapones de producción adjuntos para cabinas, brazos y motores.
Aplicación de la técnica de las 5S
Técnica de reorganización del espacio para eliminar las actividades NVA.
Rediseñar el almacén y el servicio
Introducción del uso de un ordeñador con una cadencia fija.
La direzione da percorrere
Con l’obiettivo di riorganizzare i diversi modelli organizzativi per pianificare al meglio il processo produttivo, abbiamo riorganizzato i prodotti nel seguente modo:
-
Make to Stock - macchine già pronte al momento di arrivo dell’ordine.
-
Make to Order - materiale a magazzino già disponibile per mettere in produzione l’ordine.
-
Purchase to Order - è necessario acquistare il materiale per poter produrre la macchina.
-
Engineer to Order - quando arriva l’ordine la macchina va progettata prima di cominciare a produrla.
Riprogettazione del flusso logistico-produttivo
In funzione della riduzione delle attività NVA.
Progettazione di un nuovo layout
Riprogettazione del flusso principale della linea con annesse spine di produzione di cabine, bracci e motori.
Applicazione della tecnica 5S
Tecnica di riorganizzazione dello spazio per eliminare le attività NVA.
Riprogettazione del magazzino e dell’asservimento
Introducendo l'utilizzo di un milkrun con cadenza fissa.
DO
Entrega Transformación global
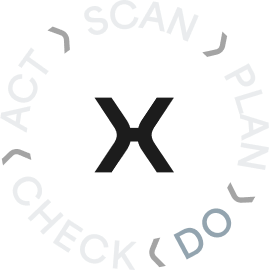
¿Qué actividades y técnicas lean nos han permitido alcanzar el objetivo fijado?
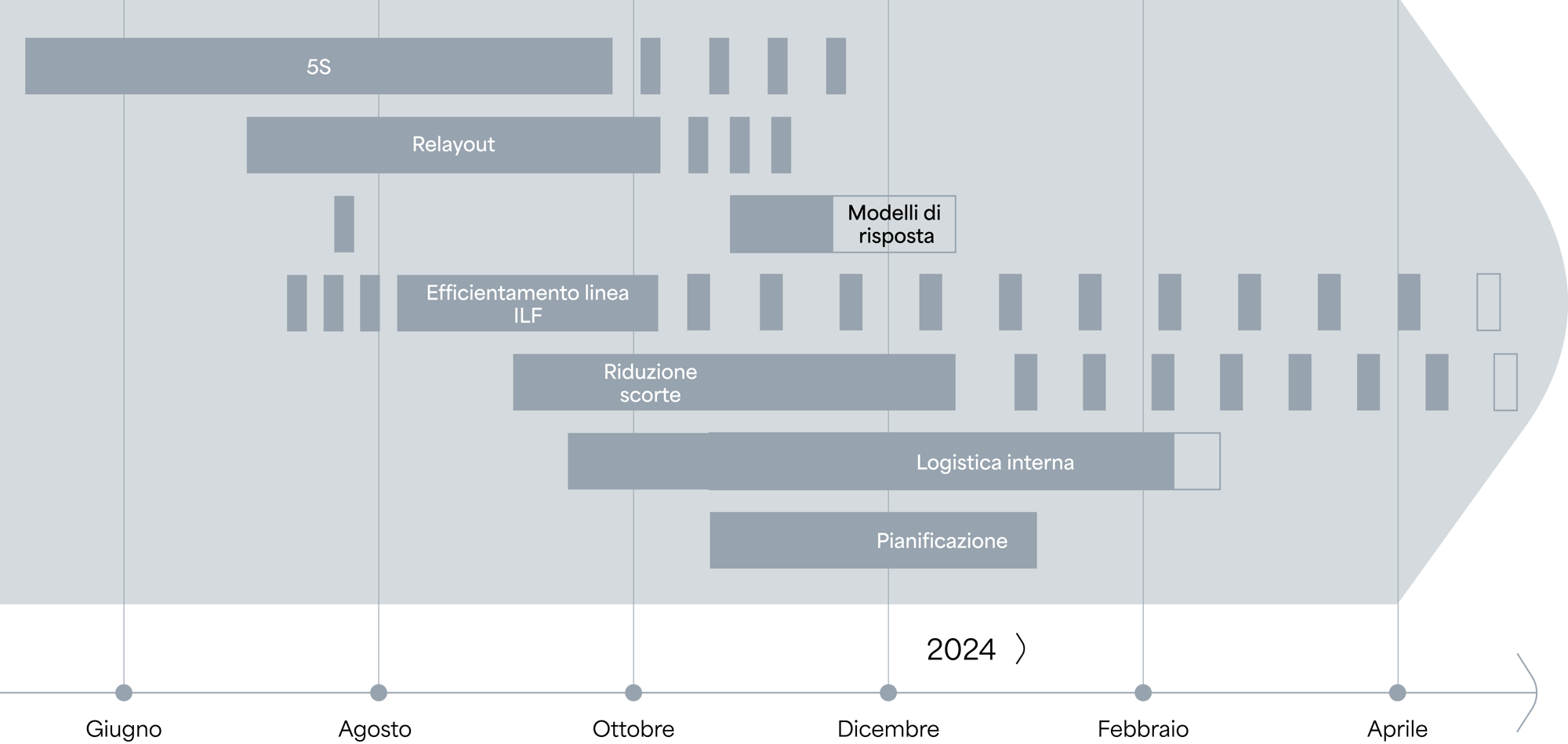
Distribución ajustada de la producción y el almacén
Las estaciones de línea se revisaron para realizar la disposición diseñada en la fase de planificación mediante la aplicación de la técnica del diagrama de espaguetis.
5S
Reorganizar y limpiar el espacio de trabajo en todas las estaciones de trabajo de la línea de producción, tapones adjuntos, con el objetivo de reducir algunos de los NVA de tipo 2 que podrían eliminarse a corto plazo. En concreto, nos centramos en los que implicaban movimientos innecesarios del operario y tiempos prolongados de búsqueda de material. Se formó a unas 40 personas durante un total de unas diez horas y se abrieron cinco centros piloto.
Pull Servo
El proceso de producción se ha transformado empezando por la forma en que se atiende a la línea: se ha pasado de la producción "por lotes" al "flujo de una pieza" vinculando el consumo real de la línea a la recogida de material. Inicialmente, la preparación de material implicaba preparar varias máquinas a la vez, mientras que hoy en día se hace de una en una.
Mediante la implantación del milkrun (cada cuatro horas), la línea dispone ahora sólo de lo necesario para las máquinas que se están procesando realmente en ese momento. El sistema implantado suministra material de alta rotación, bajo valor y bajo volumen. Además, para equilibrar la línea de producción, se redefinieron las fases de procesamiento con el fin de distribuir las actividades de forma que las distintas máquinas se equilibraran entre sí.
Implantación de la Heijunka
Herramienta utilizada para planificar la línea en modo de modelo mixto, lo que permite trabajar en diferentes máquinas de forma secuencial y ya no en grupos de familias de productos.
Aplicación de la resolución de problemas a la eficiencia del proceso
Técnica aplicada durante el relanzamiento y el equilibrado de líneas para investigar la causa raíz de los obstáculos surgidos durante el rediseño del proceso y eliminarlos eficazmente.
Lean layout della produzione e del magazzino
Le postazioni della linea sono state riviste per realizzare il layout progettato nella fase di Plan attraverso l’applicazione della tecnica Spaghetti Chart.
5S
Per riordinare e pulire lo spazio di lavoro su tutte le postazioni della linea di produzione, spine annesse, con l’obiettivo di ridurre parte delle NVA di tipo 2, eliminabili nel breve periodo. Nello specifico ci siamo concentrati su quelle che comportavano movimenti non necessari degli operatori e tempi prolungati di ricerca del materiale. Sono state formate circa 40 persone per un totale di una decina di ore di formazione e 5 cantieri pilota aperti.
Asservimento pull
Il processo produttivo è stato trasformato partendo dalla modalità di asservimento della linea: si è passati da una produzione “lotto” al “one-piece-flow” collegando l’effettivo consumo della linea al prelievo dei materiali. Inizialmente il picking del materiale implicava il prelievo di più macchine assieme mentre oggi avviene con il prelievo di una macchina alla volta.
Attraverso l’implementazione del milkrun (ogni quattro ore) in linea ora è presente sempre e solo ciò che è necessario per le macchine effettivamente in lavorazione in quel momento. Il sistema implementato rifornisce il materiale alto-rotante, a basso valore e poco ingombrante. Inoltre, per bilanciare la linea di produzione sono state ridefinite le fasi di lavorazione allo scopo di distribuire le attività affinché macchine diverse di bilanciassero tra loro.
Implementazione dell'Heijunka
Strumento utilizzato per pianificare la linea in modalità “mixed-model” permettendo di lavorare macchine diverse in sequenza e non più a gruppi di famiglia prodotto.
Applicazione del Problem Solving per l'efficientamento del processo
Tecnica apllicata in fase di relayout e bilanciamento della linea per indagare la causa radice degli ostacoli emersi in fase di riprogettazione del processo e poterli rimuovere efficacemente.
COMPROBAR
¿Hemos alcanzado nuestros objetivos?
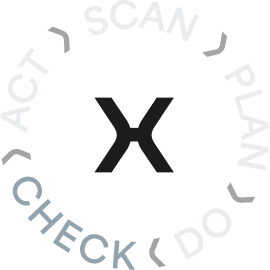
La aplicación de la técnica de las 5S -en todas las estaciones de la línea, enchufes incluidos- permitió reorganizar por completo la zona, que ahora parece mucho más ordenada, limpia y funcional.
La línea de producción se ha rediseñado por completo con vistas a un servicio y una planificación de flujo único en comparación con el anterior funcionamiento por lotes semanales.
La disposición revisada ha mejorado -además del trabajo diario del equipo- todo el equilibrio de la línea al hacer más eficiente la producción.
La línea se estabilizó alineando las compras con el consumo.
La eficiencia de la productividad aumentó un 18%, calculada como producción diaria por persona, un objetivo alcanzado antes del final del proyecto.
El ratio existencias/volumen de negocio alcanzó el 21,9%, frente al objetivo fijado al inicio del proyecto del 24,1%.
El tiempo medio de travesía disminuyó un 20%.
El tiempo de respuesta del mercado -el transcurrido entre la realización del pedido y la fecha de expedición- disminuyó un 40%.
L'applicazione della tecnica 5S – su tutte le postazioni della linea, spine annesse – ha permesso di riorganizzare completamente l’area che oggi appare molto più ordinata, pulita e funzionale.
La linea produttiva è stata completamente riprogettata in ottica di asservimento e pianificazione one-piece-flow rispetto alla precedente gestione a lotto settimanale.
Il layout rivisto ha migliorato – oltre che il lavoro quotidiano del team – l'intero bilanciamento della linea efficientando la produzione.
La linea è stata stabilizzata allineando gli acquisti ai consumi.
L'efficienza produttività è aumentata del 18%, calcolata come produzione giornaliera a persona – obiettivo raggiunto in anticipo rispetto alla fine del progetto.
Il rapporto magazzino/fatturato ha raggiunto quota 21,9% – su un target stabilito a inizio progetto di 24,1%.
Il tempo di attraversamento medio ha registrato una riduzione del 20%.
Tempo di risposta al mercato – trascorso tra la data di inserimento dell’ordine e quella di spedizione – è diminuito del 40%.
Los beneficios obtenidos influyeron positivamente en el equipo. Las personas, que se pusieron a disposición desde el principio y mostraron una notable disposición al cambio, abrazaron el proyecto con entusiasmo. Son las personas las que aportan los resultados y solo cambiando su comportamiento es posible tener éxito en la transformación: esta es la verdadera diferencia entre ser lean y hacer lean.
Del macroproceso de entrega al de desarrollo
El mercado en el que opera Energreen evoluciona constantemente tanto en amplitud como en profundidad de su gama de productos. Esto tiene numerosas repercusiones en el proceso de producción que a menudo no se tienen en cuenta durante el proceso de diseño.La innovación de los productos es, por tanto, un aspecto fundamental de esta realidad. En consecuencia, poder racionalizar los procesos de desarrollo en términos de tiempo y recursos invertidos es una necesidad primordial.
Leer también
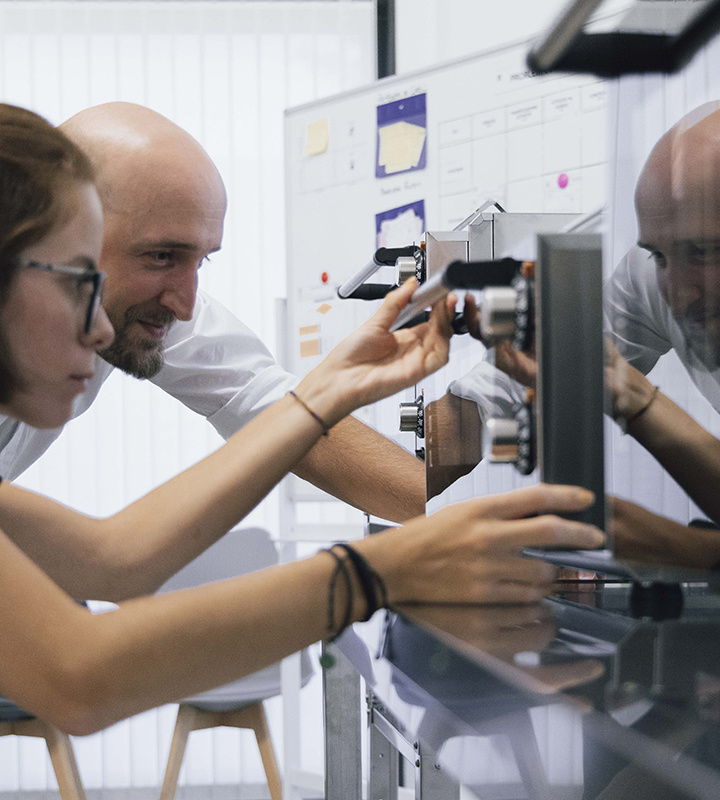
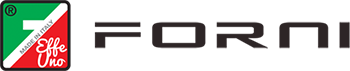
03
Effeuno
A lo largo de los años, Effeuno ha ampliado sus actividades para incluir ahora la producción de hornos. La combinación de tradición e innovación ha permitido a la empresa crecer rápidamente y establecerse en el mercado mundial. En la actualidad, la empresa destaca por la calidad de sus productos tanto en Italia como a escala internacional.
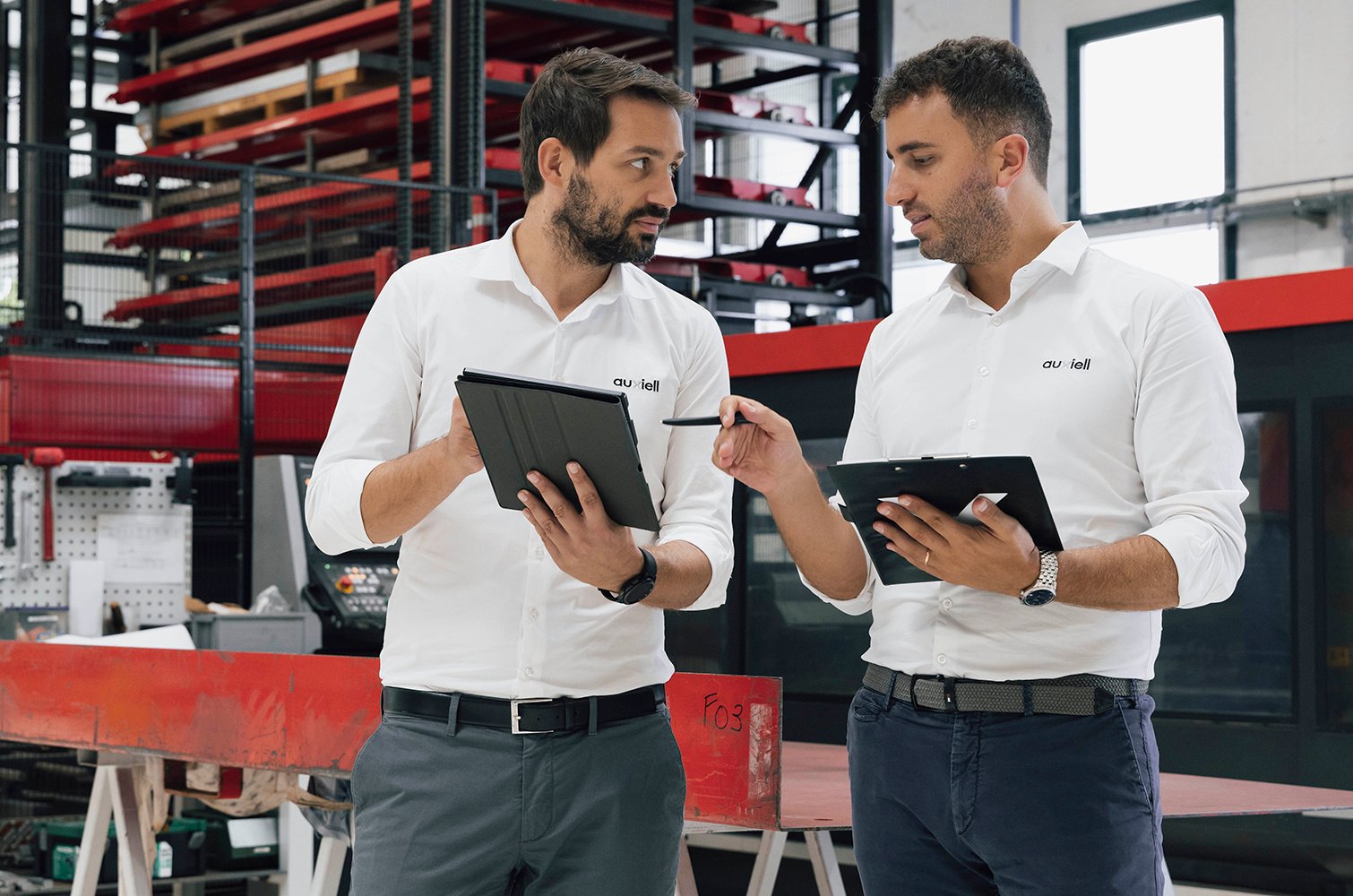
Nuestros expertos a su disposición para guiar a su empresa hacia la transformación
Suscríbase a nuestro boletín y reciba contenidos exclusivos, consejos prácticos y noticias directamente en su bandeja de entrada.