Portfolio
Energreen
Intro
Come Energreen è riuscita a efficientare i processi aumentando la capacità produttiva in meno di un anno
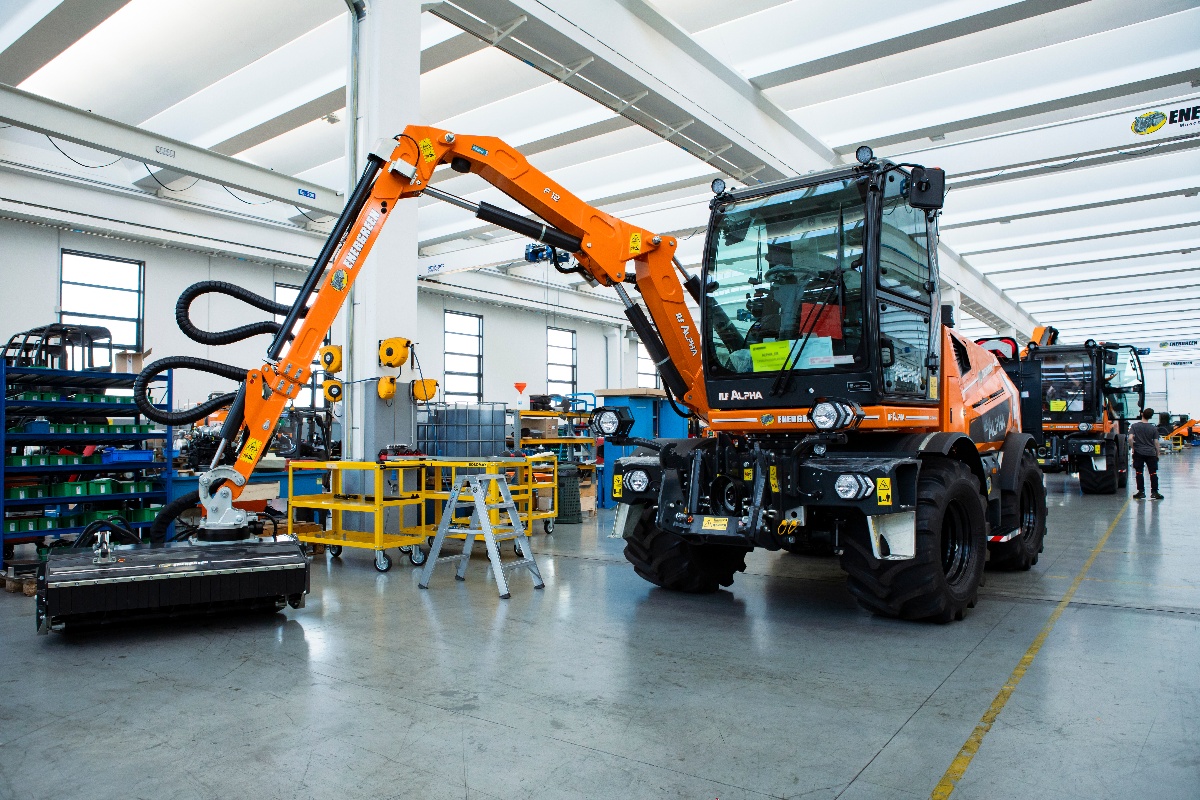
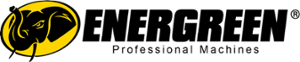
Settore
Sede
Filiali
Energreen si è rivolta al nostro team per trovare un valido supporto nell’efficientamento dei processi al fine di sostenere la crescita aziendale stimata intorno al 30% di fatturato annuo – aspettativa di crescita di gran lunga superata considerando i dati 2023 –, gran parte del quale derivante dalla produzione di una specifica famiglia di prodotto: le macchine semoventi ILF.
Con Energreen abbiamo quindi intrapreso un progetto sul macro-processo di Delivery che comprende produzione, supply chain e gestione degli ordini: l’ambito che avrebbe portato maggiori benefici nel breve termine.
In riferimento alle attività implementate, la definizione dei modelli di risposta al mercato, la riprogettazione del flusso logistico-produttivo così come quella del magazzino e dell’asservimento hanno permesso, anche grazie alla progettazione di un nuovo layout della linea e all’applicazione della tecnica delle 5S per la riorganizzazione dello spazio, di ridurre il lead time e il tempo di attraversamento medio ma soprattutto di aumentare la produttività media giornaliera.
Performance Raggiunte
Produttività media
giornaliera
rapporto magazzino/fatturato
(con obiettivo di partenza 24,1%)
Tempo di attraversamento medio
Lean time
Vuoi migliorare le performance della tua azienda?
Storia
azienda
1999
Dopo vent'anni di esperienza nell'outsourcing per altre aziende, i fratelli Ivo e Lino Fraron, imprenditori vicentini, fondano Energreen introducendo un nuovo ramo d'azienda dedicato alla produzione di macchine destinate alla manutenzione del verde.
Oggi
Energreen è in costante evoluzione e nel corso degli anni è diventata un attore principale nel settore delle macchine per il mantenimento del verde pubblico e privato. Le sue macchine innovative si distinguono per prestazioni, innovazioni tecnologiche, versatilità e sicurezza. La gamma di macchine semoventi, in particolare, è stata sviluppata con grande cura per soddisfare le esigenze operative dirette degli utilizzatori finali, il che ha portato alla registrazione di numerosi brevetti a livello internazionale.
Dipendenti
0Fatturato (2023)
0EBITDA (2023)
0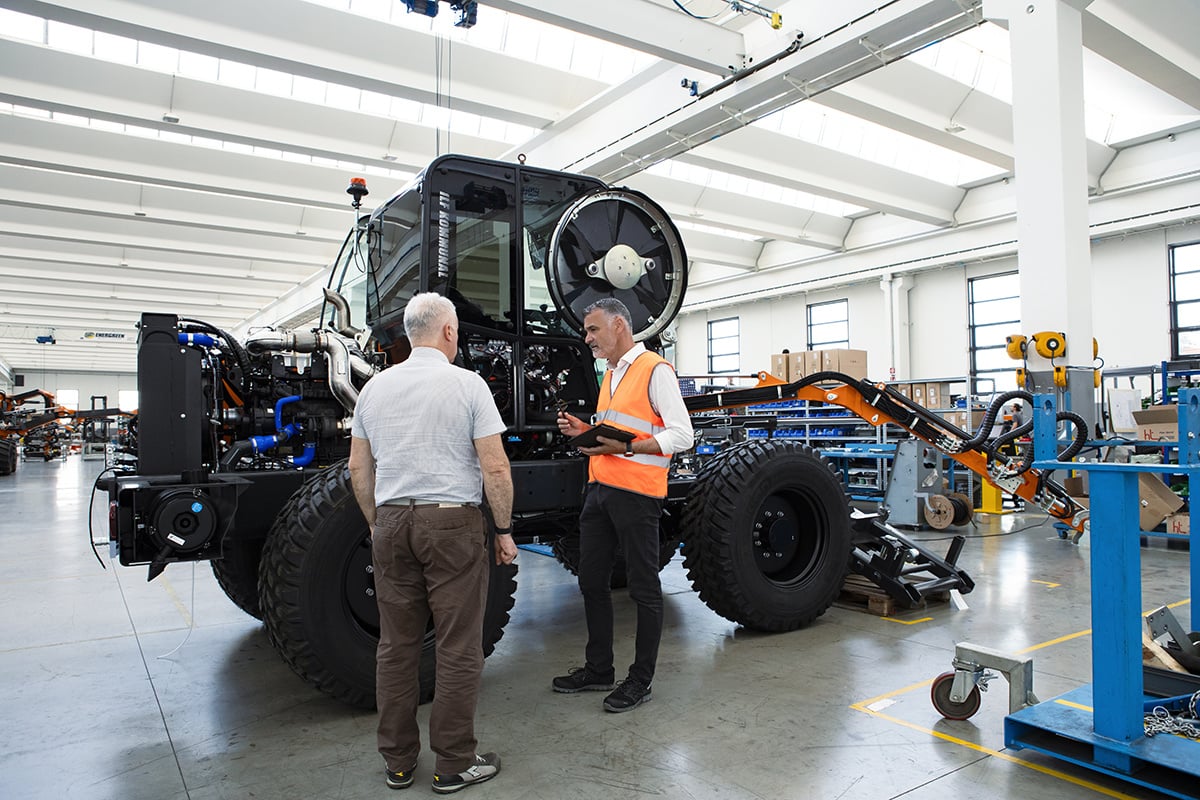
La sfida di Energreen
Energreen si è rivolta al nostro team per trovare un valido supporto nell’efficientamento dei processi al fine di sostenere la crescita aziendale stimata intorno al 30% di fatturato annuo – aspettativa di crescita di gran lunga superata considerando i dati 2023 –, gran parte del quale derivante dalla produzione di una specifica famiglia di prodotto: le macchine semoventi ILF.
Il punto di partenza
La trasformazione del primo macro-processo: Delivery
2023
Anno avvio collaborazione
con auxiell
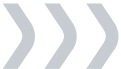
la collaborazione continua
Con Energreen abbiamo intrapreso un progetto sul macro-processo di Delivery che comprende produzione, supply chain e gestione degli ordini: l’ambito che avrebbe portato maggiori benefici nel breve termine. La scelta è ricaduta sulla famiglia di prodotti macchine semoventi ILF che da sola copre il 45-50% fatturato e rappresenta anche il prodotto con il processo produttivo più importante.
SCAN
Lean Gap Analysis® in Delivery
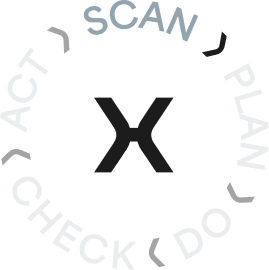
Per analizzare lo stato corrente dei processi il team auxiell-Energreen si è impegnato nella Lean Gap Analysis® del processo produttivo - dal momento dell’arrivo dell’ordine fino alla spedizione del prodotto al cliente. Quali erano le attività a valore e quelle non a valore? Ne è emersa un’analisi completa dello stato as is del bilanciamento della linea e degli sprechi a suo interno.
Lean Gap Analysis®
Fase indispensabile per misurare e analizzare i processi attuali e definire i gap tra lo stato attuale e quello desiderato. In questa prima fase si va a “fotografare” lo stato corrente dei processi in termini di quantificazione degli sprechi, individuazione di eventuali problematiche e opportunità di miglioramento, nonché di tempificazione di tutte le fasi. Avere una visione chiara delle performance del processo è necessario per individuare le più corrette contromisure volte a rimuovere la causa radice del problema e progettare, in ottica futura, le attività da fare – e su quali KPI misurarsi – per efficientarlo.
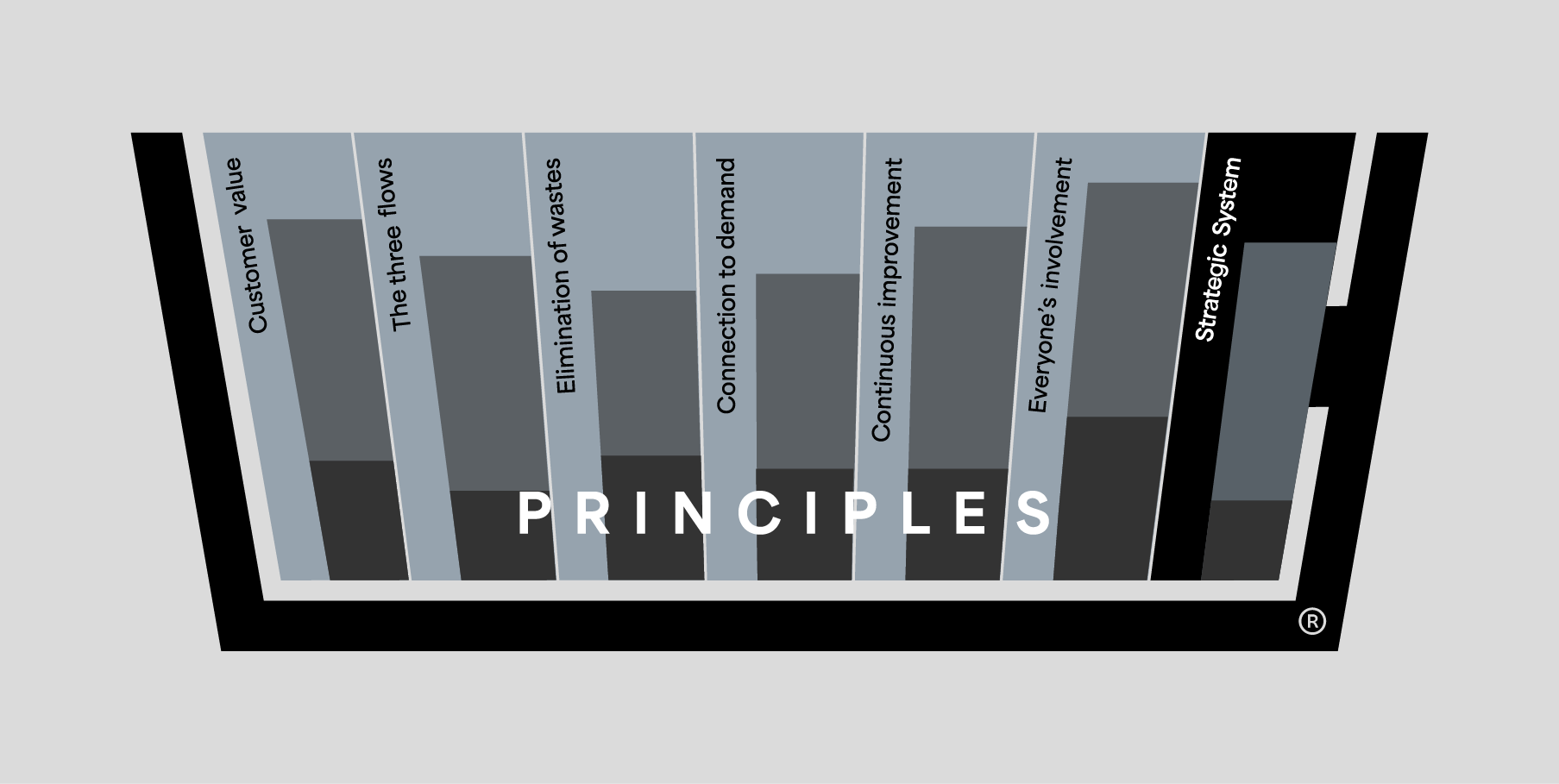
Processi complessi con un alto numero di attività NVA
Le attività non a valore per il cliente – quali attese e movimentazioni di materiale non necessarie – presenti nella linea causavano uno sbilanciamento della linea di produzione.
Layout della linea di produzione non lineare
La non linearità del layout della linea generava inefficienze nella produzione.
Materiale nell'area di lavoro
La presenza eccssiva di materiale non necessario generava inefficienze dovute ai tempi dilatati di ricerca dello stesso.
Visione puntuale dell'efficientamento
Il focus era inizialmente sull’efficientamento della singola operazione ma non sull’intero flusso del valore.
Iter produttivo omogeneo per prodotti differenti
Macchinari “standard” e “custom” seguivano lo stesso iter produttivo con tempi di produzione non definiti e lunghi.
PLAN
Lean RoadMap® in Delivery
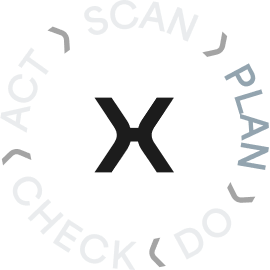
Questi i punti di partenza alla base della fase successiva del progetto, ossia quella di PLAN. Attraverso la Lean RoadMap® abbiamo definito la sequenza di implementazione delle più corrette tecniche lean che ci permettessero di raggiungere gli obiettivi concordati con il team Energreen.
Lean RoadMap®
Fase in cui si progetta lo stato futuro del processo analizzato in ottica multiscenario. Una volta scelto lo scenario più corretto dal punto di vista tecnico-economico si passa alla pianificazione del percorso da intraprendere per realizzarlo. Nella Lean RoadMap® emergono le attività su cui focalizzarci e le tempistiche con cui portarle a termine.
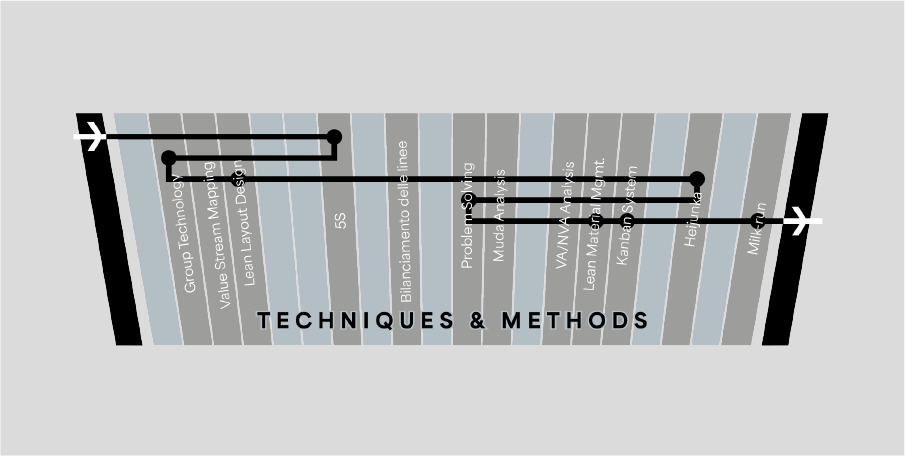
La direzione da percorrere
Con l’obiettivo di riorganizzare i diversi modelli organizzativi per pianificare al meglio il processo produttivo, abbiamo riorganizzato i prodotti nel seguente modo:
-
Make to Stock - macchine già pronte al momento di arrivo dell’ordine.
-
Make to Order - materiale a magazzino già disponibile per mettere in produzione l’ordine.
-
Purchase to Order - è necessario acquistare il materiale per poter produrre la macchina.
-
Engineer to Order - quando arriva l’ordine la macchina va progettata prima di cominciare a produrla.
Riprogettazione del flusso logistico-produttivo
In funzione della riduzione delle attività NVA.
Progettazione di un nuovo layout
Riprogettazione del flusso principale della linea con annesse spine di produzione di cabine, bracci e motori.
Applicazione della tecnica 5S
Tecnica di riorganizzazione dello spazio per eliminare le attività NVA.
Riprogettazione del magazzino e dell’asservimento
Introducendo l'utilizzo di un milkrun con cadenza fissa.
DO
Delivery Overall Transformation
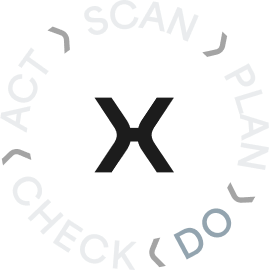
Quali attività e tecniche lean ci hanno permesso di raggiungere l’obiettivo stabilito?
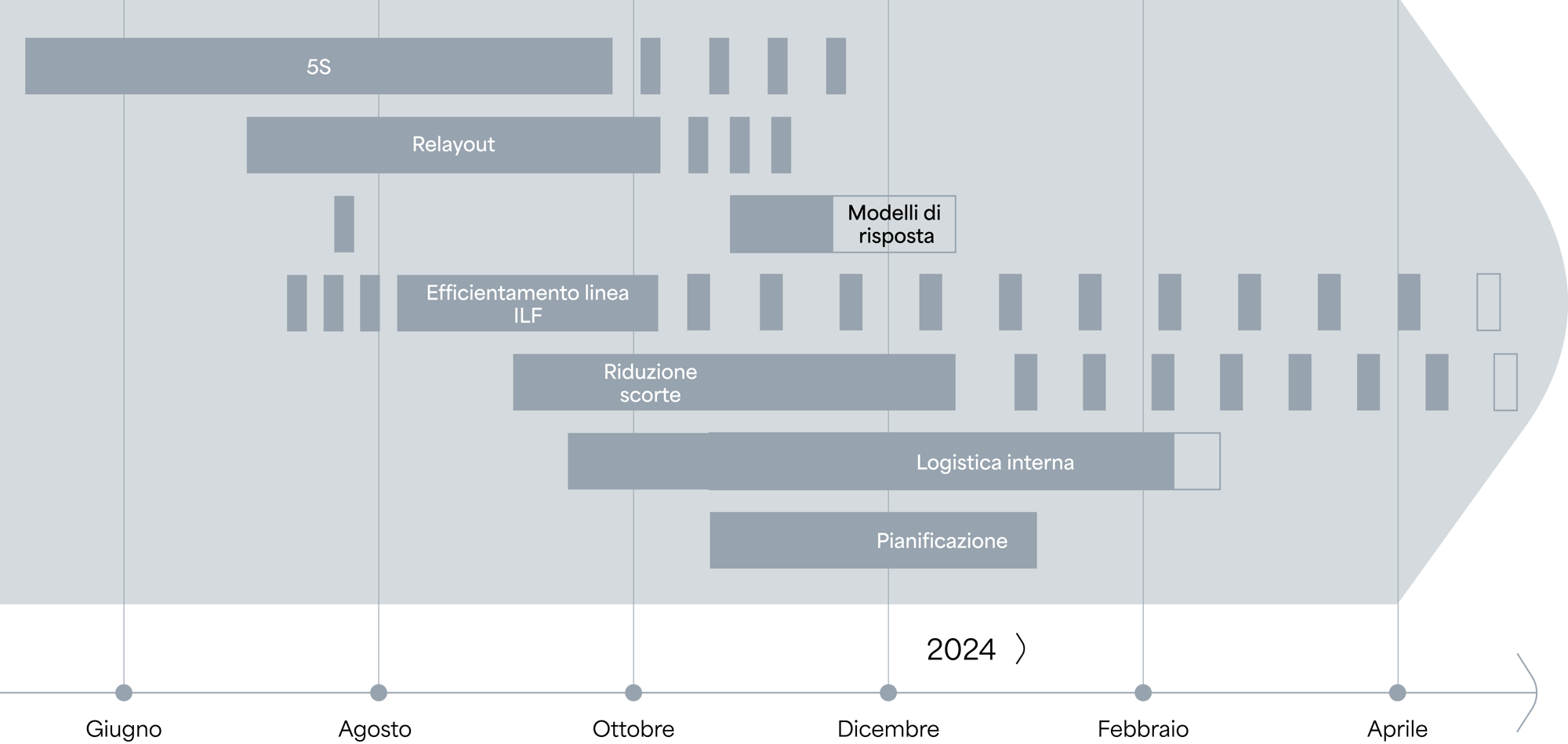
Lean layout della produzione e del magazzino
Le postazioni della linea sono state riviste per realizzare il layout progettato nella fase di Plan attraverso l’applicazione della tecnica Spaghetti Chart.
5S
Per riordinare e pulire lo spazio di lavoro su tutte le postazioni della linea di produzione, spine annesse, con l’obiettivo di ridurre parte delle NVA di tipo 2, eliminabili nel breve periodo. Nello specifico ci siamo concentrati su quelle che comportavano movimenti non necessari degli operatori e tempi prolungati di ricerca del materiale. Sono state formate circa 40 persone per un totale di una decina di ore di formazione e 5 cantieri pilota aperti.
Asservimento pull
Il processo produttivo è stato trasformato partendo dalla modalità di asservimento della linea: si è passati da una produzione “lotto” al “one-piece-flow” collegando l’effettivo consumo della linea al prelievo dei materiali. Inizialmente il picking del materiale implicava il prelievo di più macchine assieme mentre oggi avviene con il prelievo di una macchina alla volta.
Attraverso l’implementazione del milkrun (ogni quattro ore) in linea ora è presente sempre e solo ciò che è necessario per le macchine effettivamente in lavorazione in quel momento. Il sistema implementato rifornisce il materiale alto-rotante, a basso valore e poco ingombrante. Inoltre, per bilanciare la linea di produzione sono state ridefinite le fasi di lavorazione allo scopo di distribuire le attività affinché macchine diverse di bilanciassero tra loro.
Implementazione dell'Heijunka
Strumento utilizzato per pianificare la linea in modalità “mixed-model” permettendo di lavorare macchine diverse in sequenza e non più a gruppi di famiglia prodotto.
Applicazione del Problem Solving per l'efficientamento del processo
Tecnica apllicata in fase di relayout e bilanciamento della linea per indagare la causa radice degli ostacoli emersi in fase di riprogettazione del processo e poterli rimuovere efficacemente.
CHECK
Abbiamo raggiunto gli obiettivi stabiliti?
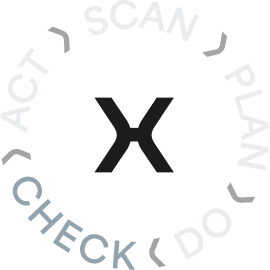
L'applicazione della tecnica 5S – su tutte le postazioni della linea, spine annesse – ha permesso di riorganizzare completamente l’area che oggi appare molto più ordinata, pulita e funzionale.
La linea produttiva è stata completamente riprogettata in ottica di asservimento e pianificazione one-piece-flow rispetto alla precedente gestione a lotto settimanale.
Il layout rivisto ha migliorato – oltre che il lavoro quotidiano del team – l'intero bilanciamento della linea efficientando la produzione.
La linea è stata stabilizzata allineando gli acquisti ai consumi.
L'efficienza produttività è aumentata del 18%, calcolata come produzione giornaliera a persona – obiettivo raggiunto in anticipo rispetto alla fine del progetto.
Il rapporto magazzino/fatturato ha raggiunto quota 21,9% – su un target stabilito a inizio progetto di 24,1%.
Il tempo di attraversamento medio ha registrato una riduzione del 20%.
Tempo di risposta al mercato – trascorso tra la data di inserimento dell’ordine e quella di spedizione – è diminuito del 40%.
I benefici raggiunti hanno influenzato positivamente il team. Le persone, che si sono rese da subito disponibili dimostrando una notevole propensione al cambiamento, hanno accolto il progetto con entusiasmo. Sono le persone a portare i risultati e solo cambiando il loro comportamento è possibile avere successo nella trasformazione: questa è la vera differenza tra essere lean e fare lean.
Dal macro-processo di Delivery a quello del Development
Il mercato in cui opera Energreen vive una continua evoluzione sia dal punto di vista dell’ampiezza che della profondità della gamma prodotto. Ciò comporta numerosi impatti sul processo produttivo spesso non considerati durante la progettazione. L’innovazione di prodotto è quindi un aspetto fondamentale per questa realtà. Di conseguenza riuscire a efficientare i processi di sviluppo in termini di tempo e risorse investite si va a delineare come un bisogno primario.
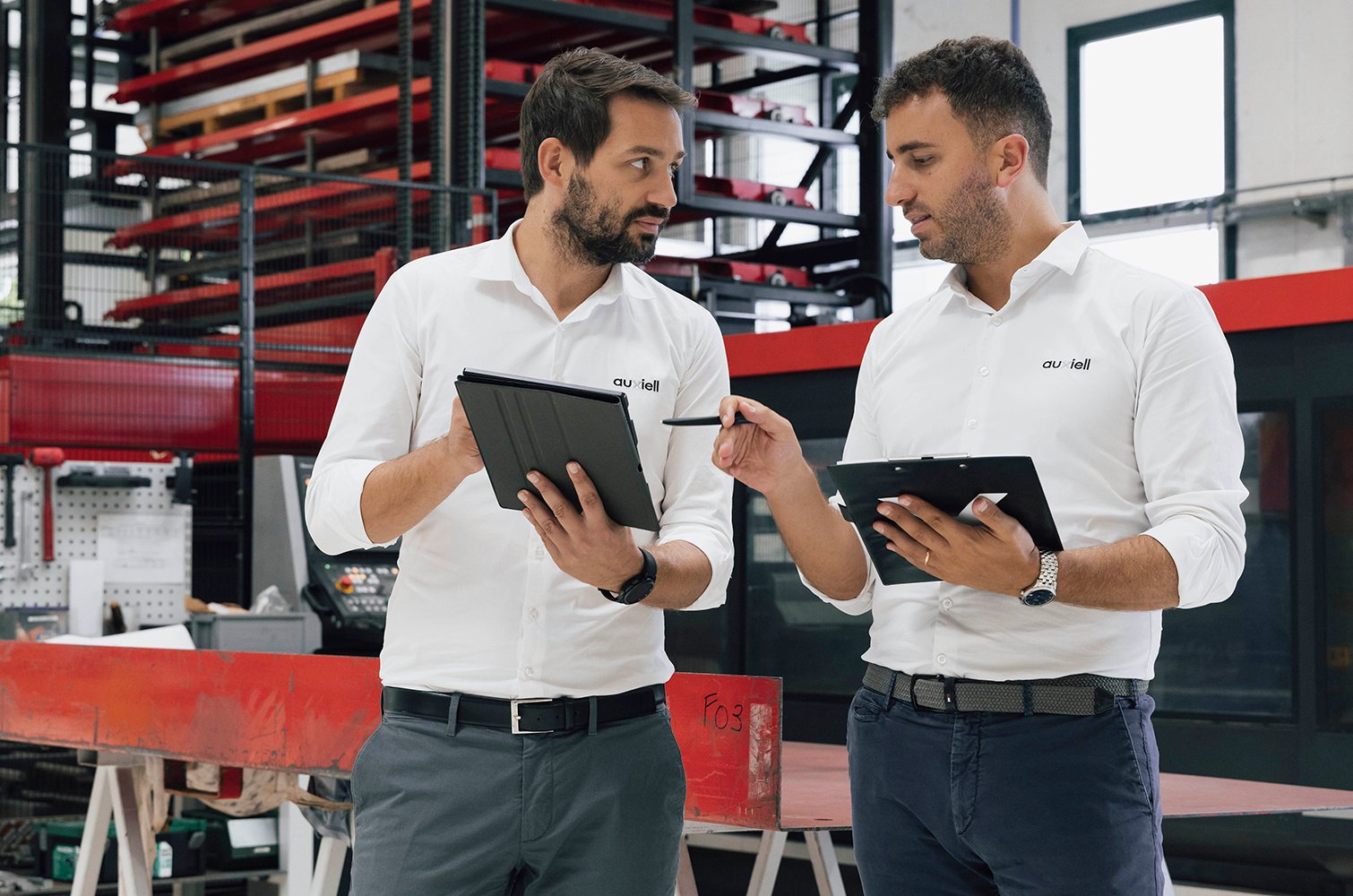
I nostri esperti a disposizione per guidare la tua azienda alla trasformazione
Iscriviti alla nostra newsletter e ricevi contenuti esclusivi, consigli pratici e novità direttamente nella tua inbox!