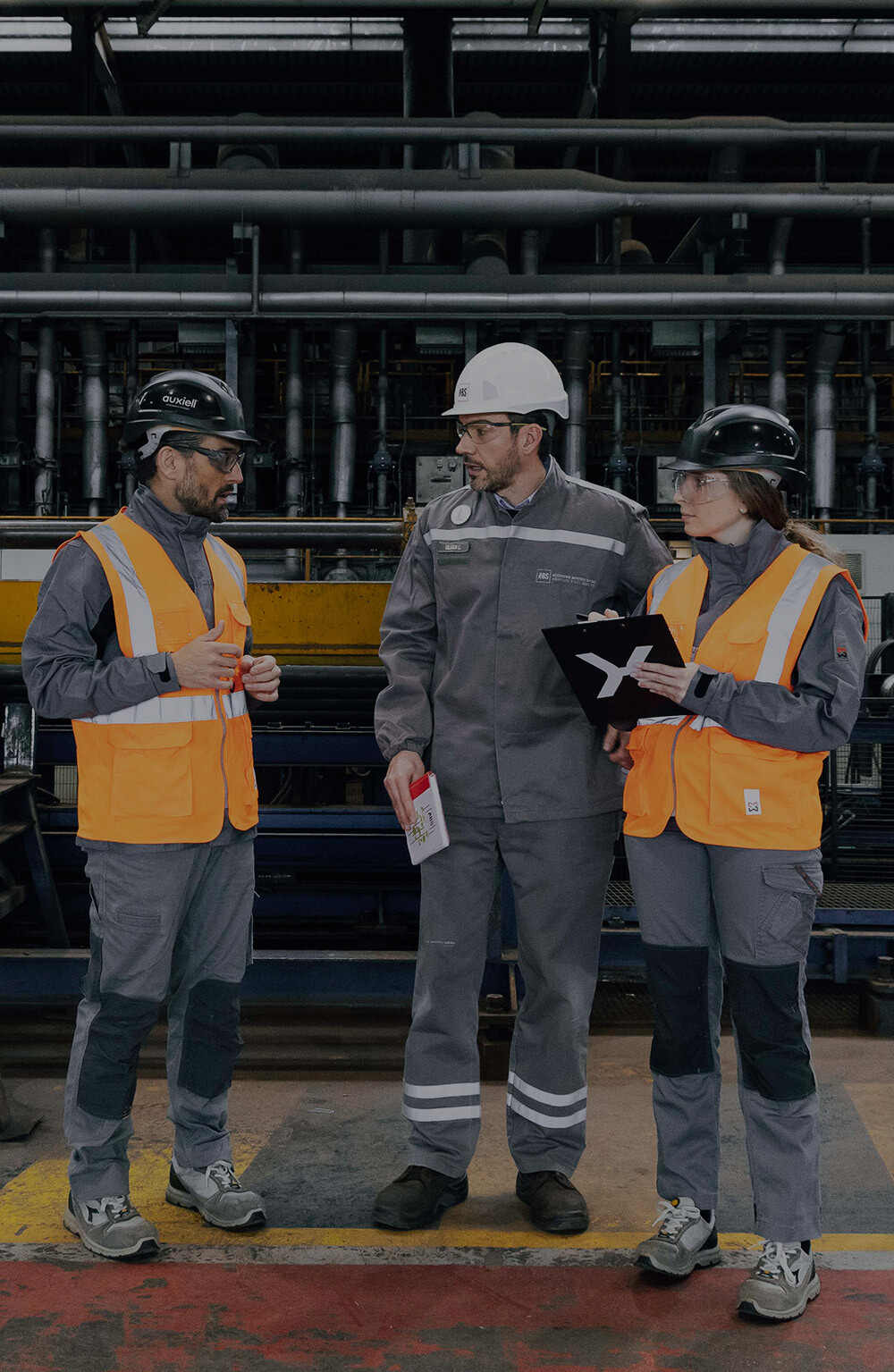
Siamo una società di consulenza che guida organizzazioni e persone nel diventare degli esempi
Vuoi migliorare le performance della tua azienda?
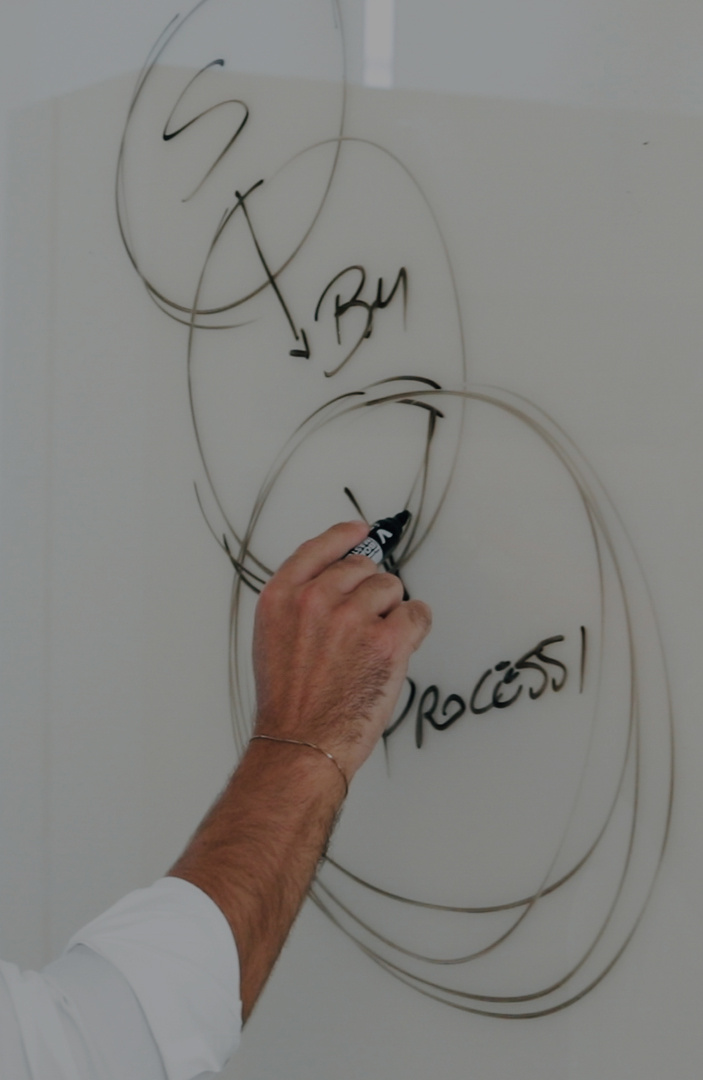
Cosa facciamo
Analizziamo, riprogettiamo e trasformiamo i processi delle aziende che vogliono aumentare le proprie performance
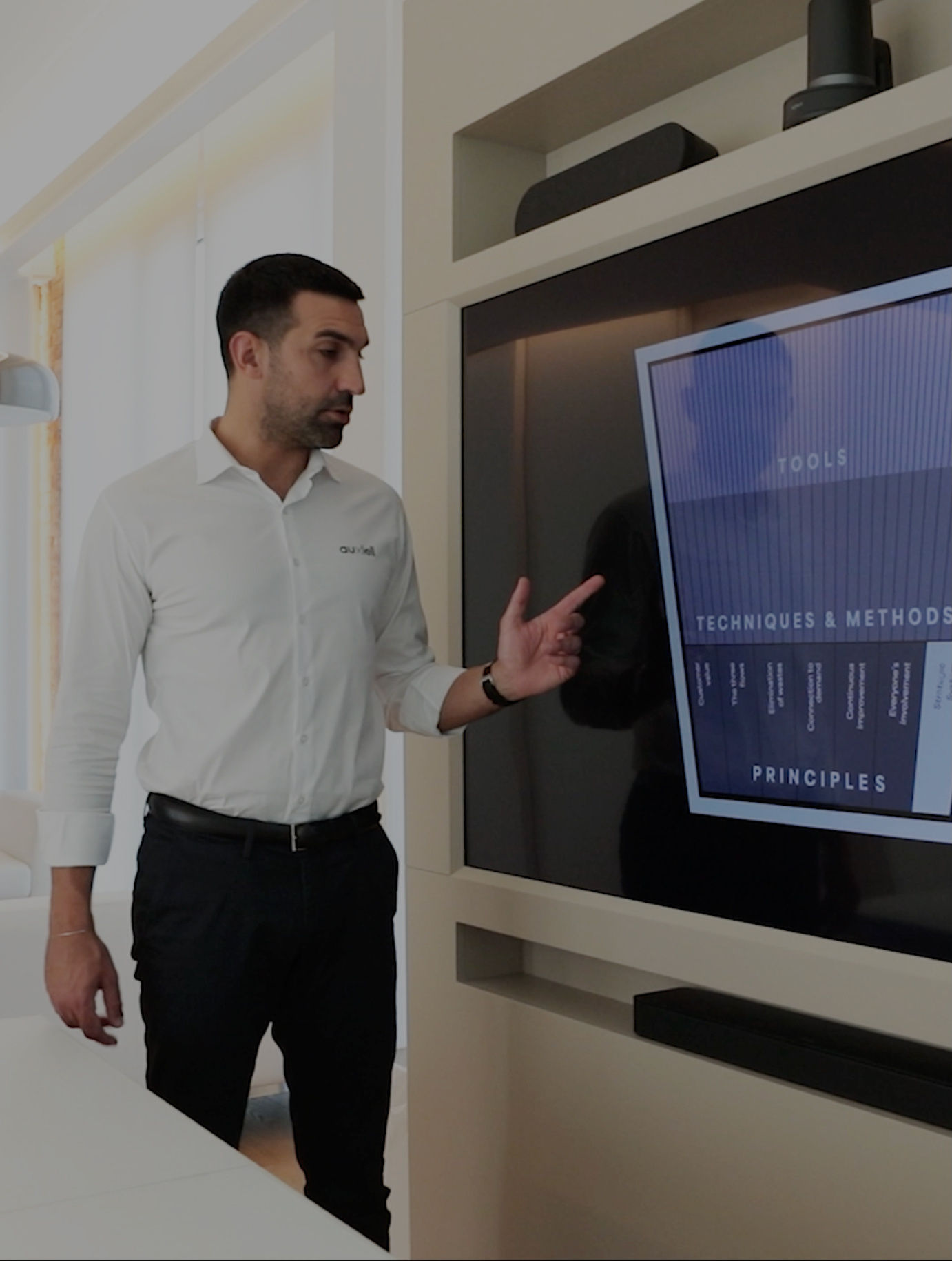
Come lo facciamo
Per trasformare i processi adottiamo un approccio pratico e pragmatico: siamo coinvolti in prima persona nella trasformazione
-
Arredamento
-
Occhialeria
-
Calzaturiero
-
Fashion
-
Food & beverage
-
Metalmeccanico
-
Grande distribuzione organizzata
-
Elettronica
-
Automazione & meccatronica
-
Metallurgico
-
Meccanica generale
-
Chimico
-
Legno e carta
-
Gomma
-
Materie plastiche
-
Logistica & trasporti
-
Farmaceutico
-
Cosmetico
-
Biomedicale
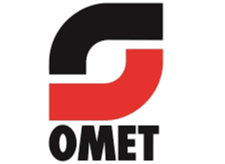
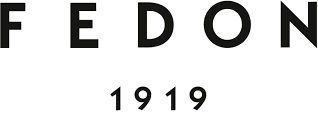
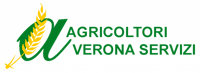

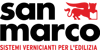
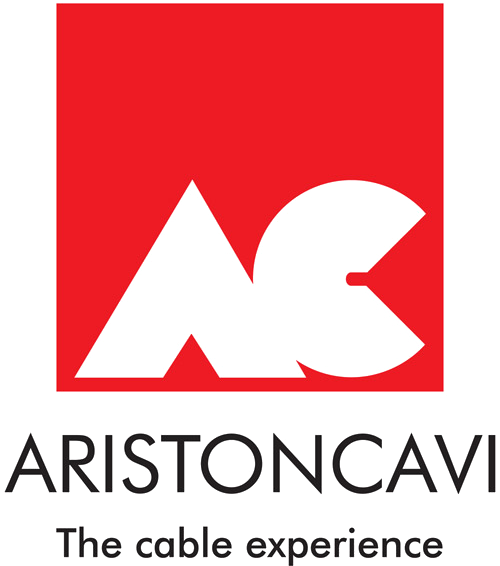
-2.png?width=713&height=685&name=AcciaierieBertoliSafau%20(1)-2.png)
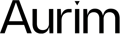
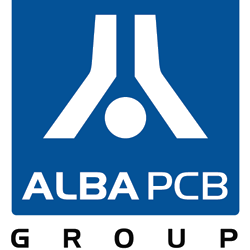


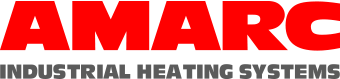

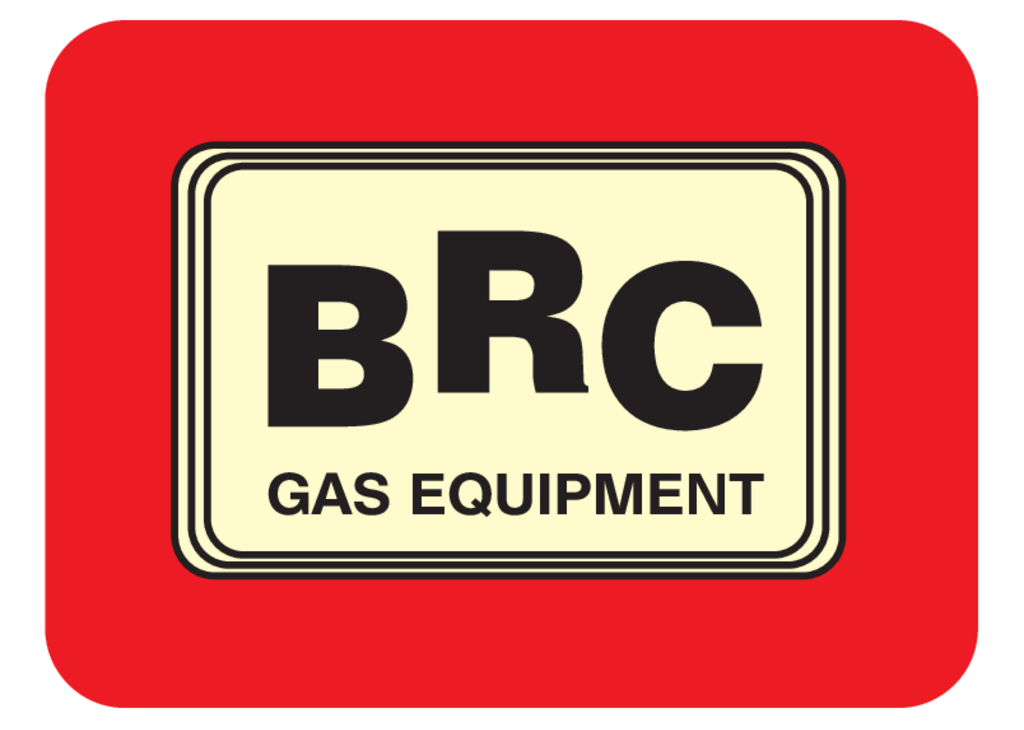
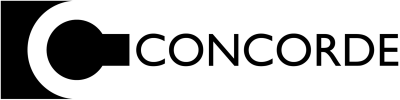
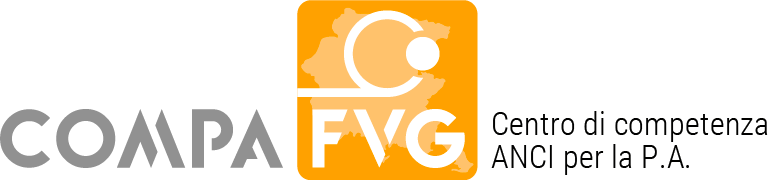
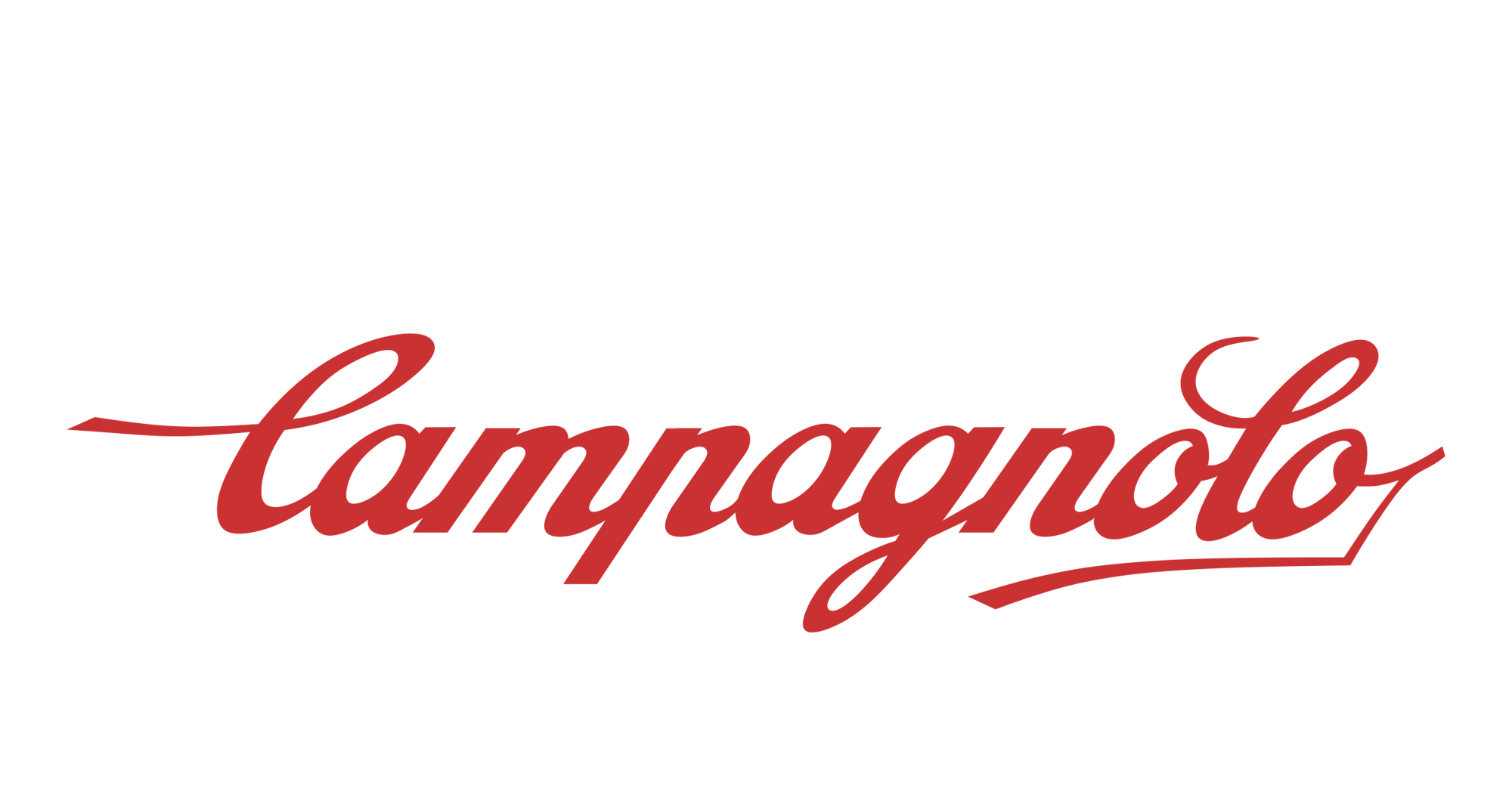
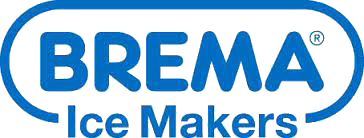
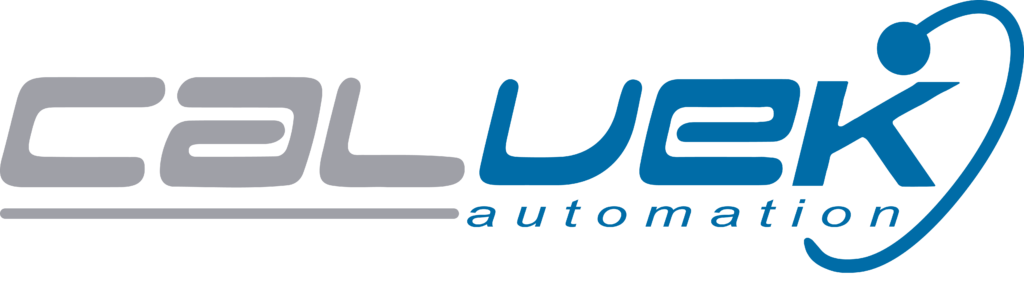
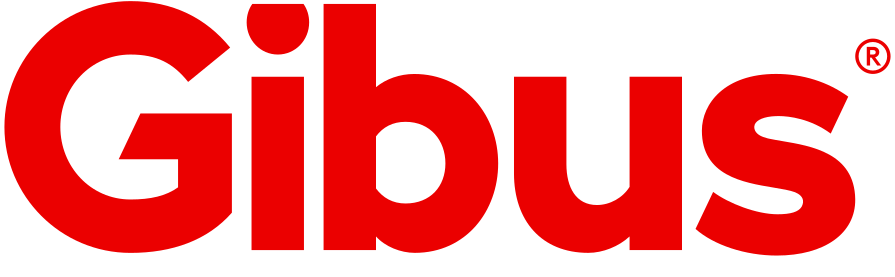
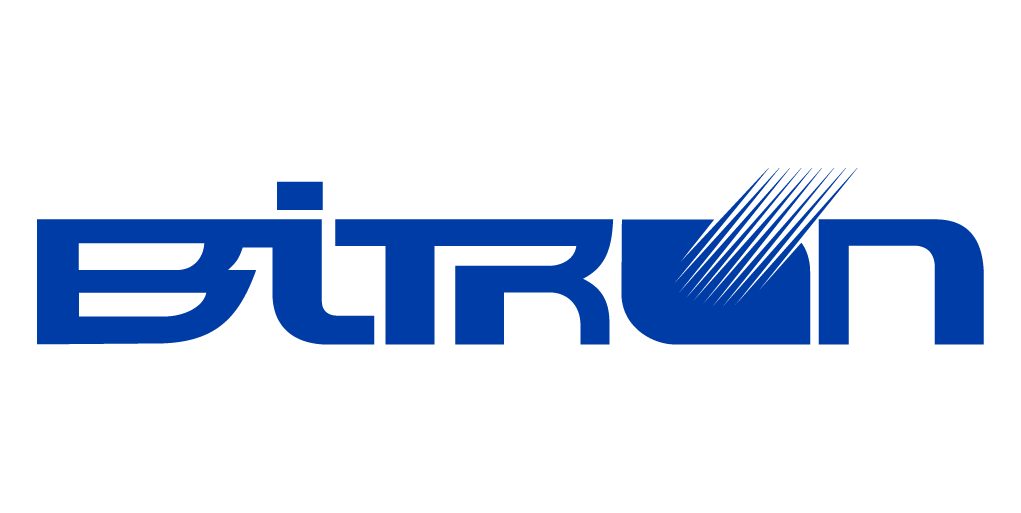
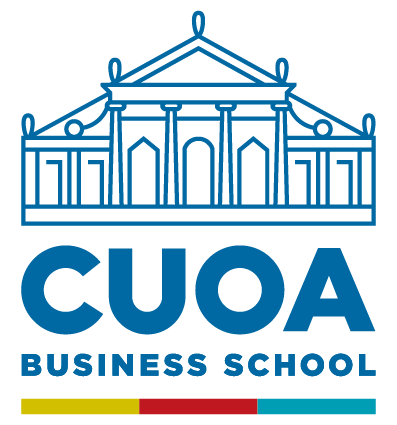
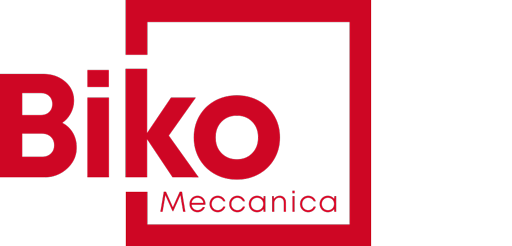
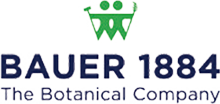
.svg.png?width=1200&height=480&name=Barilla_brand_logo_(2022-present).svg.png)
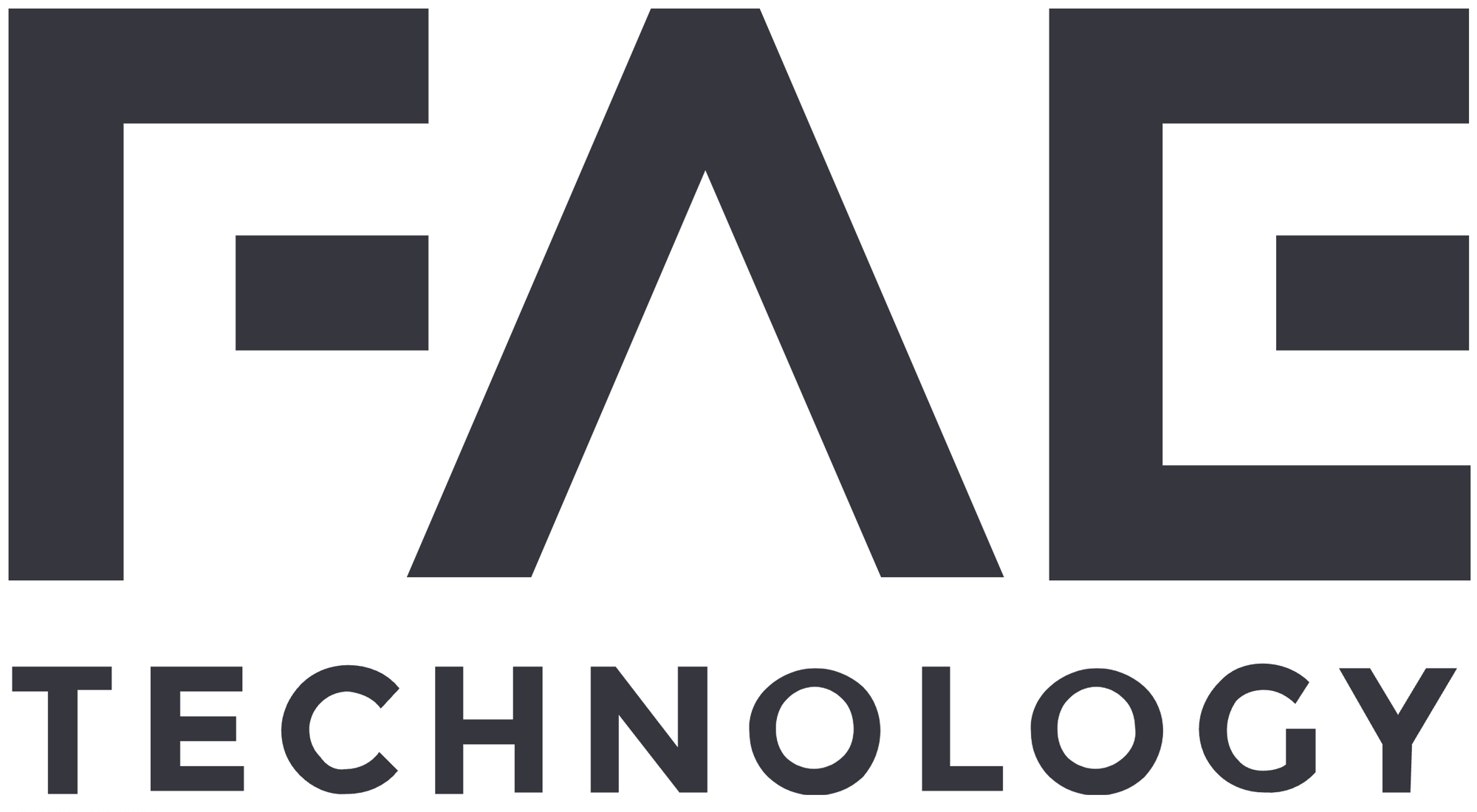
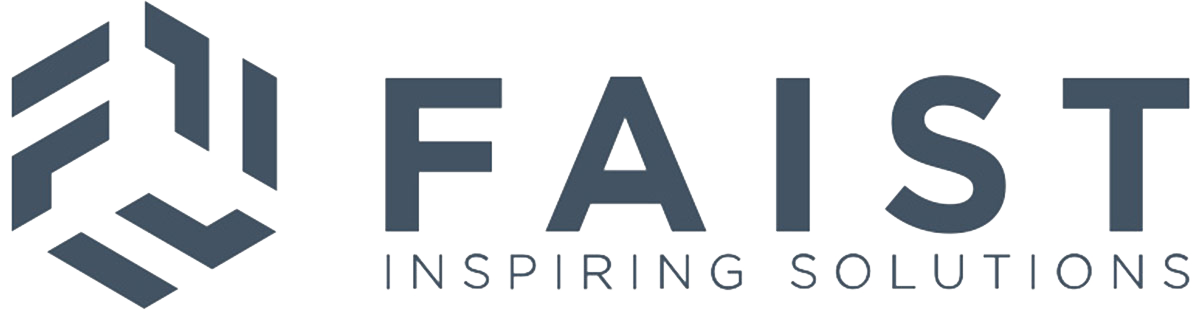
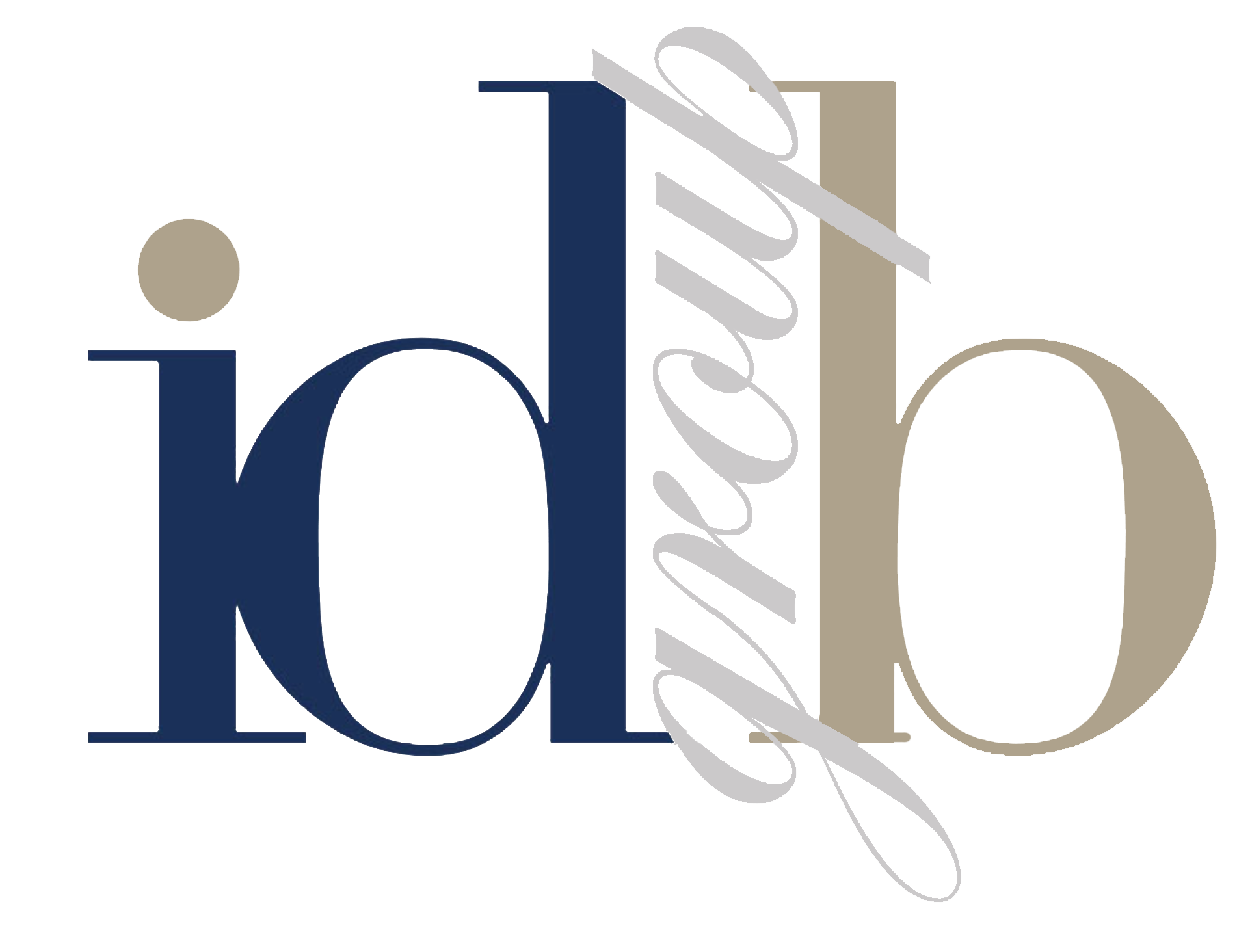
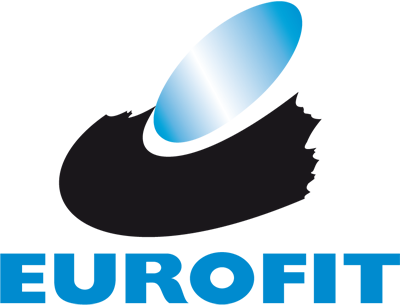

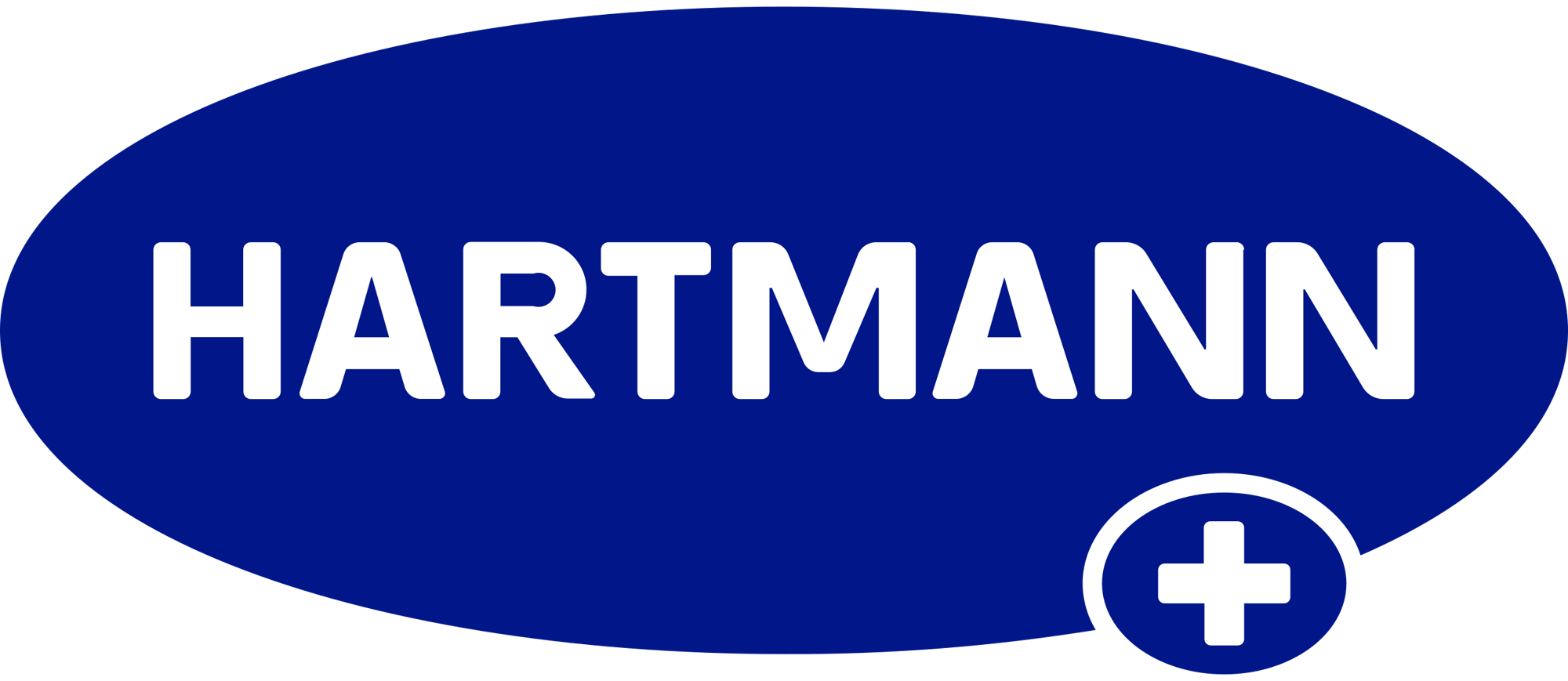
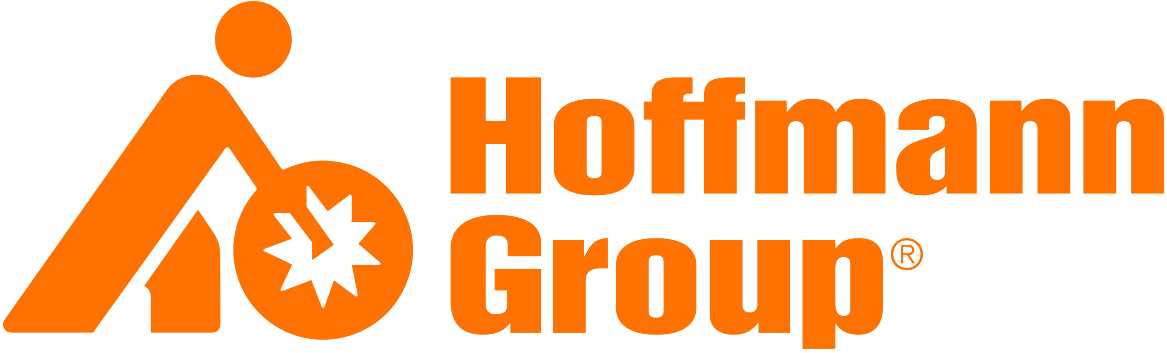
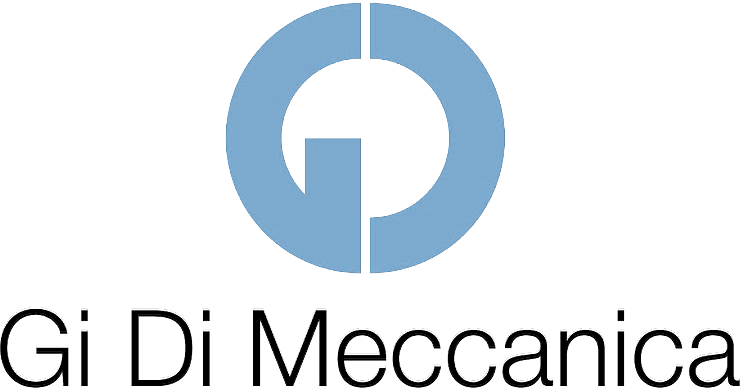
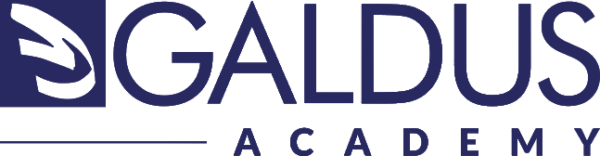
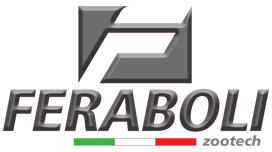
-2.png?width=713&height=685&name=AcciaierieBertoliSafau%20(1)-2.png)
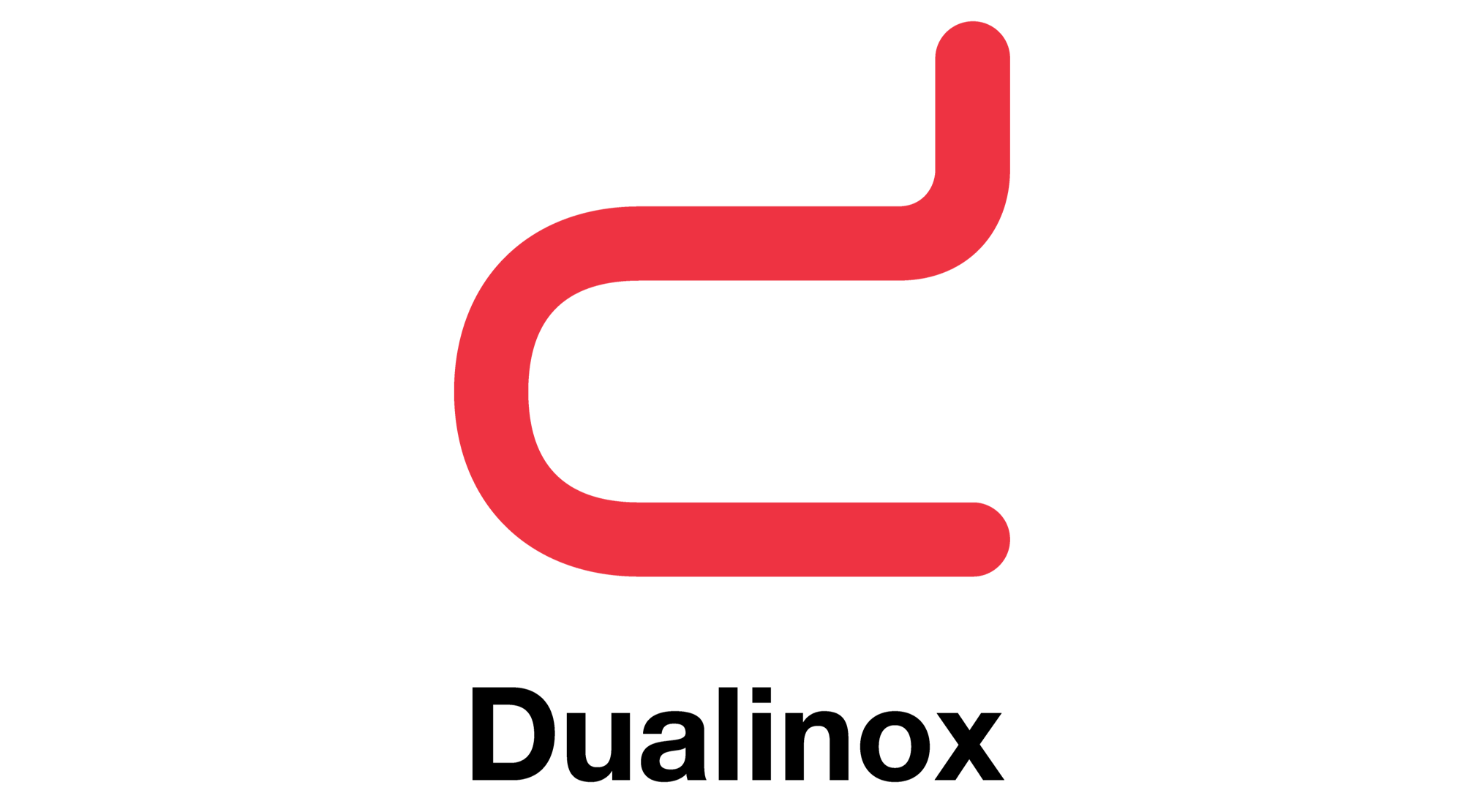
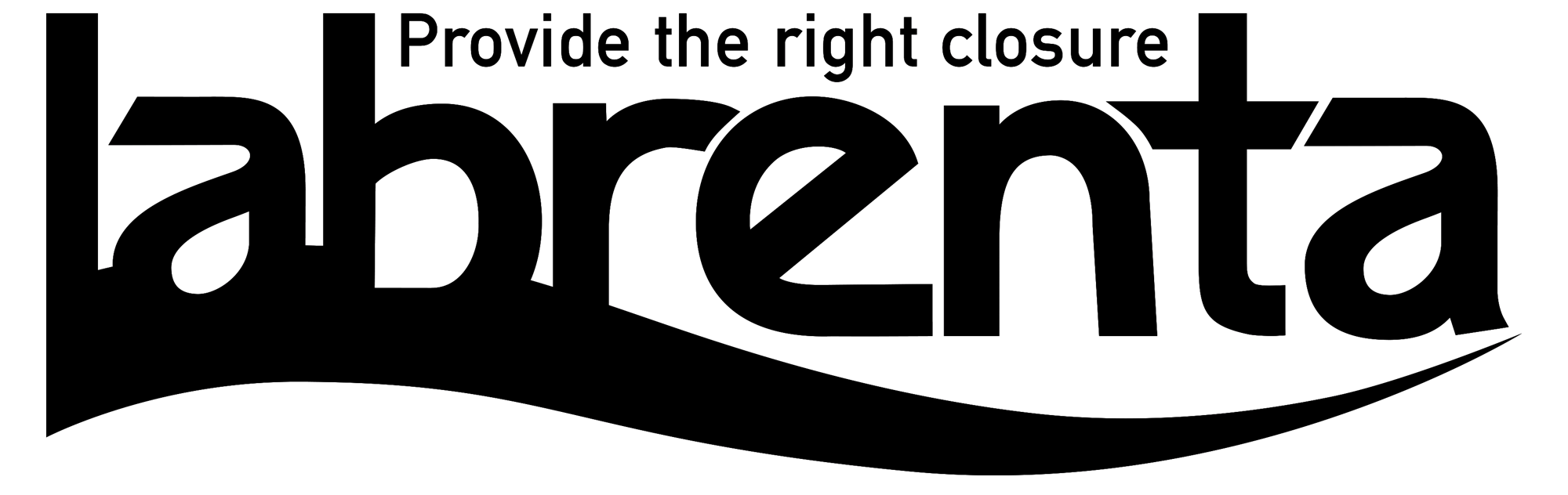

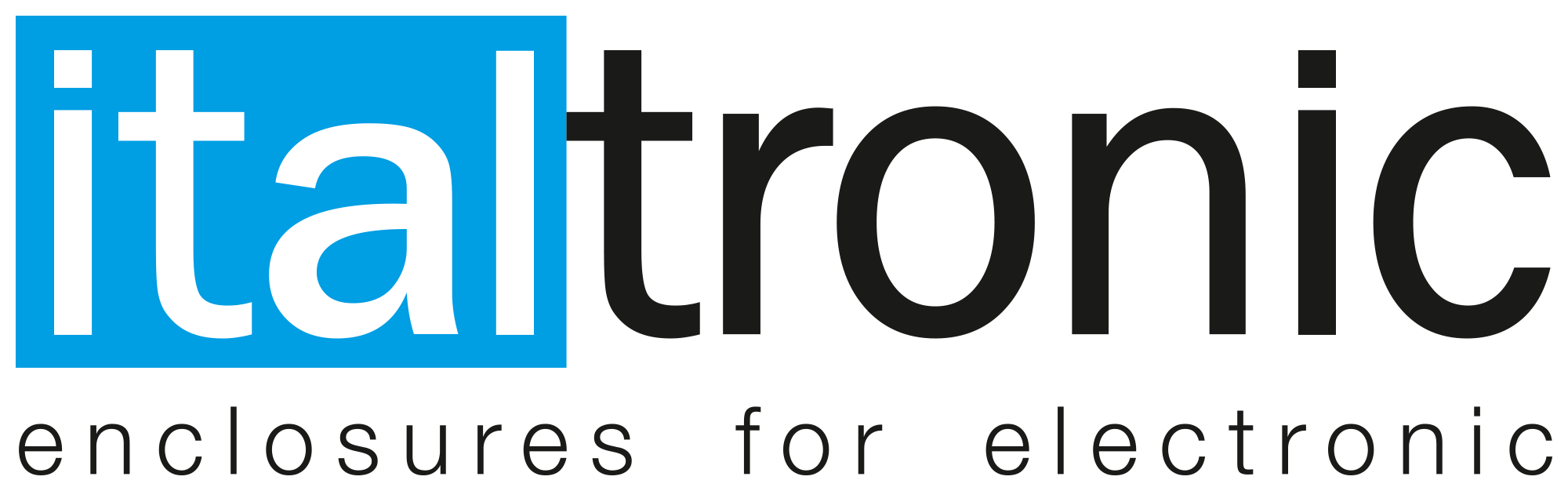
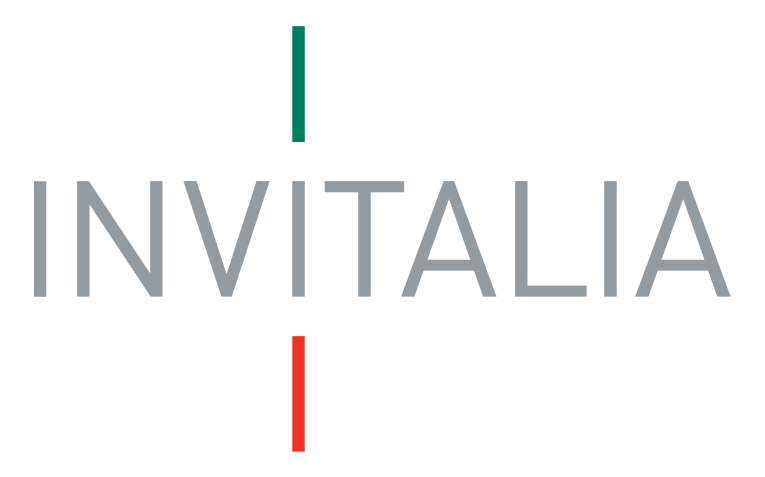
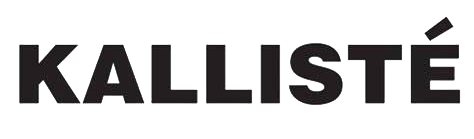
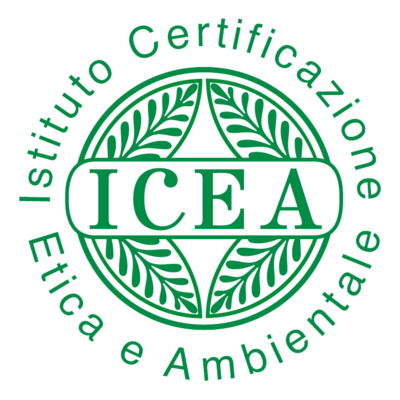
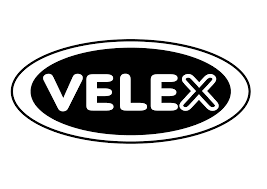
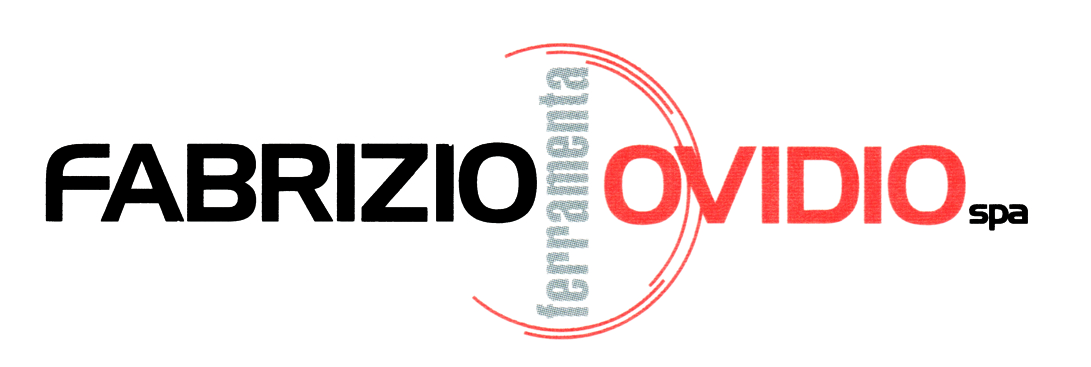
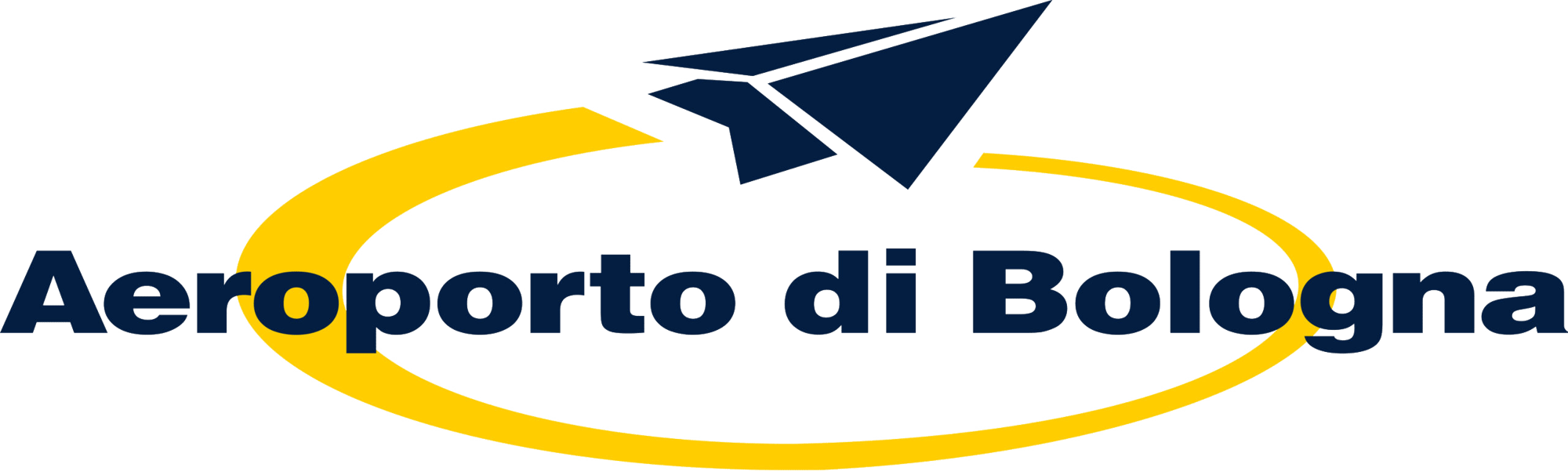
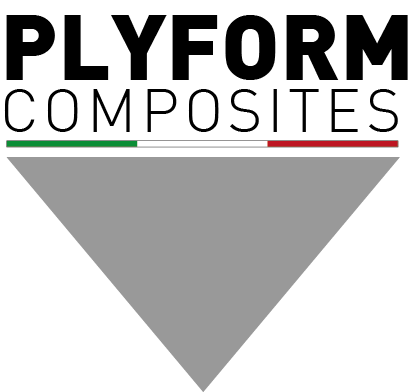
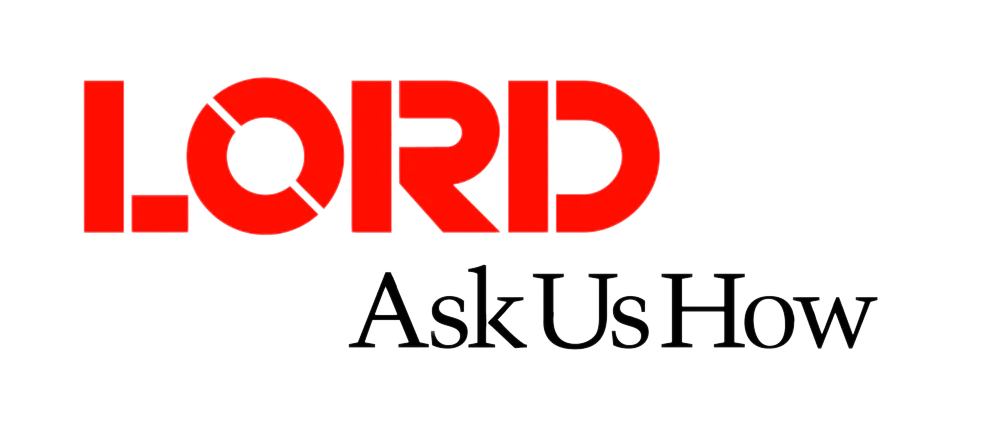
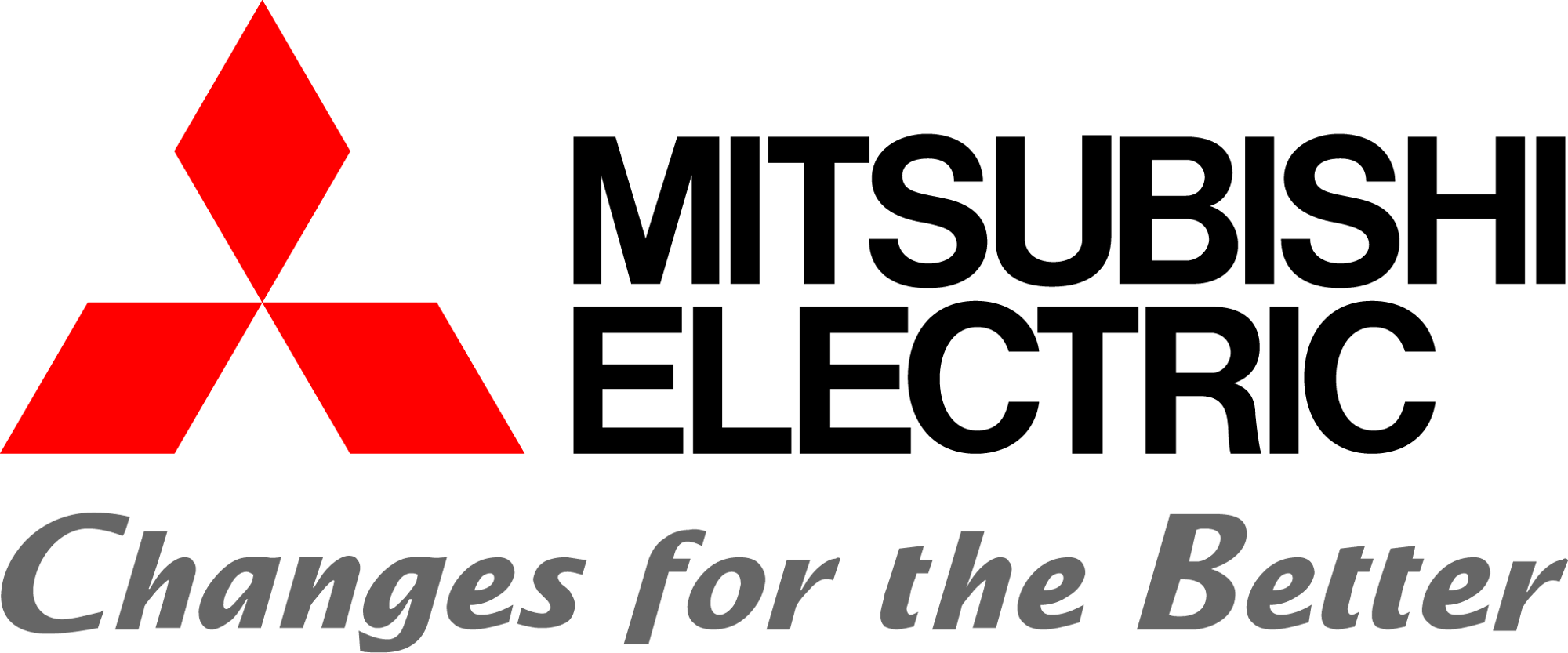
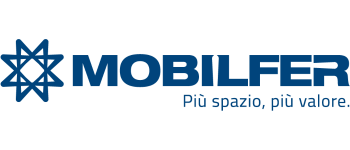
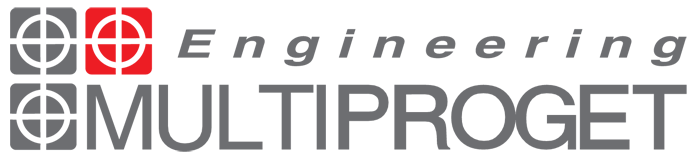
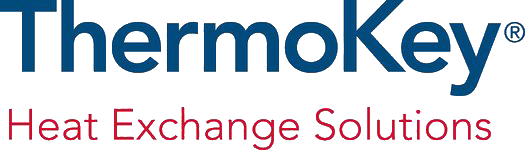
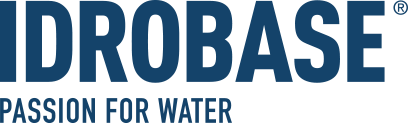
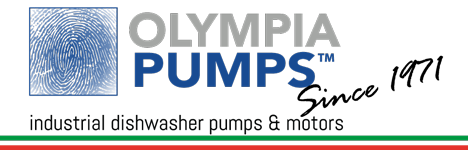
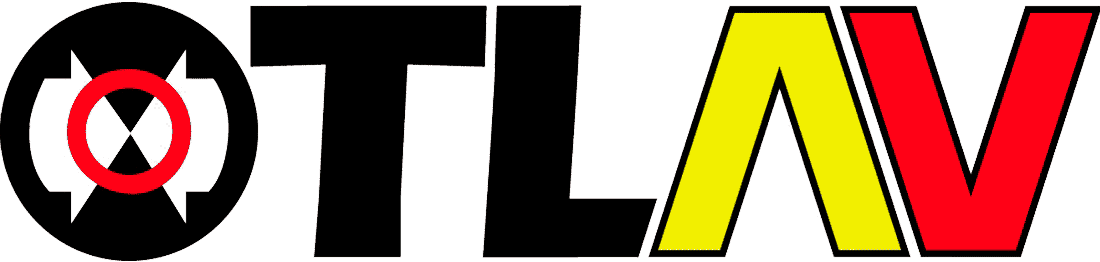
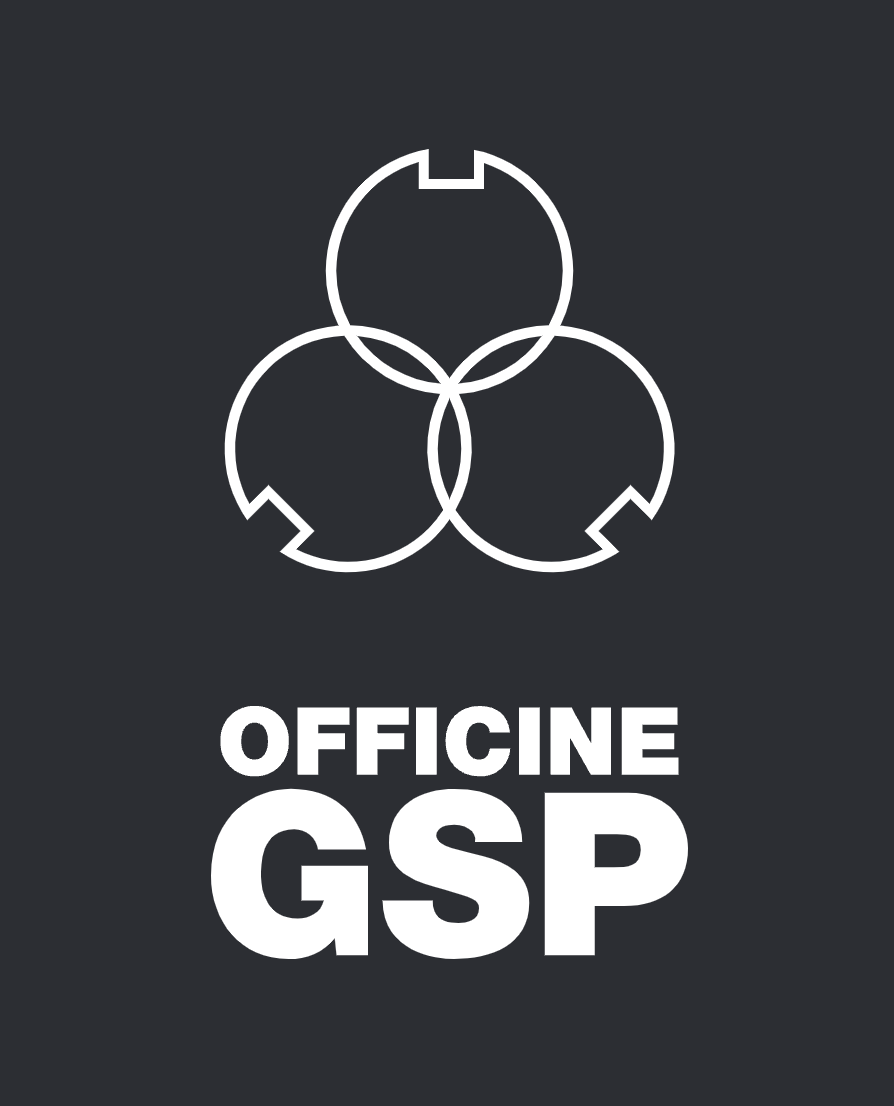
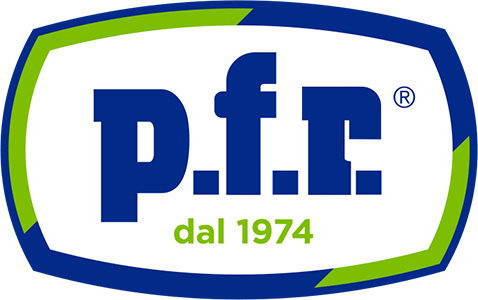
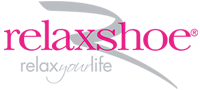
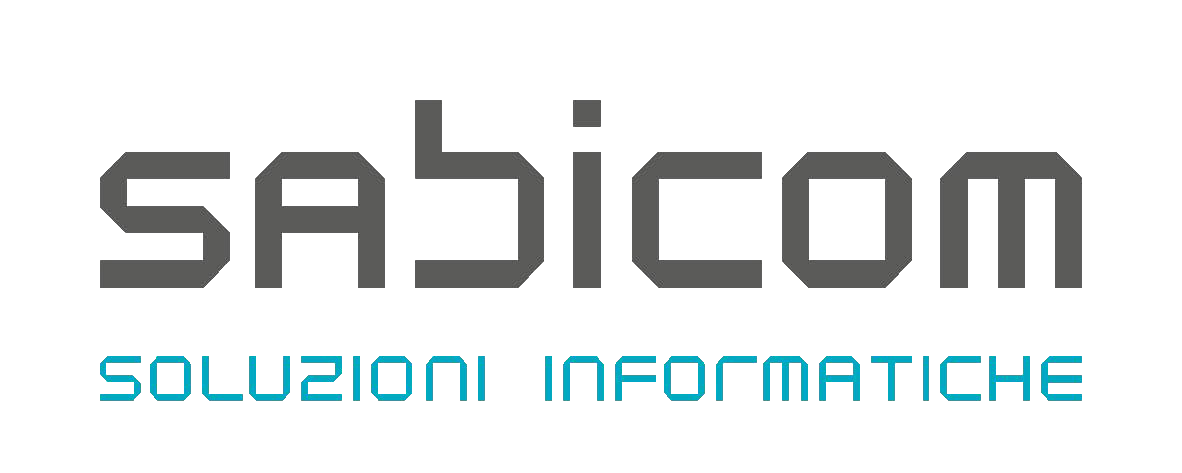
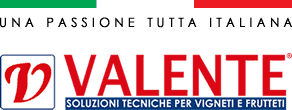

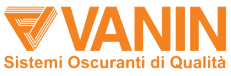
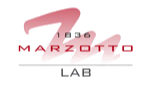

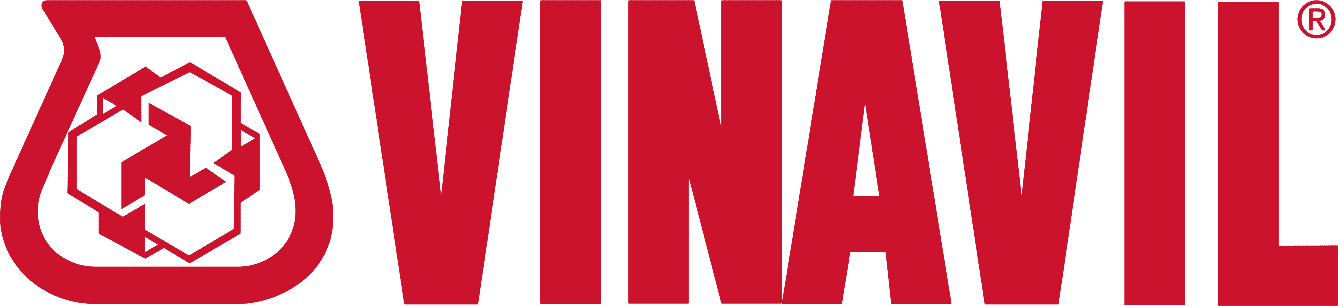
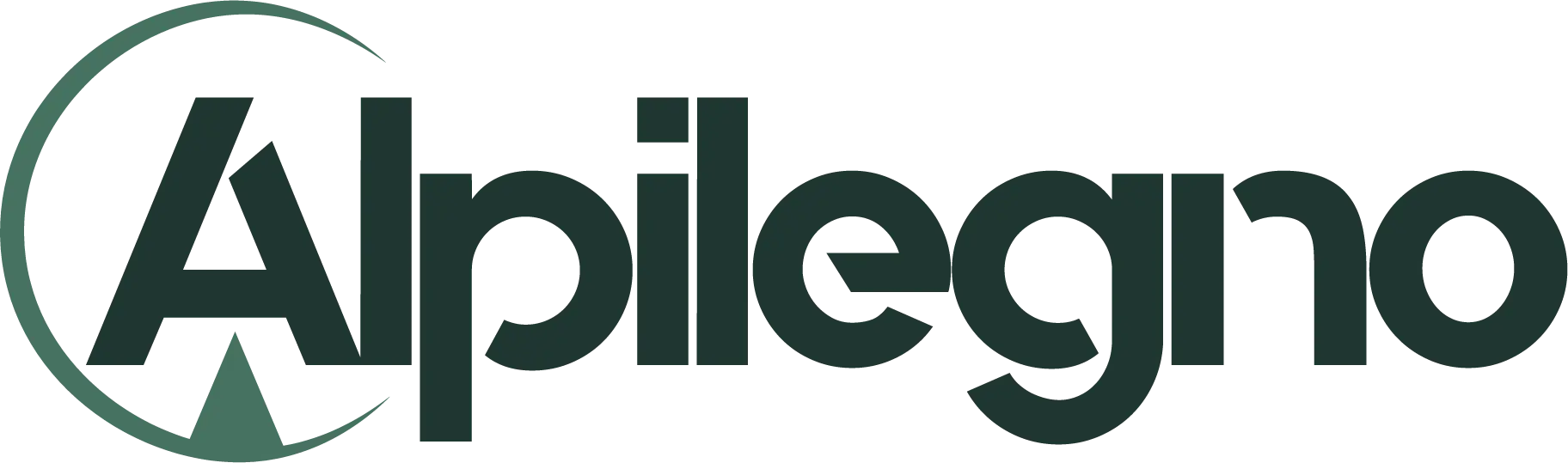
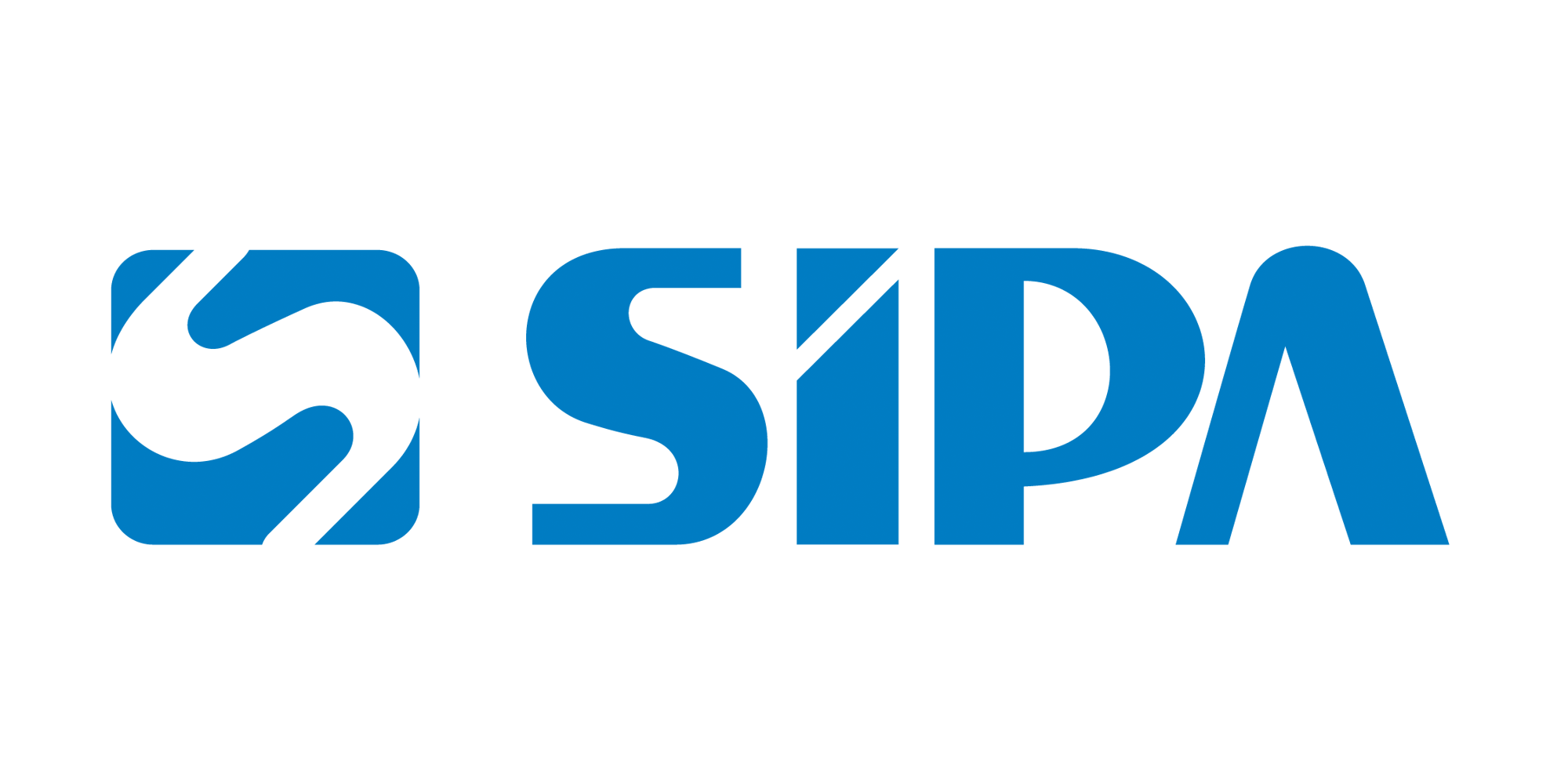
-2.png?width=713&height=685&name=AcciaierieBertoliSafau%20(1)-2.png)
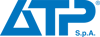
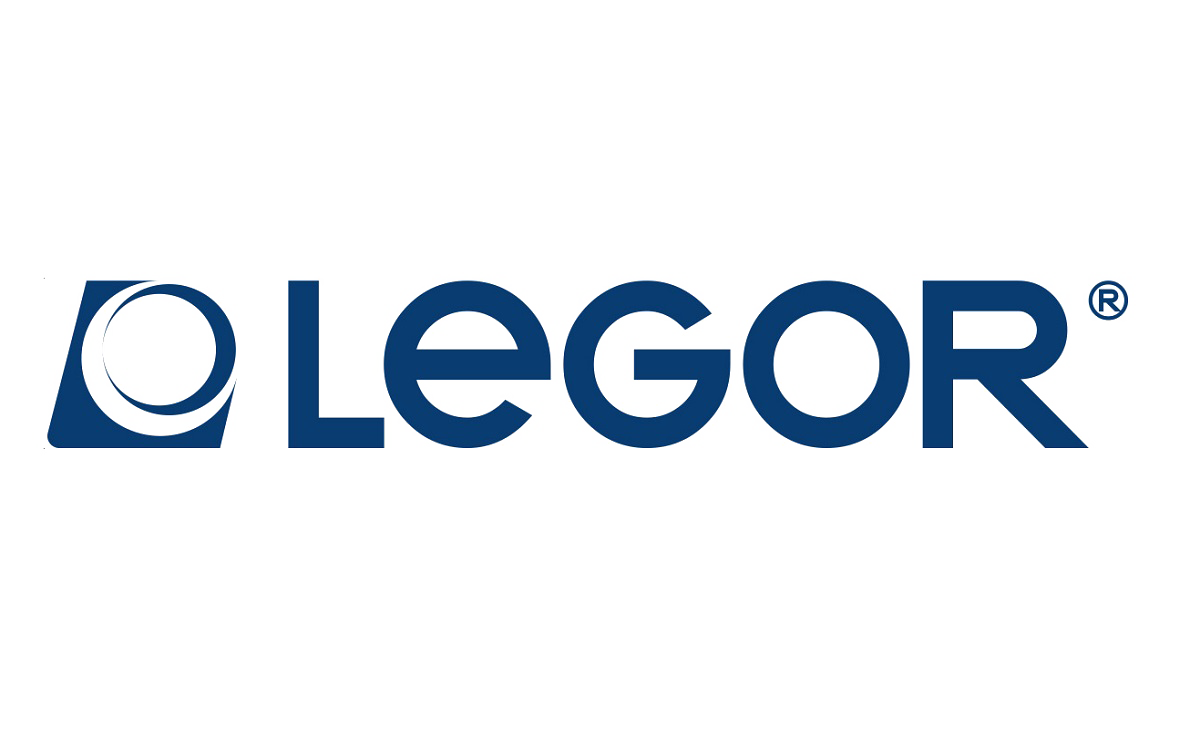
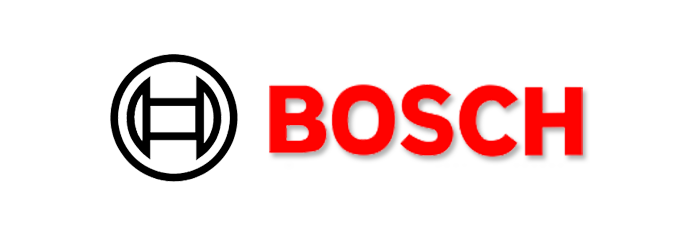
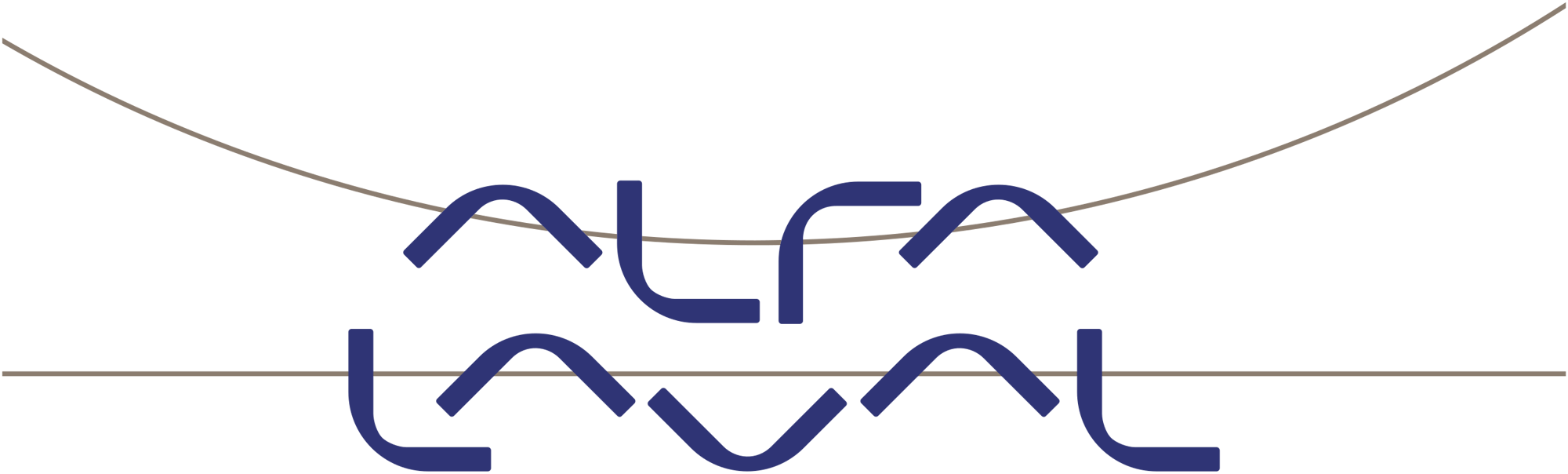
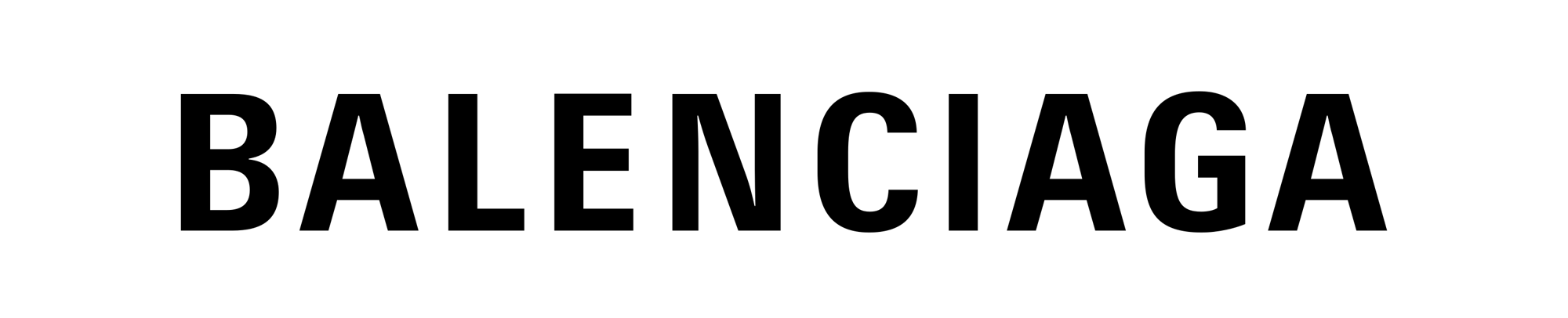
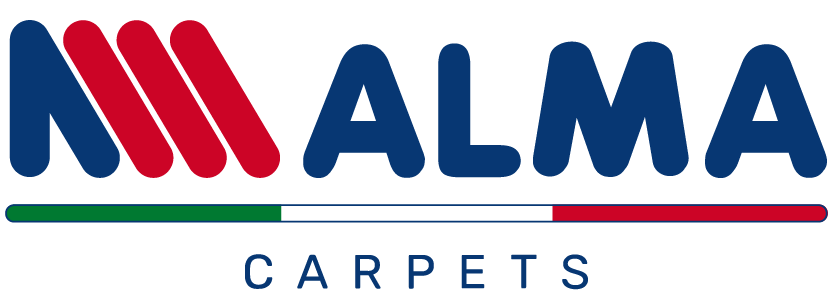
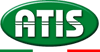
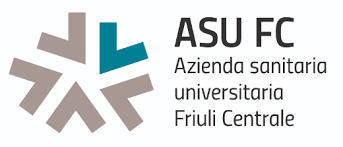
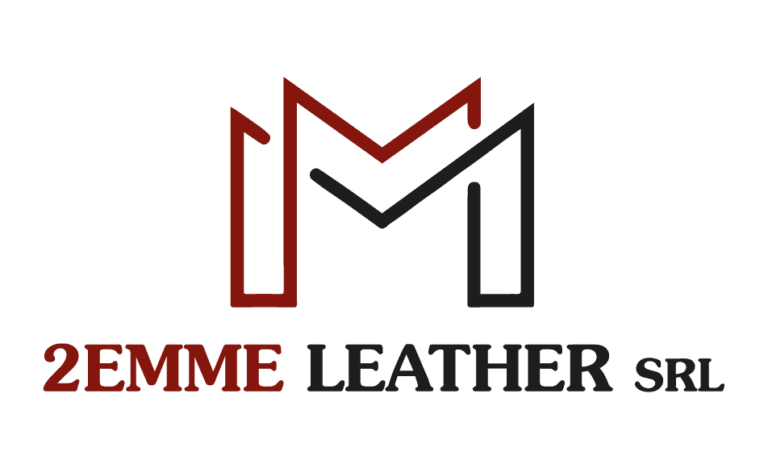
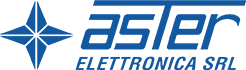
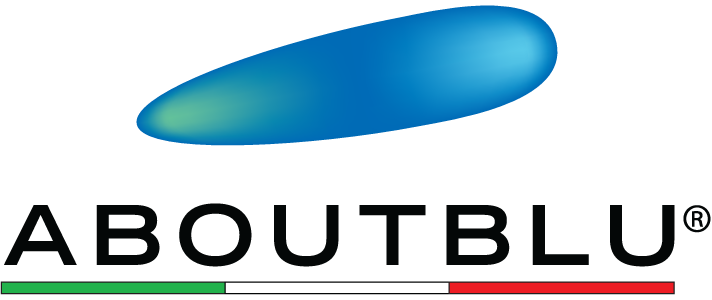
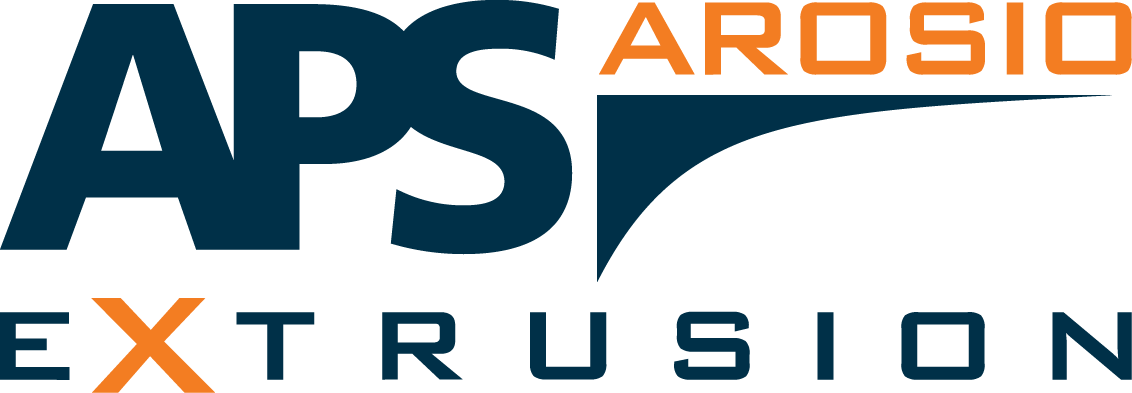
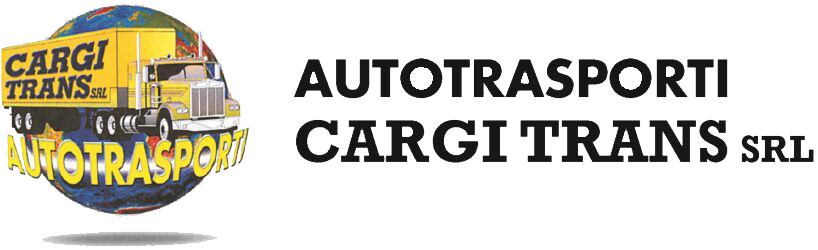
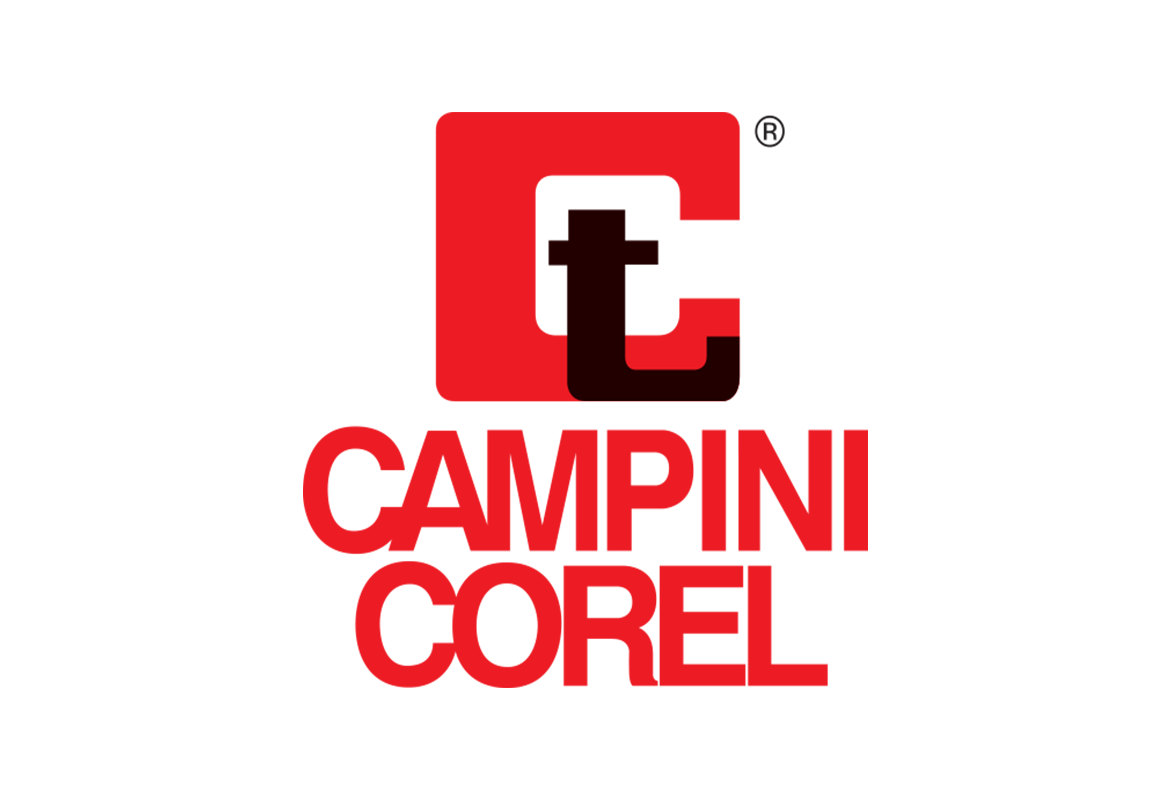
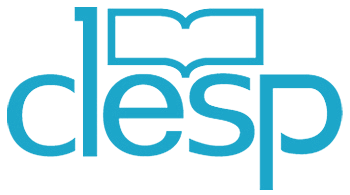
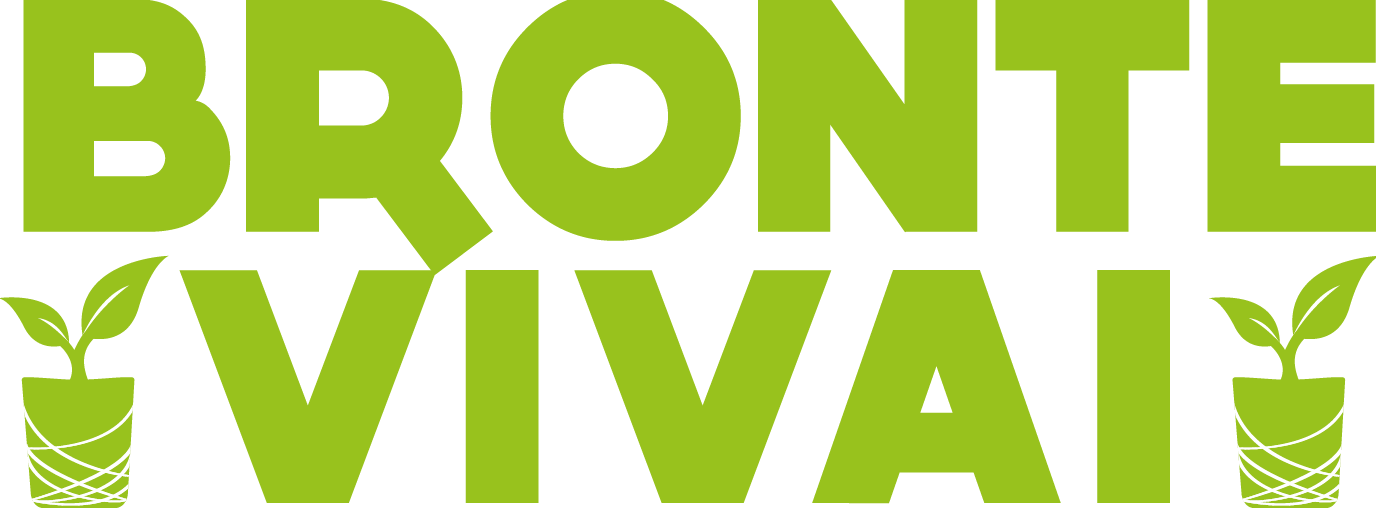
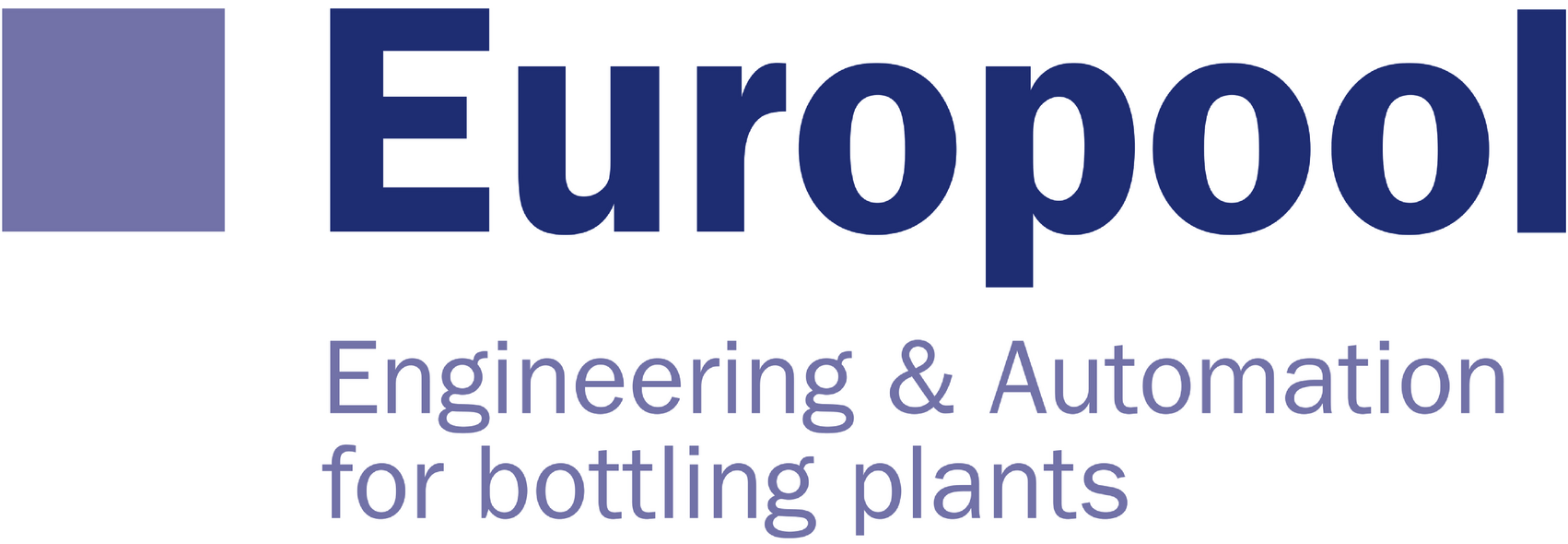
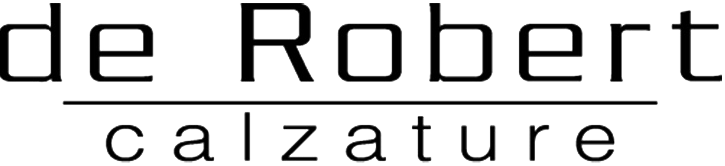
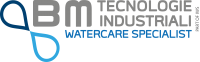
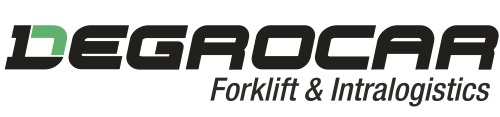
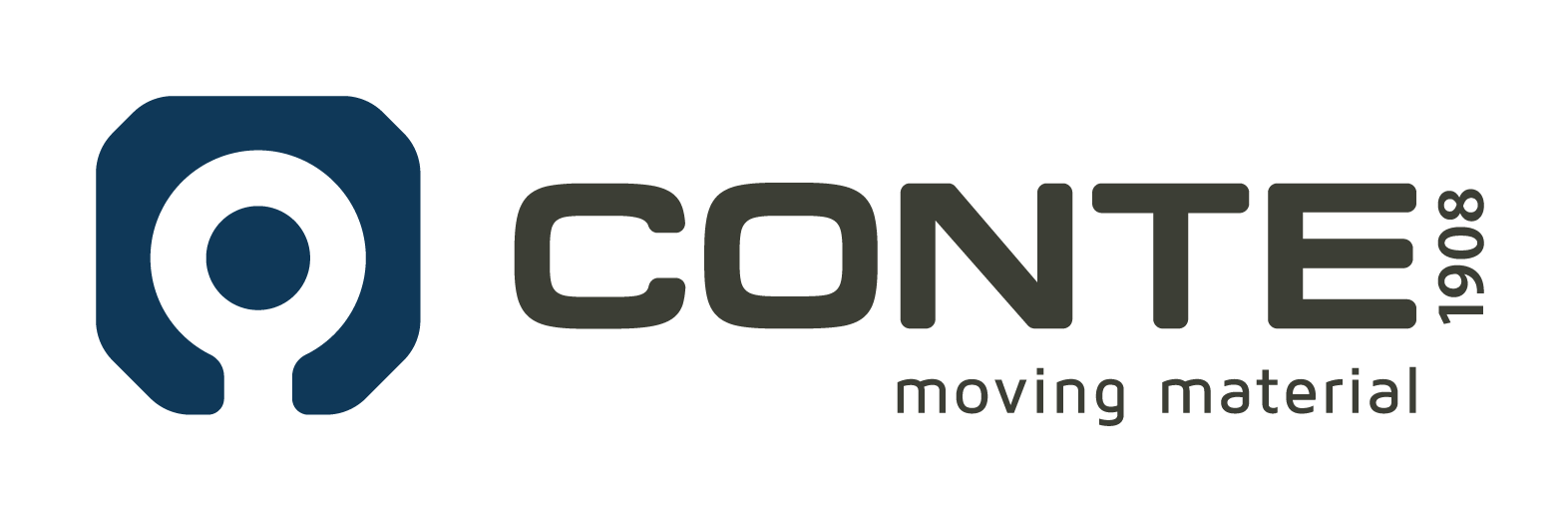

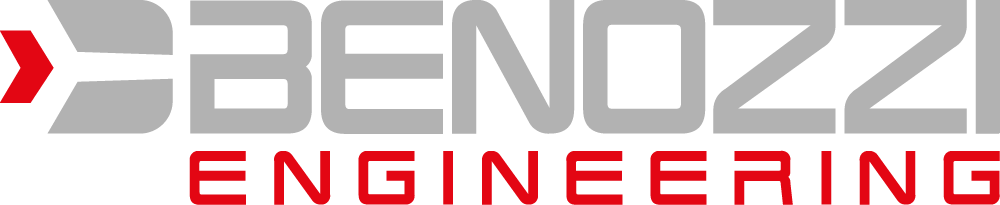
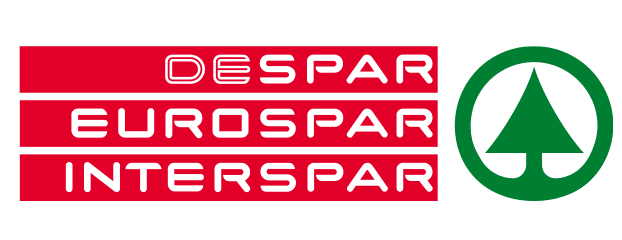
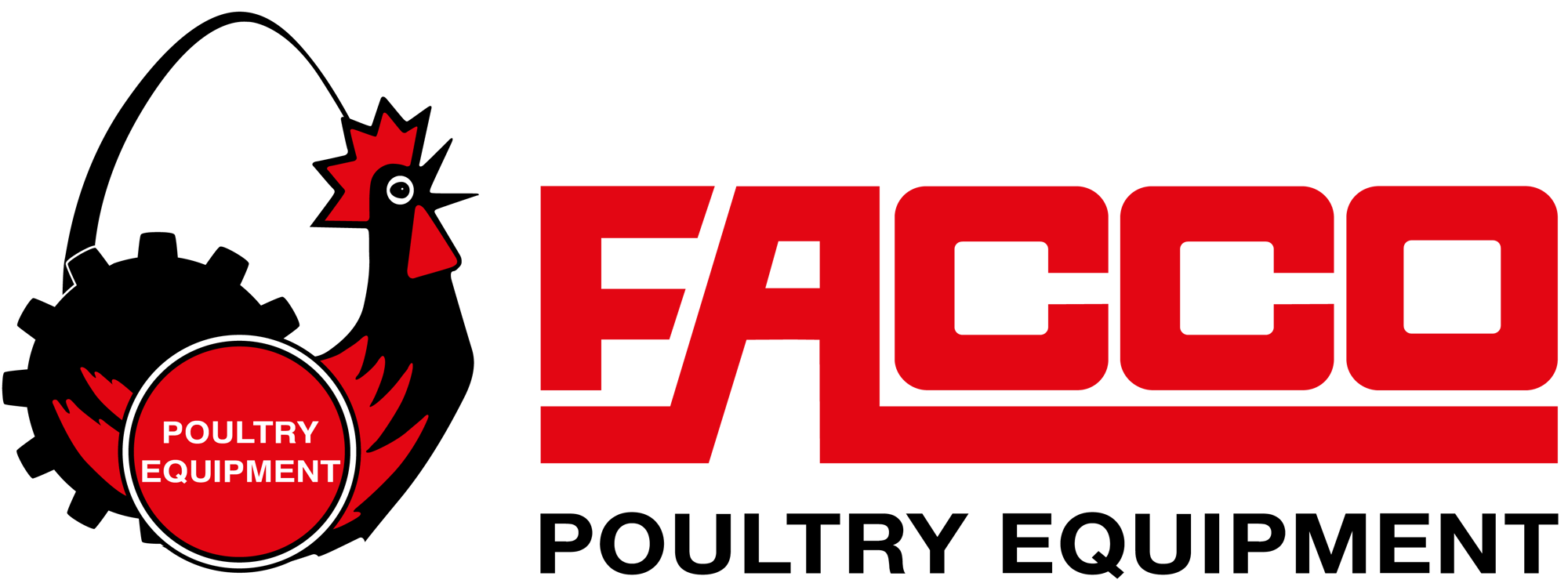
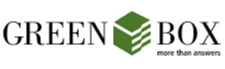
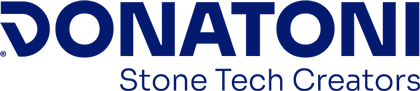
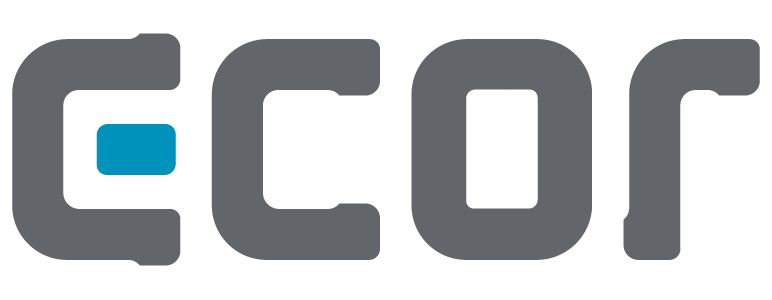
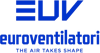
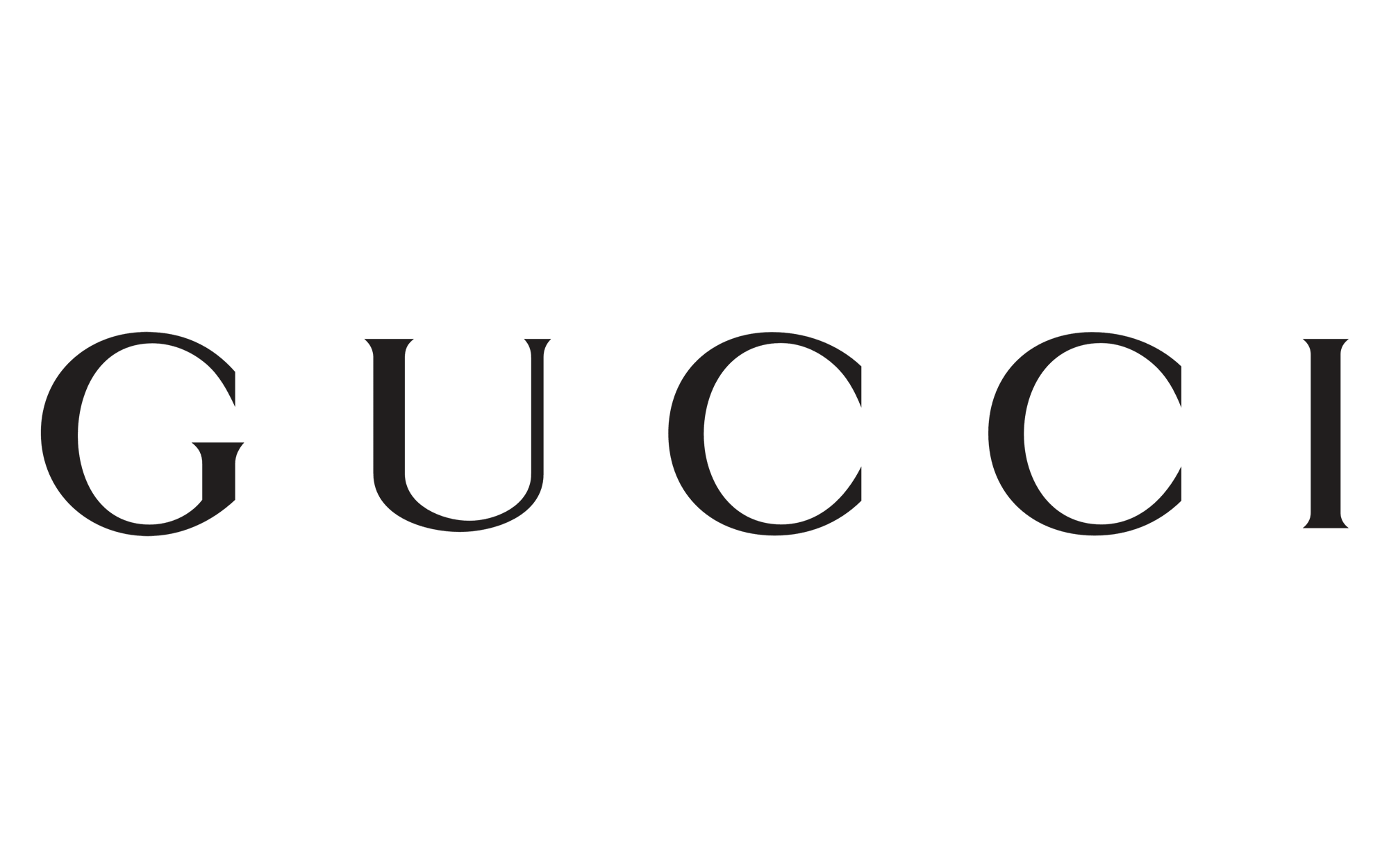
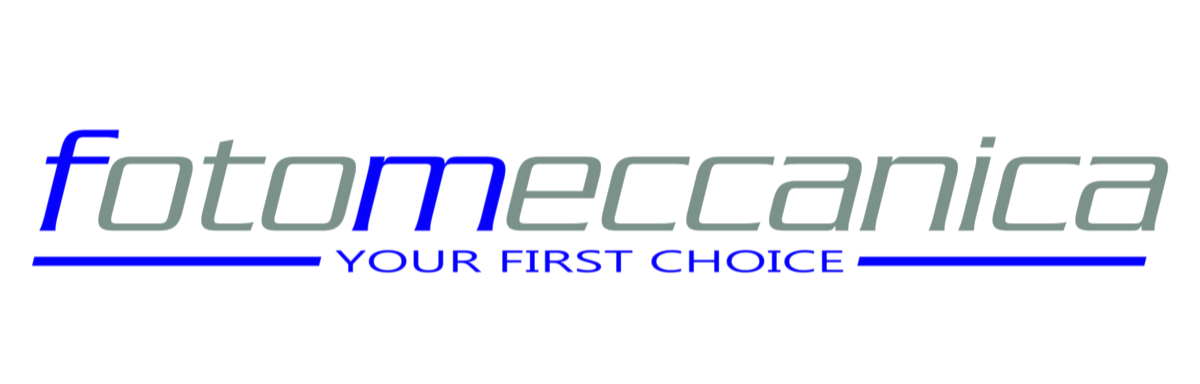
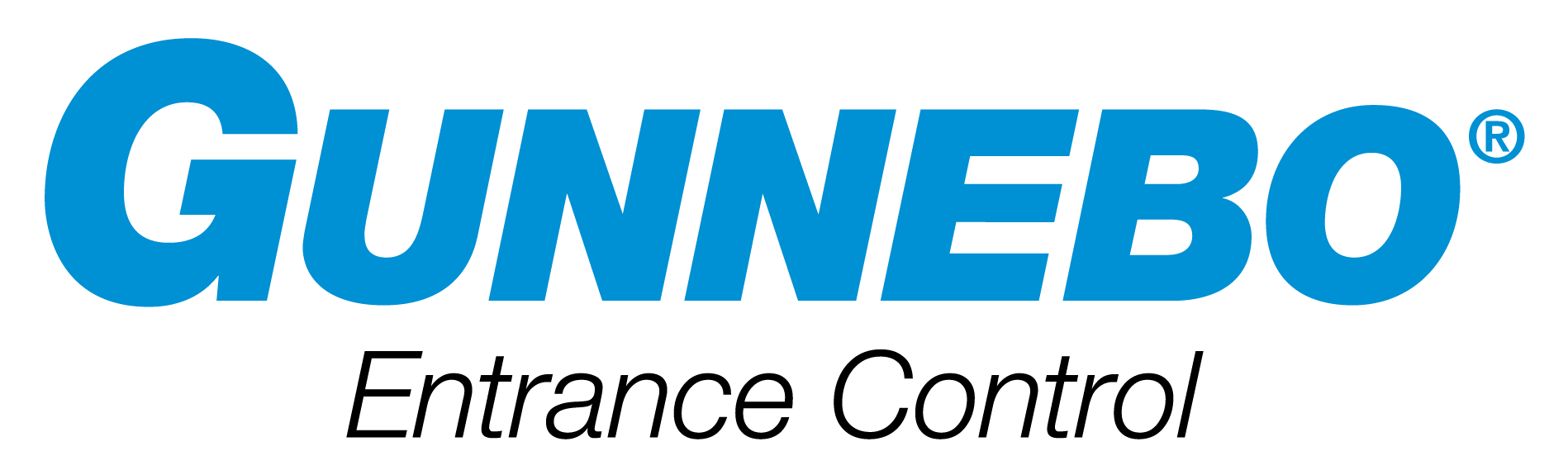
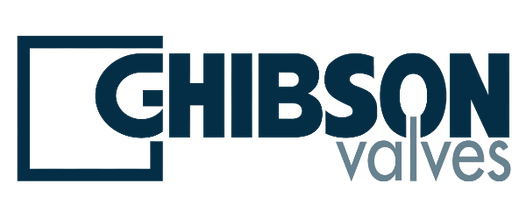
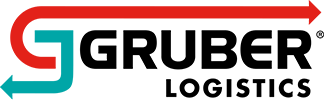
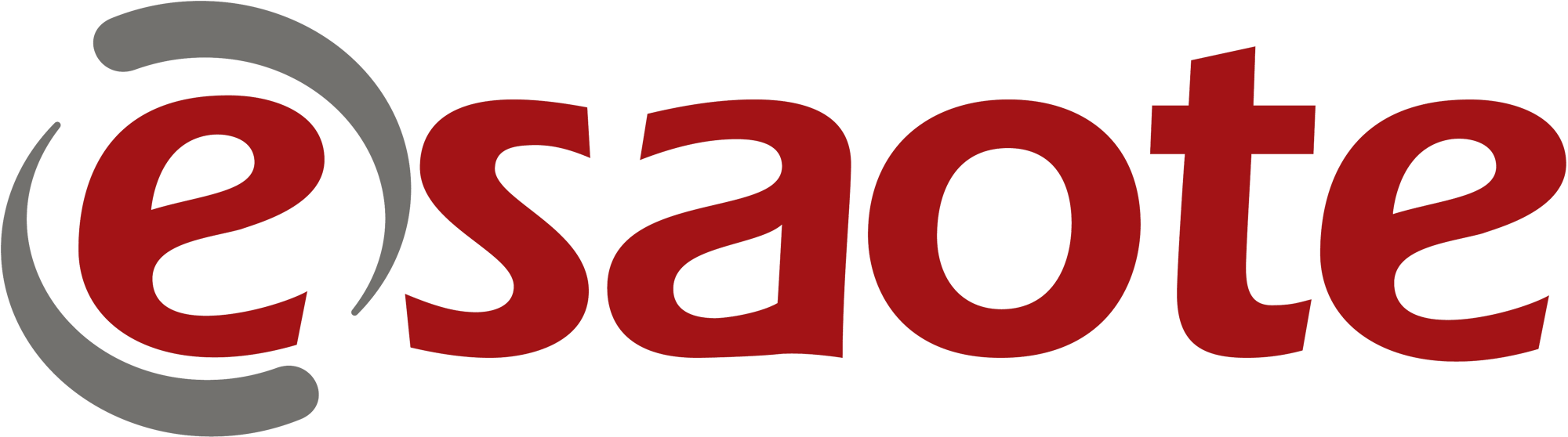
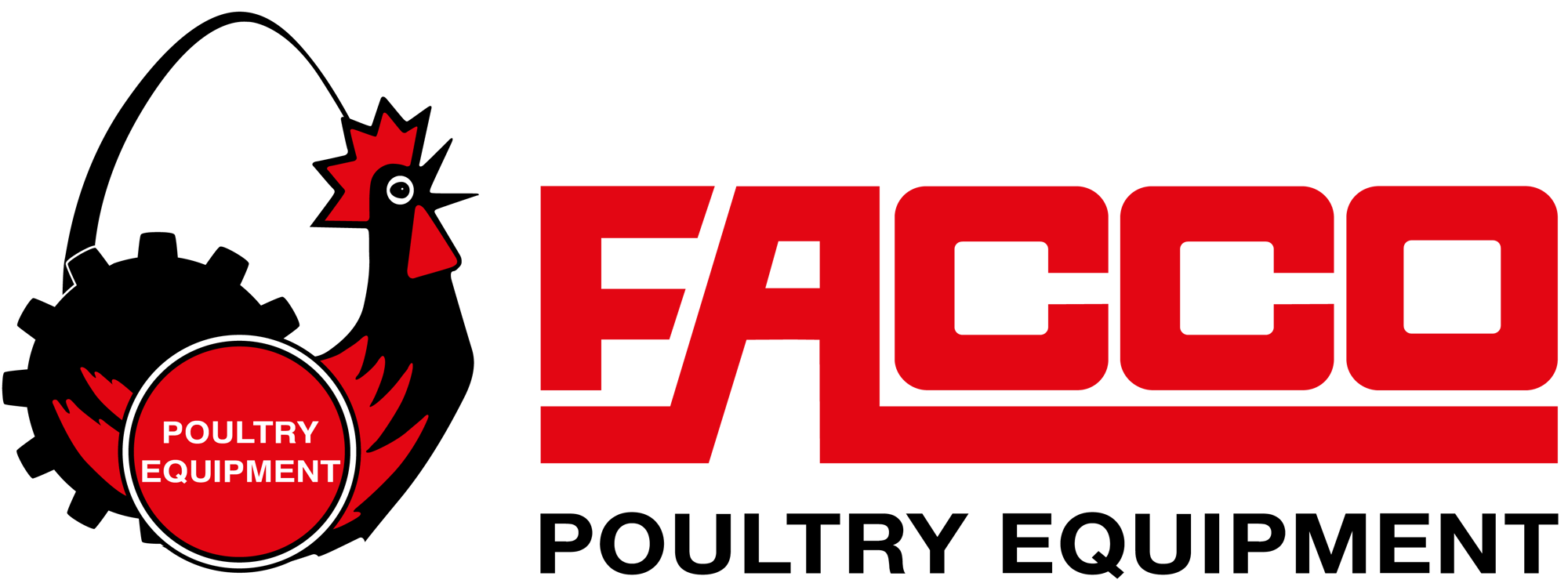
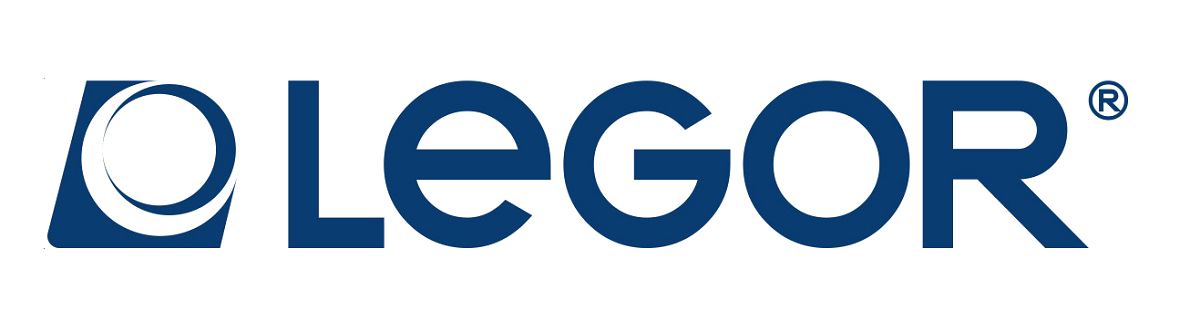
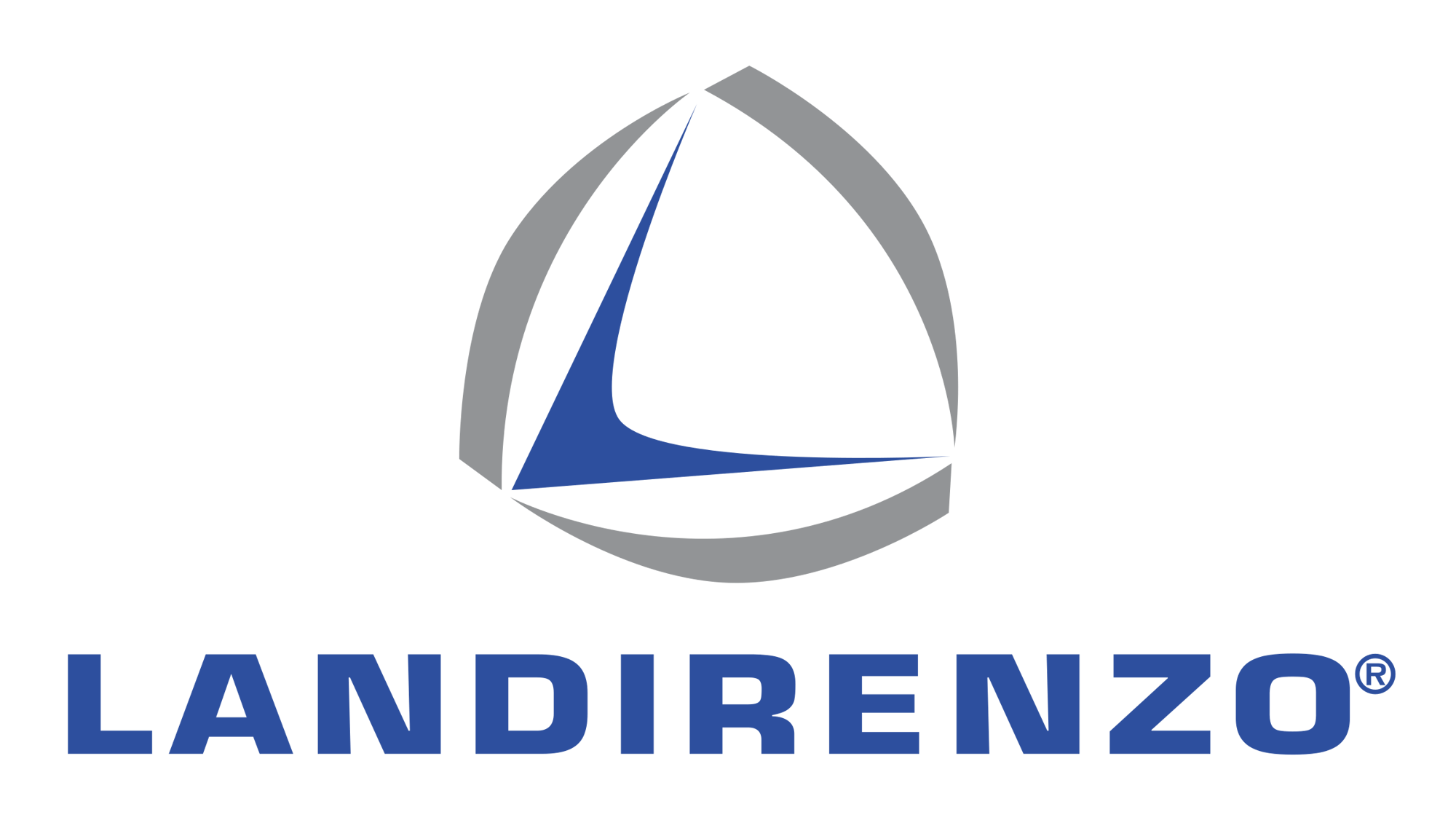
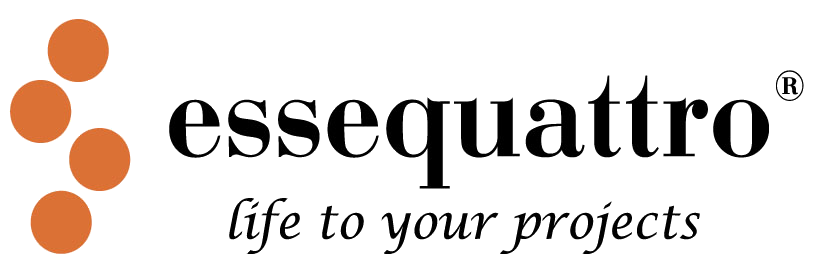
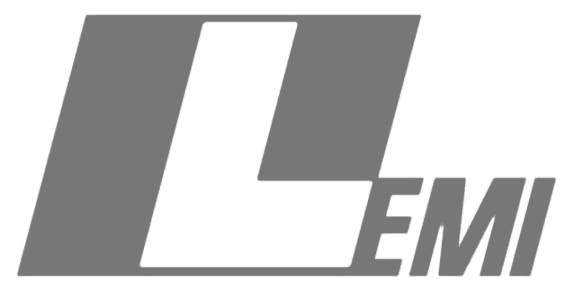
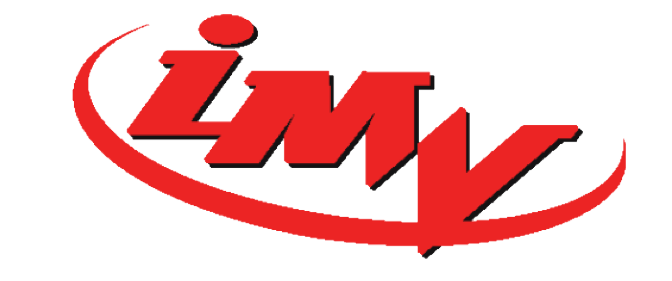

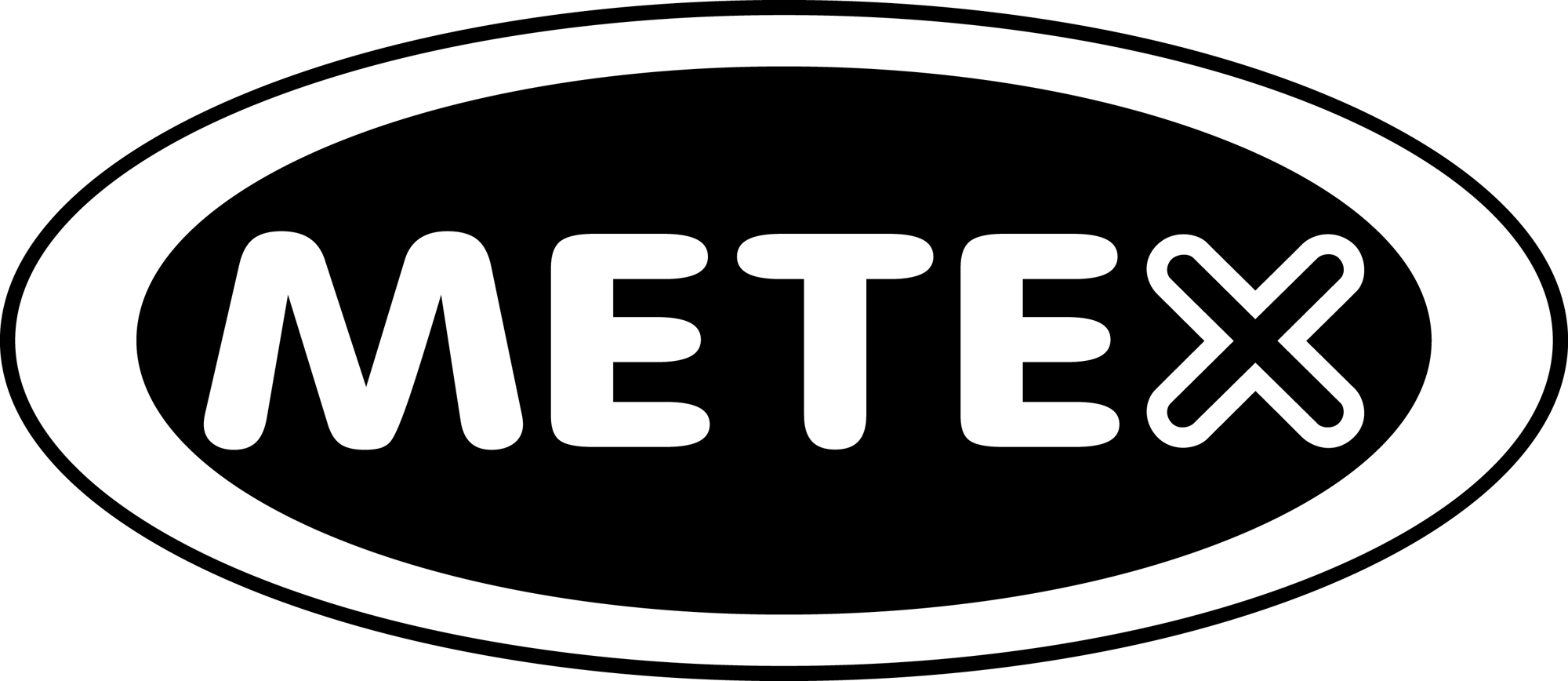
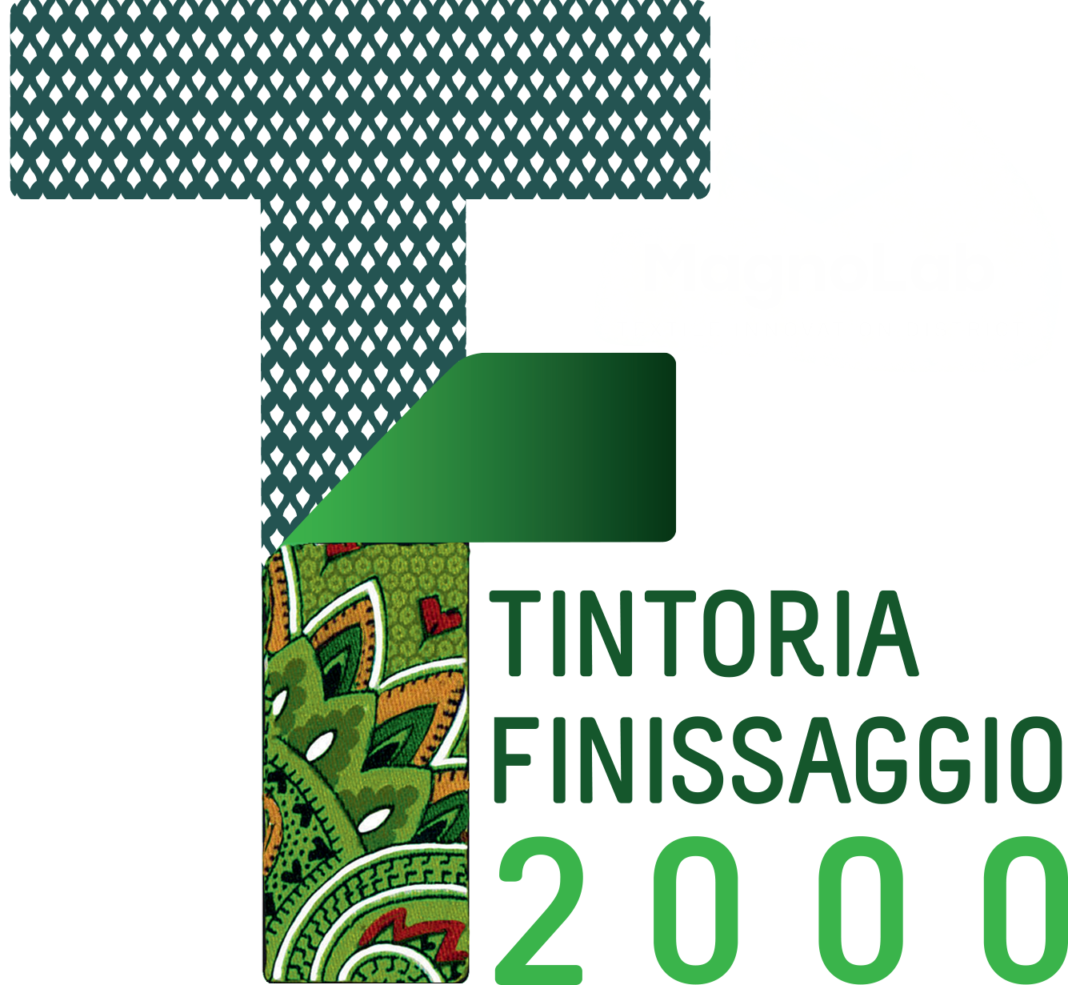
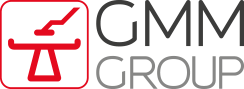
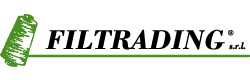
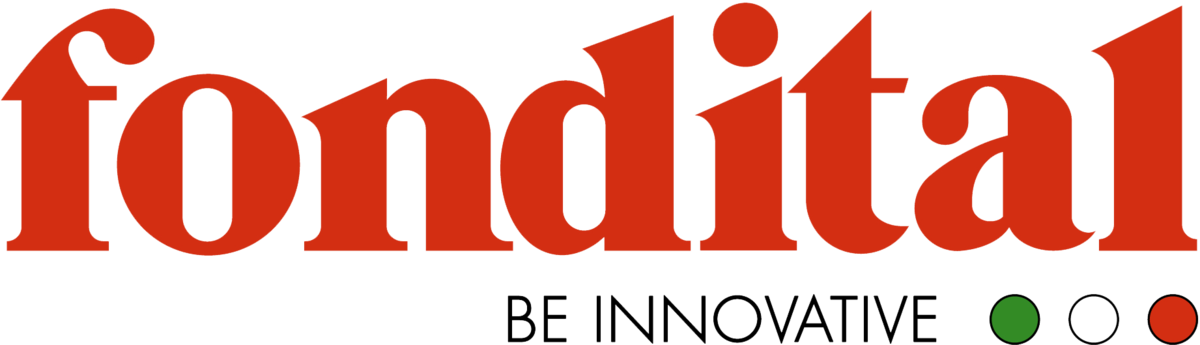
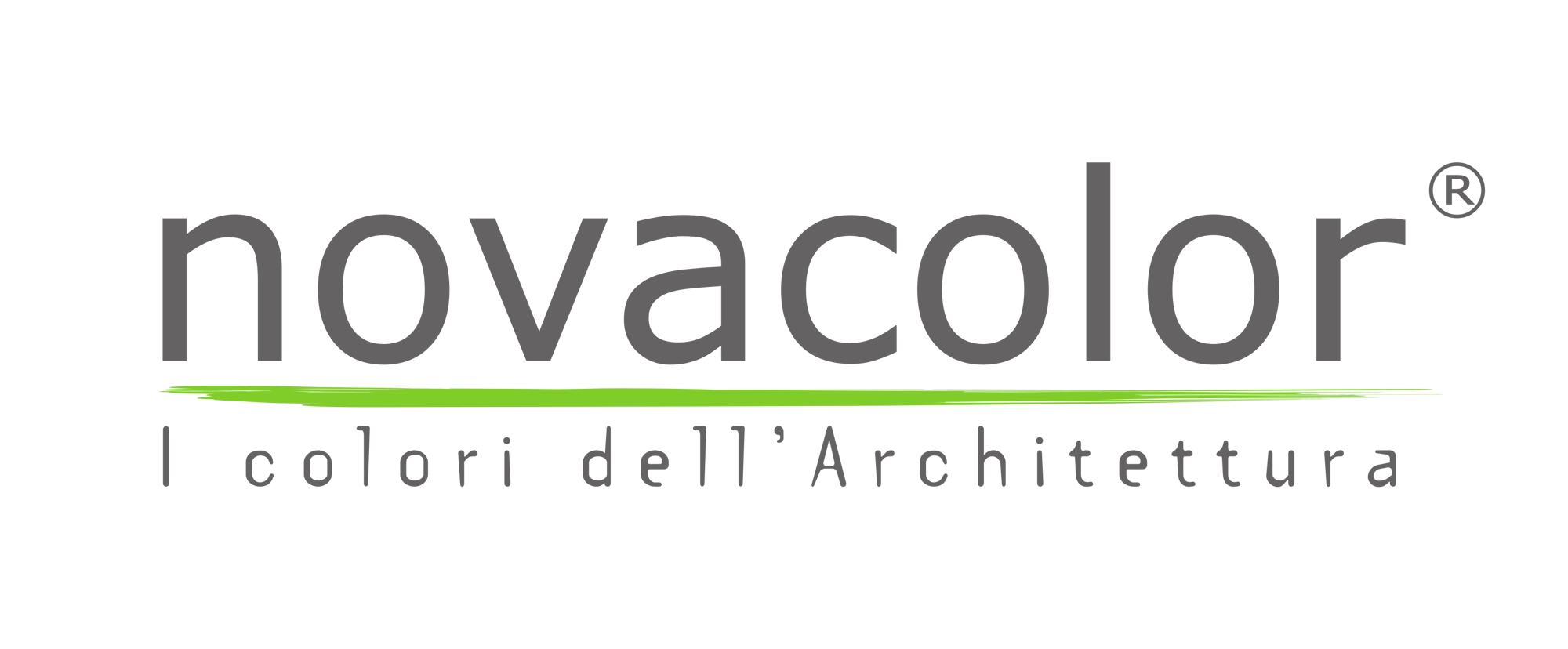

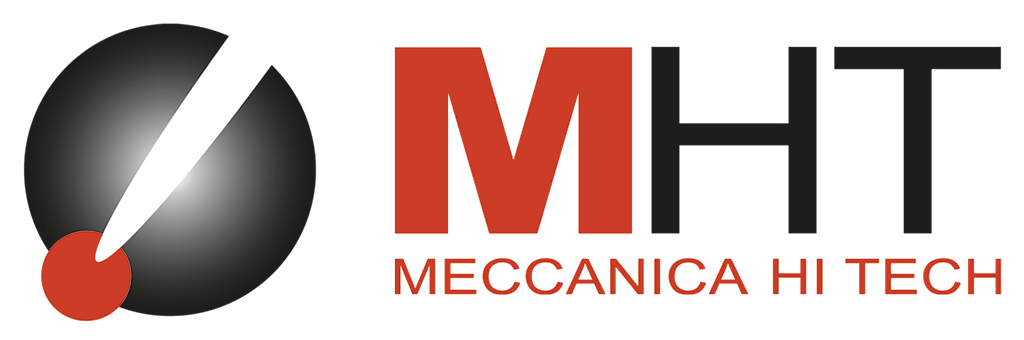
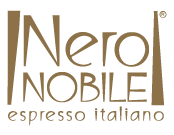

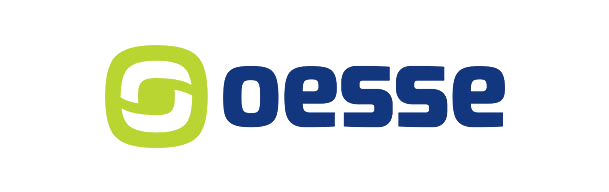

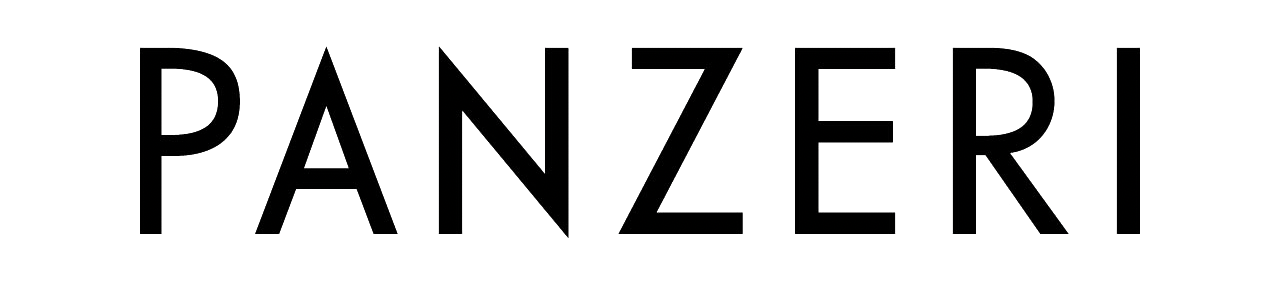
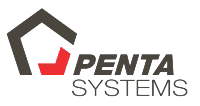
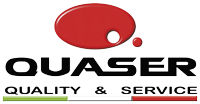
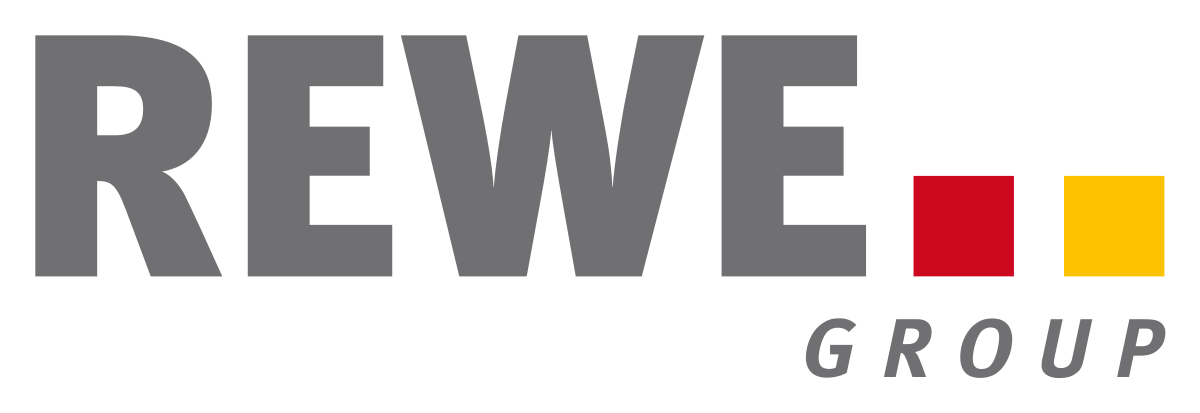
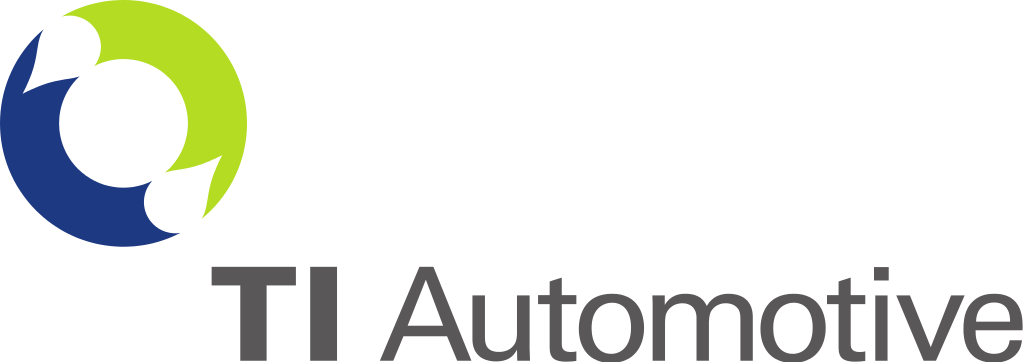

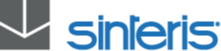
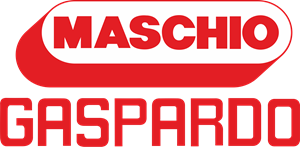
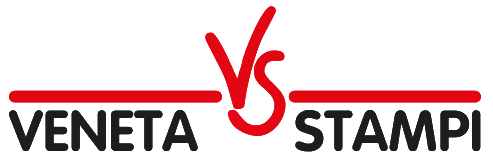
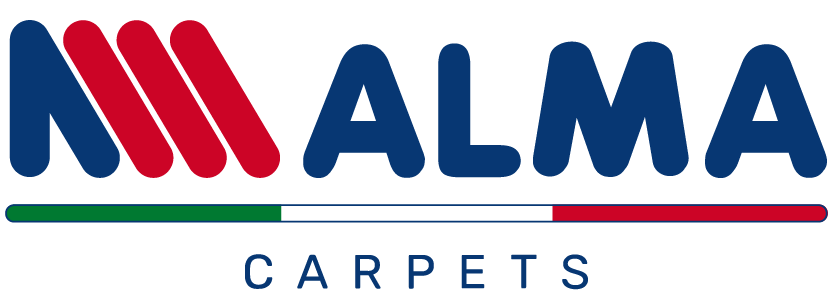
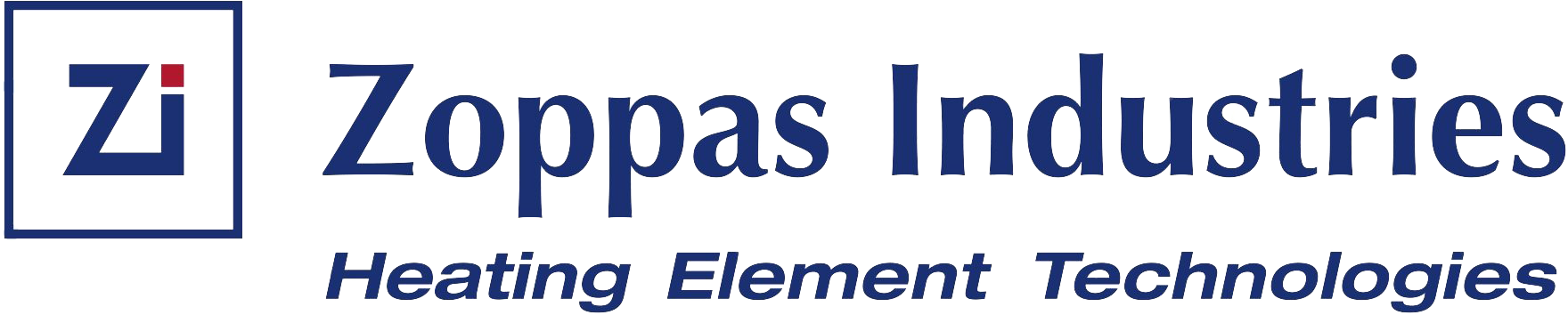
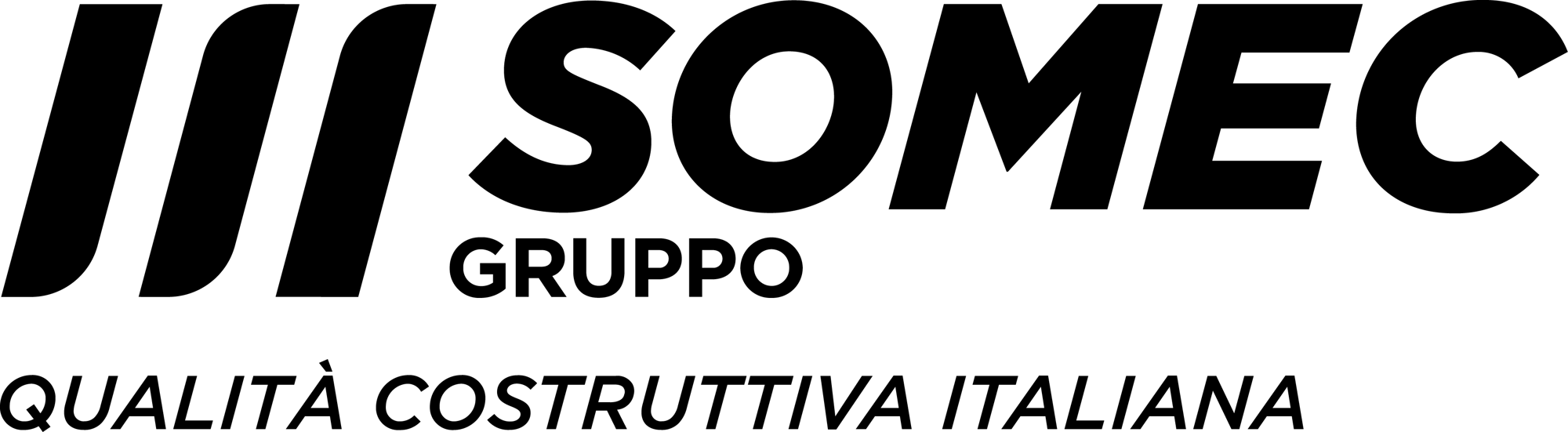

